はじめに
デジタル社会の発展とともに、ディスプレイ技術への要求は年々高度化しています。特に有機EL(OLED)ディスプレイは、その優れた画質、薄型設計、フレキシブル性により、スマートフォン、テレビ、車載ディスプレイなど幅広い分野で急速な普及を見せています。 この革新的な表示技術の中核を担うのが、透明電極として機能するITO膜(インジウム・スズ酸化物膜)です。ITO膜の品質は、OLEDディスプレイの性能を左右する重要な要素でありながら、その製造プロセスには技術的課題が存在します。
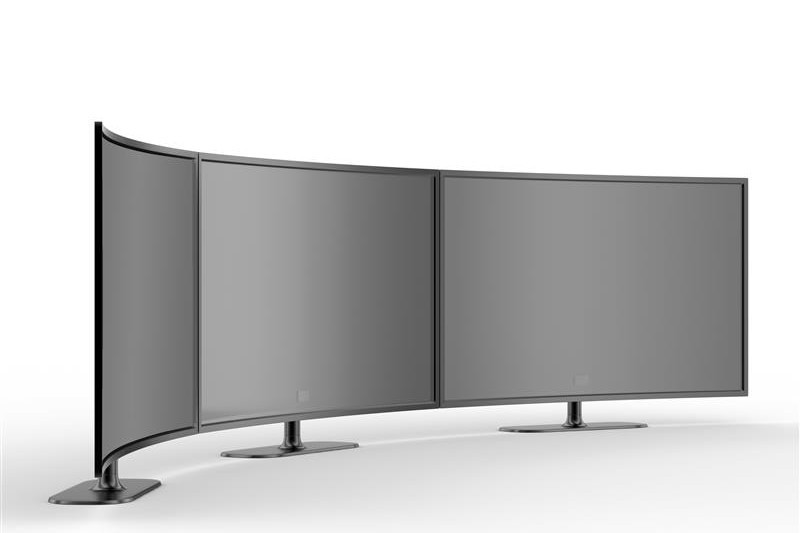
本稿では、ITO膜の技術的特性と業界が直面する課題を詳細に分析し、Mipoxが開発したDry方式・ケミカルフリーのITO膜研磨技術が、いかにしてOLEDディスプレイの性能向上に貢献するかを検証してまいります。
OLED構造におけるITO膜の戦略的役割
OLED素子は、基板上に複数の機能層を精密に積層した構造体です。正孔輸送層、発光層、電子輸送層がサンドイッチ状に配置され、その最下層に位置するITO膜が陽極として重要な役割を担っています。 ITO膜の主要機能
- 透明電極としての機能 可視光に対して高い透過性を維持しながら、電流を効率的に供給する双方向性能を実現しています。
- 正孔注入機能 陽極として正孔輸送層へ電荷を適切に注入し、発光反応の起点となる電気的環境を提供します。
- 光学的透過機能 発光層で生成された光を外部へ効率よく導出し、ディスプレイとしての視認性を確保します。
これらの機能の最適化により、OLEDパネルの輝度、色再現性、消費電力効率が大幅に向上し、最終製品の競争力向上に直結します。
ITO膜の技術的課題と産業界の対応
1. 材料供給の構造的課題 ITO膜の主要構成要素であるインジウムは希少金属であり、地政学的リスクと価格変動が製造コストに大きく影響しています。安定した供給体制の確保は、OLED産業全体の持続可能な発展において重要な課題となっています。 2. フレキシブル性の物理的制約 ITO膜は本質的に脆性材料であり、機械的応力に対する耐性が限定的です。折り曲げ可能なフレキシブルOLEDの実現においても、この特性は技術的なボトルネックとなっています。 3. 表面形状の制御課題 スパッタリング法などの成膜プロセスにより形成されるITO膜には、微細な突起構造や表面粗さが不可避的に発生します。これらの表面不均一性は以下の問題を引き起こします。 • 発光ムラの発生 - 電流密度の不均一分布による輝度バラツキ • 電流集中現象 - 局所的な電流集中による素子劣化の加速 • 製品寿命の短縮 - 電気的ストレスによる長期信頼性の低下
精密研磨による表面最適化の技術的意義
表面形状の課題に対するソリューションとして独自の精密研磨技術を開発しました。 高精度研磨フィルムと専用装置によるDry研磨方式により、ITO膜表面を理想的な平滑性まで改善することが可能です。
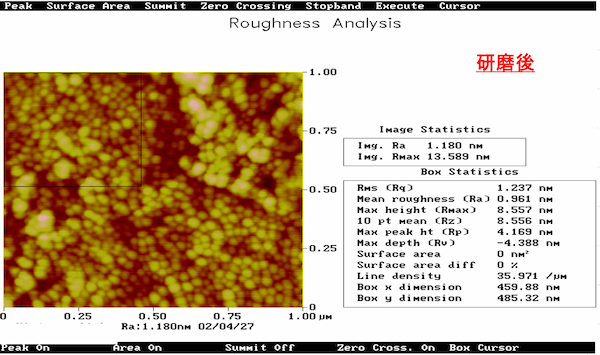
研磨処理による性能向上効果
- 電流ロスの最小化 表面平滑化により電流経路が最適化され、発光効率が大幅に向上します。
- 積層品質の向上 均一な表面状態により、上層の有機材料との密着性が改善し、製造歩留まりが向上します。
- 電圧応答の安定化 一様な電流分布により、輝度と色再現性の安定性が確保されます。
Mipoxの技術ソリューション
平面研磨装置「NMH-400」の技術仕様
- Dry研磨方式の採用 化学薬品を使用しないドライプロセスにより、環境負荷を最小限に抑制し、廃液処理コストを削減しています。
- 運用効率の最適化 装置構造のシンプル化により、操作性と保守性を両立し、生産現場での運用効率を向上させています。
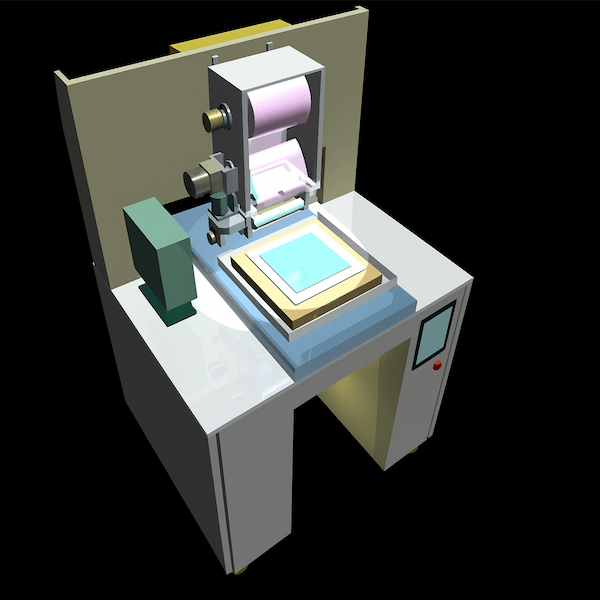
- 高速処理能力 30秒以内のタクトタイムを実現し、量産ラインへの適応性を確保しています。
研磨フィルム「AWA10000-25」の性能特性
- 表面粗さ改善実績 • 算術平均粗さ(Ra):2.16nm → 0.96nm • 最大高さ(Rz):14.5nm → 8.5nm
- 発光効率の顕著な向上 研磨処理により、ルミナンス効率が定量的に改善され、エネルギー効率の向上が実現されています。
- スクラッチレス加工技術 球状アルミナ粒子の採用により、パネル表面への損傷を完全に回避し、高品質な仕上がりを保証しています。
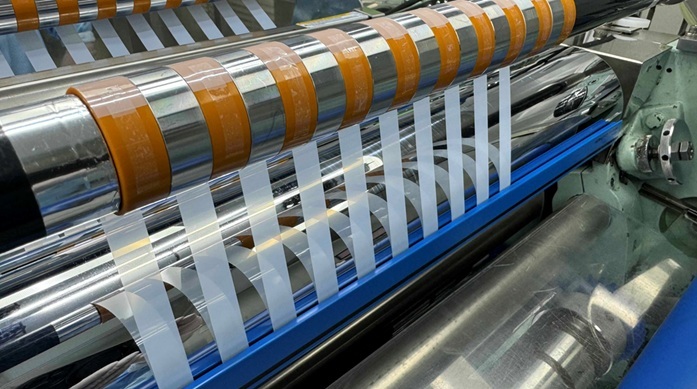
実証データと導入実績 実機検証において、Dry研磨を施したOLEDパネルは、高電圧領域においても効率低下が効果的に抑制され、安定した発光性能を維持することが確認されました。 複数メーカーのパネルを用いた比較評価では、未研磨パネルにおける発光効率の不安定性が明確に示され、研磨処理の有効性が定量的に実証されています。これらの結果は、Mipoxの研磨技術が産業レベルでの品質向上に確実に貢献していることを示しています。
代替材料の動向と将来展望
次世代透明電極材料
- FTO(フッ素ドープスズ酸化物) 優れた耐熱性と製造コスト削減の可能性を有し、特定用途での採用が進んでいます。
- ZnO系材料(AZO, GZO) 高い導電性と透明性を両立し、ITO代替材料として有望視されています。
- 先進的有機・ナノカーボン系材料 導電性ポリマーやグラフェンなど、フレキシブル性に優れた新材料の研究開発が活発化しています。 市場動向と技術的位置づけ 現在の商用OLEDパネル市場において、ITOは依然として主流の透明電極材料として位置づけられています。代替材料の開発が進展する中でも、ITOの品質最適化を目的とした研磨プロセスは、製品競争力の維持・向上において不可欠な技術として今後も重要性を増していくと予測されます。
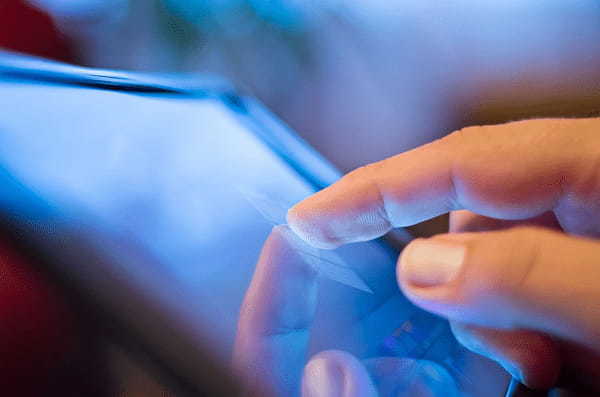
結論
ITO膜は、OLEDディスプレイ技術の発展において中核的な役割を担う一方で、材料特性や製造プロセスに起因する複合的な課題を抱える重要な技術要素です。 Mipoxが提供する環境配慮型の研磨技術は、これらの課題を効果的に解決し、OLEDディスプレイの性能と信頼性を向上させるソリューションとして評価を受けています。 持続可能な技術発展を目指すMipoxは、今後も「塗る・切る・磨く」の中核技術を基盤として、次世代ディスプレイ技術の進化に貢献し、産業界の発展に寄与してまいります。