Mipoxの装置製品のラインナップである「エッジポリッシャー」は、ポリエステルフィルム上に研磨砥粒が塗布されたテープ状の研磨フィルムを使用し、 半導体ウェーハのノッチおよびベベル面の研磨を行う「エッジ研磨装置」です。
従来の半導体ウェーハのノッチ・ベベル研磨工程で使用されている、砥石方式・スラリー方式の両方のメリットを兼ね備えた装置として、半導体ウェーハメーカーおよび再生ウェーハメーカーへ 200 台以上の納入実績を有しております。
目次

エッジポリッシャーによるウェーハエッジ研磨
独自の「研磨フィルム方式」によって、最終仕上げ工程前のパーティクル除去、エッジ部の面取り加工などに対応しております。
研磨フィルムの特性である柔らかさによって、研磨加工時におけるウェーハへの負担は少なく抑えつつ、エッジポリッシャーの柔軟な対応力によって、ご要望のエッジ形状と仕上げ面を実現します。
研磨フィルムをウェーハの研磨箇所に対して均一に充てることができるため、安定した研磨加工が実現できます。
[加工実績のあるウェーハ基板一例]
- Si(シリコン)
- SOI(酸化膜付シリコン)
- SiC(シリコンカーバイド)
- GaN(窒化ガリウム)
- GaAs(ヒ化ガリウム)
- AlN(窒化アルミ)
- LT/LN(タンタル酸リチウム/ニオブ酸リチウム)
- PZT(チタン酸ジルコン酸鉛)
ウェーハエッジ加工に求められる要件「ナイフエッジ形状の解消とデバイス面保護テープの除去」
半導体機能の向上を目的とした、ウェーハ薄化技術であるバックグラインド技術の進化に伴い、半導体ウェーハのエッジ部分にナイフエッジと呼ばれる鋭利な形状が多く発生するようになりました。
粗研削工程は、その加工処理時間を削減するために、比較的粗い砥粒を使用した砥石が選定されます。
その影響により、研削加工中の「ウェーハにかかる負荷」が増えることとなり、それは特にウェーハの薄い部分である「ナイフエッジ部」に集中します。その結果、エッジにチッピングやひび割れが発生し、ウェーハの破損へとつながってしまいます。
これを防ぐため、半導体のエッジ部分がナイフエッジ形状にならないように、事前に研磨加工等によって整える作業を行います。これを「ウェーハエッジ研磨加工」といいます。
ウェーハエッジ研磨には、ダイヤモンド砥石を使う研削方式や、ブレードを使用した切断方式等があります。それらはナイフエッジの形状は解消するものの、BGテープ(※)を除去することは不得意です。除去できなかったBGテープはウェーハに対し、負荷や破損を引き起こす原因となります。
※デバイス面保護テープ。バックグラインド加工を行う際にウェーハ反対面のデバイスを保護する役目を持つ。
Mipoxのフィルム研磨方式は、ウェーハ本体への負荷を最小限に、BGテープごと除去することが可能なため、それらの問題を解消することができます。
Mipoxのウェーハエッジ研磨加工「フィルム研磨方式」
「従来のプロセス(エッジ研磨無し)」
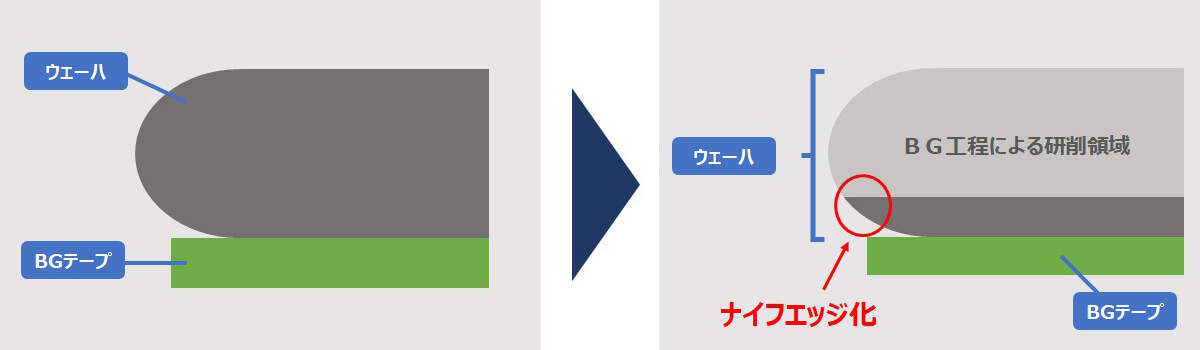
「Mipoxのウェーハエッジ研磨加工」
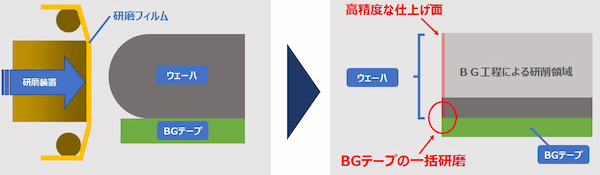
[BGテープ(デバイス面保護テープ)の粘着材やはみ出た部分を除去]
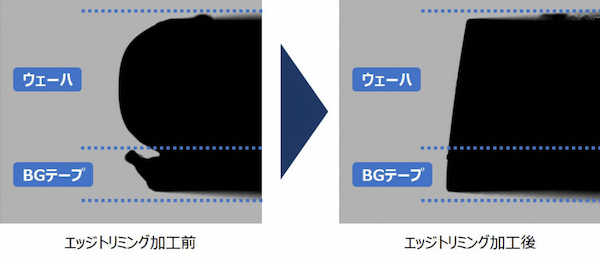
BGテープは粘着材がウェーハからはみ出やすく、それはウェーハ本体の破損の要因となるため除去することが求められます。
ウェーハエッジ加工に求められる要件「チッピングの除去による、ウェーハの割れ防止」
砥石等を用いた粗研磨加工、ブレードやレーザーを用いたくり抜き加工などにより発生する、ウェーハエッジ部のチッピングやひび割れを、Mipoxのエッジポリッシャーによって除去することが可能です。
これにより、ウェーハのハンドリング・搬送等の際のチッピングをきっかけとした割れの発生を防止することができ、歩留まりの向上、ウェーハ破損により発生するリスクなどを低減することができます。
[左:エッジトリミング無 右:フィルム研磨方式によるエッジトリミング有]
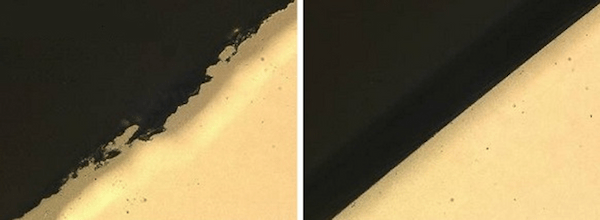
ウェーハエッジ加工に求められる要件「不要膜・不要物の除去」
Mipoxのエッジポリッシャーでは、ウェーハエッジ部に付着した、酸化膜などの表層膜の除去が可能です。
各基板に対し、繊細な表層(エピ)膜へ与える負荷を最小限に抑えることが可能な研磨フィルム方式によるエッジ脱膜加工によって、基板(下地)露出を行うことができます。
エッジミラー処理(鏡面化)も施すことが可能ですので、脱膜後エッジ部分へのパーティクル再付着防止、基板の強度向上・破損防止・歩留まり向上などの効果を付加することができます。
また、対象は膜に限らず、樹脂や金属系元素などの異物・不要物であっても可能です。
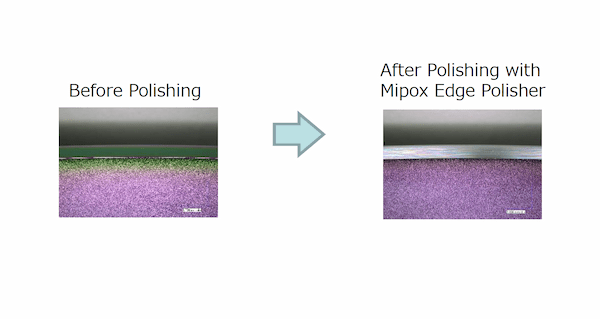
ウェーハエッジ加工に求められる要件「接合精度の向上」
Mipoxエッジポリッシャーを用い、ウェーハエッジ部の形状を作ったり鏡面レベルに加工したりすることで、ウェーハ接合の強度、歩留まり、接合精度の向上が期待されます。
また、接合加工後のウェーハに対し、エッジトリミングを行うことで、上層ウェーハと下層ウェーハのズレをなくすことも可能なため、ハンドリング時の破損防止効果を得ることができます。
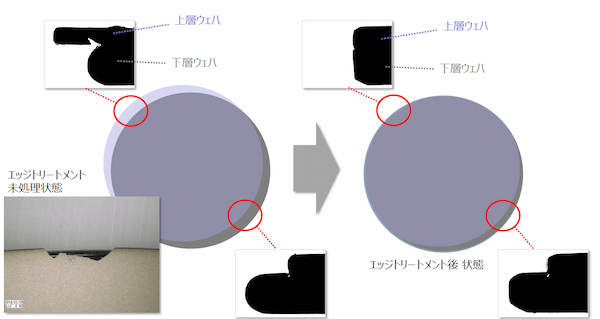
Mipoxエッジポリッシャー その他の特徴
環境へ配慮したノンケミカル加工
研磨加工に切削油を用いることはありません。 研磨フィルムと純水のみを使用した、環境を汚染しないノンケミカルの加工方式です。 そのため、加工後の洗浄処理、廃液処理が容易です。 化学処理等を必要としないため、それを適用するプロセスを問いません。
優れた形状コントロール性
ウェーハの強度を上げる目的で、エッジ部の形状をSEMI規格に沿って成形する、面取り加工を行うことができます。 エッジポリッシャー独自の研磨機構と、研磨フィルムの柔軟性の特徴を活かしたフレキシブルな加工により、ご要望のエッジ形状に仕上げることが可能です。
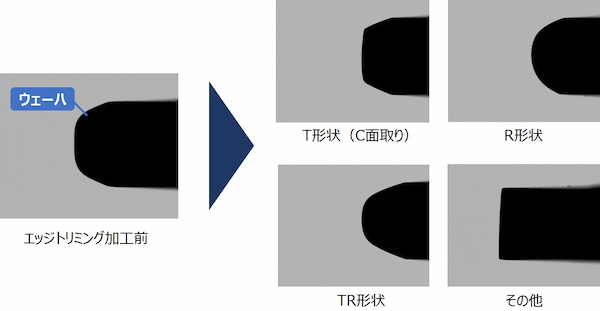
粒度・砥粒・パラメータ調整による幅広い加工能力の選択性
Mipoxでは研磨材総合メーカーとして、半導体用途によって異なるウェーハの素材に合わせた研磨フィルムを選定することが可能です。粒度は#400~#10000、砥粒はGC、Dなどからの選択が可能です。 これらに加え、エッジポリッシャー本体側による加工パラメータの調整により、幅広い加工能力の選択が可能となります。
[調整可能装置パラメータ] ・研磨時間 ・研磨角度 ・研磨パッド押付加圧 ・フィルム揺動幅 ・フィルム揺動速度 ・ウェーハステージのRPM ・研磨フィルムテンション ・研磨フィルムの送り速度
エッジ部CMP(スラリー方式によるエッジミラー工程)の負荷を大幅に軽減させる効果
スラリー方式は研磨力のレートが低く、膜種によっては除去に多大な時間を要します。 フィルム研磨方式は、スラリー方式と比較し、高い研磨力レートを有しているため、エッジ部CMPの前工程に導入することで、その後のエッジ部CMP工程での負荷を大幅に軽減させる効果が得られます。
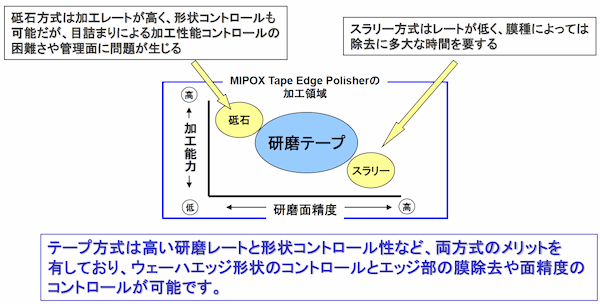
研磨フィルム送り方式による消耗品管理の容易さ、加工の安定性
エッジポリッシャーの研磨フィルムは Roll to Roll の方式で少しずつ、常に送られる形となります。
それにより、常に研磨テープの新しい面を使った状態で加工がおこなわれることになり、1Roll の使い終わりまで、研磨力が変わることなく、最後まで同じ条件で安定した加工がおこなわれます。
他の消耗品のように、目詰まりによる使用中の研磨力の変化に伴う加工性能コントロール調整等の管理に気を配る必要はなく、1Roll が使い終わったら交換するだけで、後は気を配らずとも常に同じ研磨結果を得られるため、管理が非常に容易です。
エッジポリッシャーが不得意な加工内容
エッジポリッシャーは柔軟性を持つ研磨フィルムを使用した、ウェーハへのダメージが少ない「倣い研磨」が特徴となります。
倣い研磨はウェーハの形状に沿う形(倣う)での研磨方式です。
そのため、ウェーハ外径を1mm単位でサイズダウンするような研磨力が必要な加工であったり、ウェーハ形状が一定になるように加工をする(真円でないものを真円にしたいなど)といった加工には不向きな装置となります。
Mipoxエッジポリッシャー ノッチ研磨
3㎜幅の研磨フィルムを、研磨ヘッドに取り付けて、5.0N~10.0Nのテンションを掛ける。
研磨ヘッドが上下に動き、ヘッド角度や研磨時間は調整することができる。
(研磨ヘッド角度の可動範囲: +/-62度)
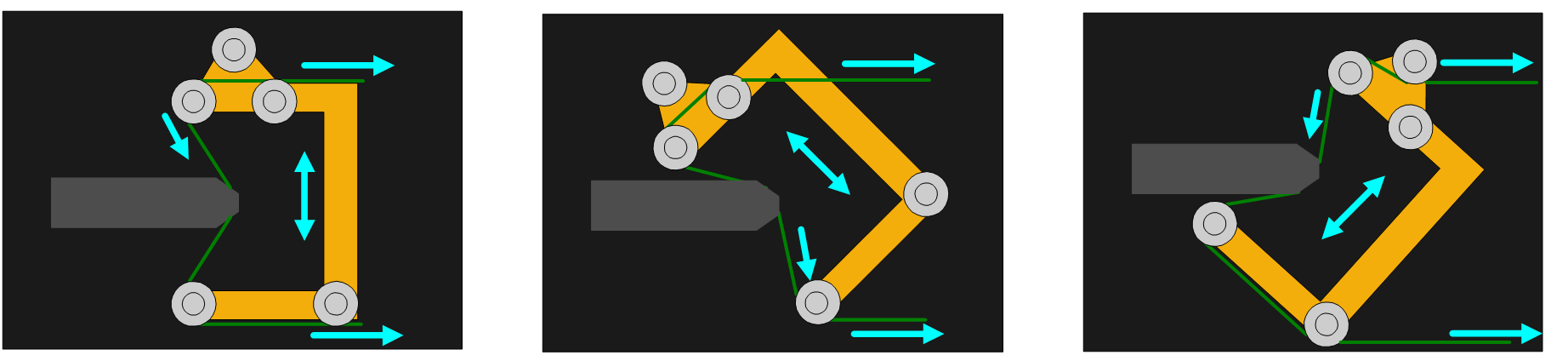
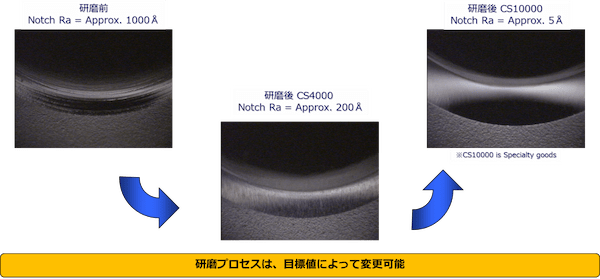
Mipoxエッジポリッシャー ベベル研磨
ウェーハを回転させ、外周部に研磨フィルムを当てることで研磨する(ヘッド圧力 5N~15N)。
研磨ヘッド角度と研磨時間は調整可能(研磨ヘッド角度の設定範囲: +/- 79 degree)。
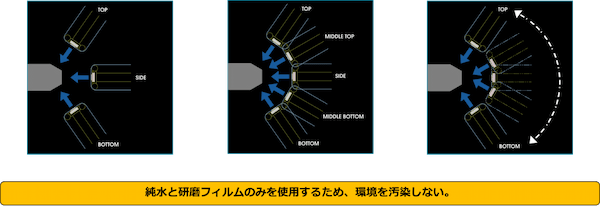
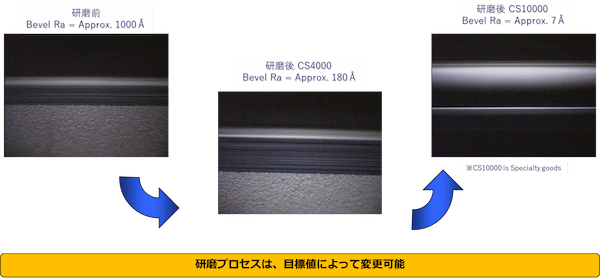