金属加工分野で一般的なフライス加工と研磨紙による仕上げ加工の表面状態とパラメータについて解説します。
フライス加工
フライス盤加工とは
金属加工でごく一般的な加工にフライス盤加工があります。
フライス盤加工は大別すると正面フライス加工と平フライス加工の2種類に分かれます。フライスはいずれにしてもチャックに加工材を固定し、材料に対して切削加工を行うことで加工を行っていきます。このため、材がチャックで固定できることが前提の加工方法となります。
磁石チャックであれば材を磁力で固定できることが前提ですし(非磁性材料やあまり小さいものは加工できない)、通常のチャックもある程度の厚みがあり、つかめて加工中に変形しないことが前提となります。加工材が大きくなるとどうしてもチャックが大きくなるため、大型のフライス加工では設備投資のイニシャルコストがより必要になります。また近年は、NC工作機械による自動化・省力化が一般的になっています。
フライス加工の種類
●正面フライス加工
正面フライスはフェイスミルを使用して広い面積を切削していきます。金属加工で形状を作る際には最も一般的です。正面フライスは特徴的な研削痕が残るので、この研削痕も金属加工製品らしさがあって趣があります。
●平フライス加工
フライスと言えば正面フライスが一般的なのであまりなじみはないかもしれないですが、平フライス加工というものもあります。回転軸が正面フライスは加工面に対して垂直ですが、平フライスは並行に回転する横フライス盤を使用します。正面フライスと比較すると加工速度に優れますが、面がどうしても荒れるので荒加工に使用されます。
●エンドミル加工
正面フライスとほぼ同じですが、エンドミルという工具を使います。加工面積が小さいので加工に時間がかかります。
研磨加工
研磨加工とは
研磨加工にはハンドツールから専用の研磨装置までさまざまな形態があります。ハンドツールであれば数万円程度の投資でさまざまな加工が可能ですし、ワークのサイズや形状・性質もほぼ選びません。ただし、形状加工には不向きですし、形状制御についてもハンドツールの場合は作業者の腕に左右されます。専用の研磨装置を使用するとしてもやはり形状加工には不向きで、おおむね表面の加工や表面の状態を改善することに力を発揮します。
研磨加工の種類
●サンダー研磨
ダブルアクションサンダーが一般的です。おおむねマジックテープ加工を施した研磨紙や研磨フィルムをサンダー(雷Thunderではなく砂のSandの方です)に付けて研磨を行います。
ダブルアクション・シングルアクション・ランダムサンダーの三種類が市場では一般的です。
ダブルアクション | シングルアクション | ランダムサンダー | |
---|---|---|---|
研磨力 | ○ | ◎ | △ |
使いやすさ | ◎ | △ | ◎ |
表面状態の良さ | ◎ | 〇 | ◎ |
ダブルアクションサンダーは内蔵されているオービットダイヤによって差が出ます。オービットが大きいと研磨性が上がり、小さくなると表面状態が良くなります。これは、同じ回転数でもオービットが大きいと動作距離(振幅)が大きくなるからです(同じポンプでも東日本の50Hzと西日本の60Hzでは流量が違うのと同じですね)。
弊社では2種類のダブルアクションサンダーをご用意しています。研磨力に優れた9mmオービットのGoQサンダーと、表面仕上げ状態重視の3mmオービットのプレトップサンダーです。どちらもお客様からご好評をいただいています。
●ベルト研磨
ベルト研磨は一般的にベルトサイズによってワイドベルト、ナローベルト、小物ベルトの3種類に大別されます。
ワイドベルトはおおむね大面積の平面研磨に使用されます。ナローベルトはさまざまで、基材の柔軟性で向き不向きが出ます。一般的な鉄鋼材料に対しての重研削ではしっかりとしたXウェイト基材が、軽金属や小物の曲面加工などでは柔軟なJウェイト基材が一般的です。特にベルト研磨は研磨加工では最も研磨性能(=加工能率)が高くなっています。
●平面研削盤加工・両頭グラインダー加工
平面研削盤では丸いロールを使用して研磨加工を行います。例えば、研磨布をフラップ状に並べて金具で押さえたフラップホイール(弊社NPホイール)や、不織布を成型加工した不織布ホイール(NLなど)などです。
ロール状の製品を回転させて素材を削っていくので、前述の平フライスに近い加工になります。もっとも、平フライスではミルが剛体に近いので荒加工向きとなるのに対し、これらの研磨製品群はどれも柔軟なため、平フライスと比較すると仕上げ前などの作業に向いています。
●ディスクグラインダー加工
ディスクグラインダーで使用される研磨材は金属ブラシ・研磨ディスク・ダイヤモンドカッター(は研削ですが…)などが一般的です。ハンディツールの中では最も研削力があり、回転数も高いため安全性が最も重要とされます。弊社で製造している研磨ディスクは、主に船舶の製造中に発生する溶接ビードなどを削り取るような豪快な粗加工工程に使用されます。
研磨紙では比較的細粒度で評価いただいている弊社ですが、ディスクグラインダー用途の研磨ディスクでは14番などの砂粒サイズの研磨材を使用しています。
表面パラメータについて
三角記号
▽の数で表面の粗さを規定しています。何となくの感覚で分かるので今でも現役で図示表示されていることが多いです。また、ぱっと見て分かりやすいので特に表面状態がそれほど精密でなくてよいのであれば逆に分かりやすいです。1952年のJIS規格で制定されています。
表記 | 表面状態 | Ra換算数値 |
---|---|---|
▽ | 荒仕上 (切断加工レベル) | 25μm以下 |
▽▽ | 並仕上げ (切削・フライス) | 3.2~6.3μm |
▽▽▽ | 上仕上げ (切削でも細かい仕上げ) | 0.4~1.6μm |
▽▽▽▽ | 精密仕上げ (研磨仕上げ) | 0.2μm以下 |
Ra(算術平均粗さ)
表面状態のデコボコをすべて凸とみなして単純平均した数値です。現在最も使用頻度が高いパラメータです。筆者の感覚だとPCB関連では下表のような感じになります。
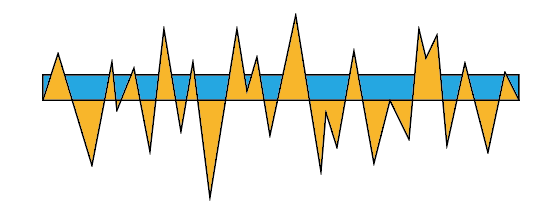
Raの数値 | 状態 |
---|---|
10μm以上 | 粗番手での形状加工などで見るレベル |
1~10μm | 粗粒度での研磨加工 |
0.5~1μm | 中粒度での研磨加工湿式研磨であれば120~320番程度 |
0.1~0.5μm | 精密加工レベル 白ボケした感じ 密着性はこのくらいが良い |
0.05~0.1μm | 準鏡面レベル 顔が写る程度 1200~2000番レベル |
0.05μm以下 | 鏡面加工レベル 2000番より細かい粒度 |
Rz(旧Ry)
現在はRa使用頻度が最も高いのですが、2002年のJIS改定以前まではRz(Ry)を最も重要視されるお客様が多かったように記憶しています。内容としては最大高さ粗さ、といい、評価単位内の最も高いところと低いところの合計の平均です。
具体的には深いスジ(スクラッチ傷)があると、そこから製品欠陥になったり、後工程でスクラッチを磨いて消すことが困難になることから現在でも重要なパラメータです。
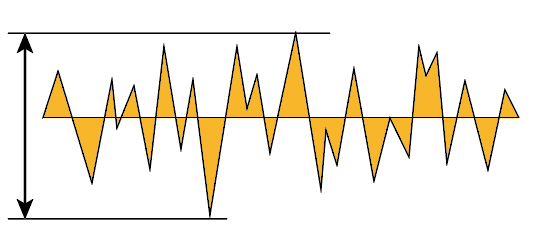
Rpk・Rvk
筆者が特に興味深く見ているパラメータです。Rpkは突出山部高さ、Rvkは突出谷部深さといいます。エンジンシリンダーなどの摺動材料などでは、Rpkは初期摩耗(つまり慣らしが早くあがるかどうか)、Rvkは油切れ耐性に効果があると伺っています。Rvkは前述のスクラッチの全体量にもつながるので、用途によっては注視するべきパラメータです。

RSm
研磨加工後には必ず山と谷がセットで発生します。この山谷セットの長さの平均がRSmです。細かくなればなるほど細かく研磨されていると見られます。
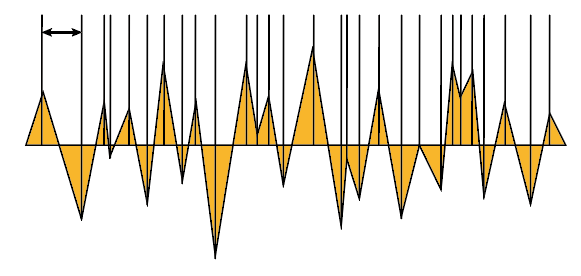
フライス・研磨紙加工の特徴と表面状態の比較
実際のフライスと研磨加工の状態を確認していきましょう。それぞれ50倍の顕微鏡写真と粗さ曲線です。
○正面フライス
![]() 正面フライスの50倍の顕微鏡写真
|
![]() 正面フライスの粗さ曲線
|
○平フライス
![]() 平フライスの50倍の顕微鏡写真
|
![]() 平フライスの粗さ曲線
|
![]() 研磨加工の50倍の顕微鏡写真
|
![]() 研磨加工の粗さ曲線
|
どれも標準試験片のRa1.1μmの状態ですが見た目も表面プロファイルも大分異なることが分かります。加工によって表面状態が大きく変わることがご確認いただけたと思います。
正面フライス | 平フライス | 研磨加工 | |
---|---|---|---|
Ra | 1.1106μm | 1.1084μm | 1.1621μm |
Rz | 3.9768μm | 4.8984μm | 10.0028μm |
RSm | 60.0482μm | 690.6445μm | 71.7458μ |
Rvk | 0.7766μm | 0.3317μm | 1.7392μm |
いずれの加工方法も、加工して終了ではなく、この後に仕上げ加工や塗装・加飾などの工程に進むと考えられます。この際の次工程に合わせた加工方法をご検討いただくのが最善と考えます。
まとめ
本稿では加工方法と各パラメータについて、概要ですがご説明しました。お客様の加工と、後工程の重要視するパラメータを理解することで、よりお客様自身の顧客満足度の向上のための参考となれたのであれば幸いです。