異なる素材を接合する 「異種直接接合技術」~セラミック材料に注目して~
2つ以上の材料を溶接工法や接着剤を使用せずに結合させる「接合技術」は、半導体など精密機器から自動車、航空機向けに至るまで様々な分野で適用されている重要な技術です。 特に、異なる材料を接合する「異種材料接合技術」は、一つの材料では出せない優れた物性・性能を有する新たな複合材料を生み出します。
本稿では、異種材料接合分野で近年、特に多くの期待が寄せられている「セラミック材料(焼結体・多結晶材料)」に着目し、同材料向けにMipoxが開発したセラミック材料向け高精度研磨加工技術について、紹介します。
目次
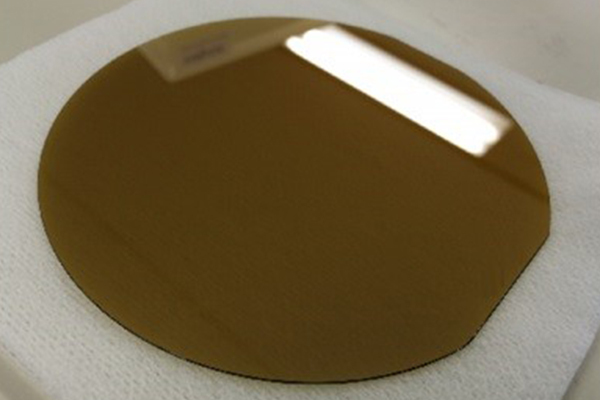
異種材料接合において重要な「表面粗さ」について
異種材料接合は構成される元素の結合メカニズムによって3つの分野に分けられ、解決したい課題や用途・目的に合わせて、各分野の材料より最適な接合方法を適用します。
- 金属材料
- 高分子材料
- セラミック材料
固相接合に分類される原理で材質的結合を促し、共有結合・イオン結合・金属結合の結合力で接合させるメカニズムは一見簡単に見えるかもしれません。
しかし、材料表面には接合を阻害する汚染物質や、吸着ガスなどが存在するため、表面原子同士が繋がりにくく、必要とする接合強度を得るのが難しいなど、実際は多くの問題を抱えている場合が多くあります。
理想的な接合界面を得るための表面洗浄処理や、異種材料間を繋ぐ結合手を形成する表面活性化処理は接合技術の基本なのですが、まずは接合に必要な「表面粗さ」を満たしている事が前提となります。
また、物体を固体のまま接合する固相接合は、溶融が発生するろう接など他の接合方法と比較した場合、数nm程度のごく僅かな凹凸であっても接合不良の原因となる事が多いです。
接合品質を左右する材料表面のぬれ性や、接合強度を司る表面損傷効果やアンカー効果などは材料の表面粗さに依存するとされており、可能な限りその値を小さく抑える事が品質向上には欠かせません。表面粗さのコントロールは、用途や材料に限らずラッピングやポリシング等の研磨加工によって行われる事が一般的です。
異種材料接合の主要分野とセラミック材料接合時の問題点について
異種材料接合の大きな市場の一つと言えるのが半導体・MEMS分野です。
近年まで高温加熱を伴う陽極接合が一般的でしたが、異種材料間の熱膨張の差による影響や高温環境で発生するガスの問題が避けられず、用途が限られた状況が続いていました。
常温、または低温条件下での接合を実現出来ればそれを回避する事が出来ます。異種材料接合においては下記3点が特に重要な要素となります。
- 今まで以上の高精度な表面粗さ・平面度を持った材料
- 材料間の熱膨張係数が近い
- 収縮の挙動が近しい物性を持つ材料を選定・適用
異種材料接合見合うセラミック材料が各メーカーによって開発・試作されており、既にリリースされている材料も多くあります。
しかしながら、熱膨張係数・収縮挙動を調整するために加えるフィラーの影響により結晶粒界段差(凹凸)が顕著に発生してしまう材料が多く、通常の研磨加工では接合に耐える表面を得られないのが一般的でした。
次世代半導体基板として期待された新材料(新素材)が、研磨加工技術の未達・表面粗さを満たせないという理由でNGとなりその進化を妨げていました。
Mipoxが開発した「セラミック材料に対する高精度研磨技術」は、それまで接合に用いる事が出来なかった多くの常識を覆し、多くの課題・問題を解決してきました。
車載用~電力向けまで広範囲にわたるSiCパワーデバイス、高輝度LED、医療用デバイス、通信用デバイスなど(高周波・表面弾性波フィルター・シリコンフォトニクス等)、次世代を担う半導体用途に対して大いに貢献している技術であると自負しています。
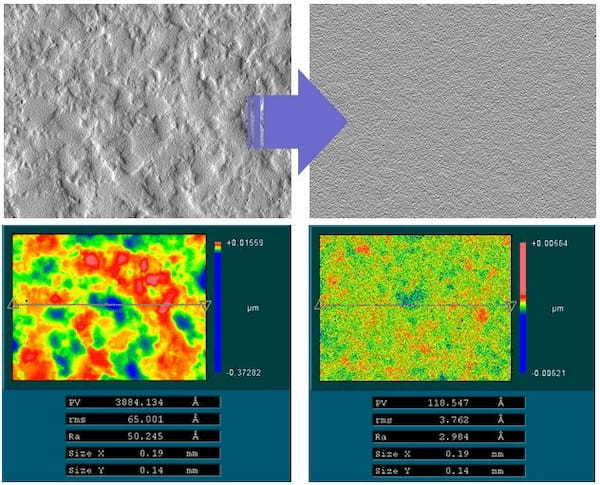
加工例と課題に対するソリューション
Si3N4(窒化珪素)/AlN (窒化アルミニウム)セラミックスの加工例
環境負荷低減を目的とした電動化は自動車だけでなく航空機にも波及しており、それに用いられるSiCを主とする化合物半導体を使用した次世代パワーデバイスのニーズが高まっています。SiCパワーデバイスは、従来のSi デバイスと比較して高耐圧かつ低損失を達成し高周波・高温動作を 可能にしました。
しかし、それを用いたパワーモジュールは高温環境下での動作を強いられる事になり、熱対策、特に接合部・接続部などのヒートシンク機構(放熱機能)の改善が要求されるようになりました。
一般的なパワーモジュールはデバイス(チップ)で発生した熱を効率良く冷却出来るよう、はんだや絶縁基板、熱伝導グリスをなどを使用し、チップを動作保証温度以下に保つよう設計されています。
しかし、動作保証温度の上限が150℃程度とされているSiデバイスと比べSiC デバイスは300℃近い温度で使用する可能性があり、融点に迫りつつあるはんだの代替や放熱機構の設計を根本的に変えなければSiCデバイス本来の性能を生かすことは出来ません。
課題に対するソリューション
その解決策として期待されているのが、銅材とSi3N4またはAlN焼結体(セラミック)の接合で構成された直接接合で構成された基板です。
Si3N4やAlNは通常の研磨加工(CMP)ではセラミック基板の結晶粒界(グレイン)の影響で表面が大きく荒れるため、接合相手となる銅材との接触面積が限られ十分な接合強度や熱伝導率を得られませんでした。、その結果、超音波接合等の際に必要な接合エネルギーによって基板が破損する等の問題を抱えていました。
しかし、高精度研磨加工によって達成された平滑な表面を達成した同基板は、良好な熱伝導特性を示し低い接合エネルギーで充分な接合強度を得る事が可能となったため、はんだを用いることなくSiCデバイスの高熱に耐える放熱特性を有するパワーモジュールの可能性を見出しました。Si3N4、AlN共に放熱特性に有利なより薄い形状での接合実現を目指し、試作・開発が行われています。
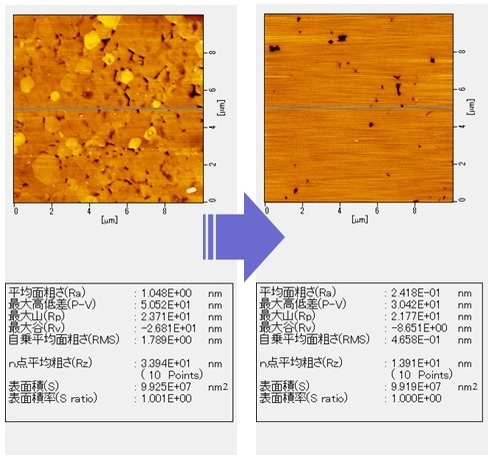
単結晶SiCの接合を目的としたセラミック材料高精度研磨加工事例
パワーデバイス用途を中心に流通量が増加している単結晶SiC基板ですが、高コストにより、市場形成に至っていないのが現状です。Mipoxでは、セラミック基板に単結晶SiC基板を接合し、必要層を残し剥離する事で高価な単結晶SiC基板の使用量を抑制することが可能です。これにより、コスト低減を狙う工法に適用されている平坦化処理(結晶粒界段差の平滑化)においても、Mipoxがその一躍を担っています。
この工法においてはセラミック材料側の表面粗さ及び平面度はもちろん重要となりますが、選定の時点で、単結晶SiC基板が良質な種結晶から作られ欠陥が少ないもの、かつ基板製造プロセス中に生じた加工による歪が極力少ない高品質な基板を選定する事が非常に重要になります。
基盤内部歪可視化装置「XS-1」
Mipoxは偏光顕微鏡の原理を応用し、大型放射光施設の観察に匹敵するあるいは 、それ以上の精度・情報を得られる観察精度を実現し、自社開発の基板内部歪可視化装置「XS-1」をこの用途に適用しています。これによりSiC単結晶基板に対しあらかじめ欠陥箇所のマッピングを行い、本工法の効果(コストダウン・歩留まり)を高める対策を行っています。もちろんセラミック材料との接合に適した単結晶SiCの研磨加工(CMP)も対応しています。
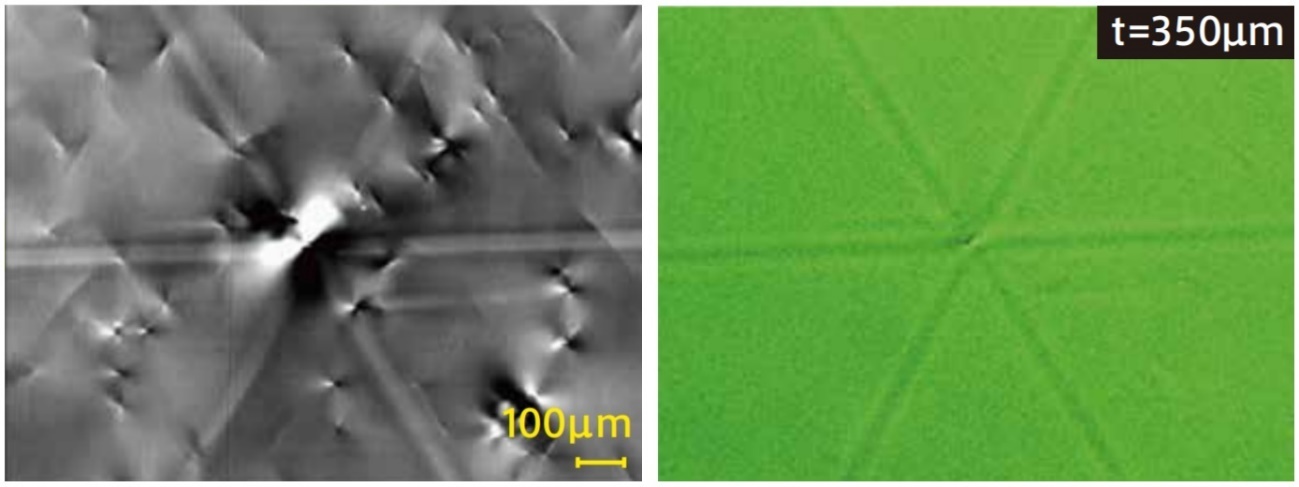
先進パワー半導体分科会 第3回講演会 ポスター講演P-35(2016年、つくば国際会議場)偏光顕微鏡を用いた複屈折観察による半導体単結晶基板の結晶転位の評価 竹中研介1、加藤智久2、松永達也2、武井 学1、米澤喜幸2、奥村 元2 (1富士電機株式会社、2国立研究開発法人産業技術総合研究所)
高機能セラミックとして期待される材料に対する加工例
Al2O3(酸化アルミニウム)とY2O3(酸化イットリウム)の複合酸化物(YAG)とAl2O3の複合セラミックス材料は、耐熱性に優れる固形蛍光体として高輝度LED照明向けの用途に使用されています。
耐熱温度は1700℃程度とされLED照明用で一般的な樹脂製蛍光体の150℃程度と比較すると大変優れた耐熱性ですが、研磨加工に対する各相の特性が真逆の挙動を示すため平滑な研磨面を得る事が困難な代表的な材料です(Mipoxの高精度研磨加工事例を図5に示します)。
特に、ガーネット焼結体は、レーザーや光学素子用途等への応用が期待されている「透明ナノセラミックス」の一種として最近取扱いが急増している材料であり、Mipoxの研磨加工技術(CMP)が有効な材料の一つです。
さらに、各セラミックス材料や、Si・GaAsなどの半導体基板との接合を目的とした、Auを筆頭とするAl・Cu・Ag・Ni・Ti・Snの金属材料についても対応しており、医療用デバイス向けを中心に多くの実績を有しています。
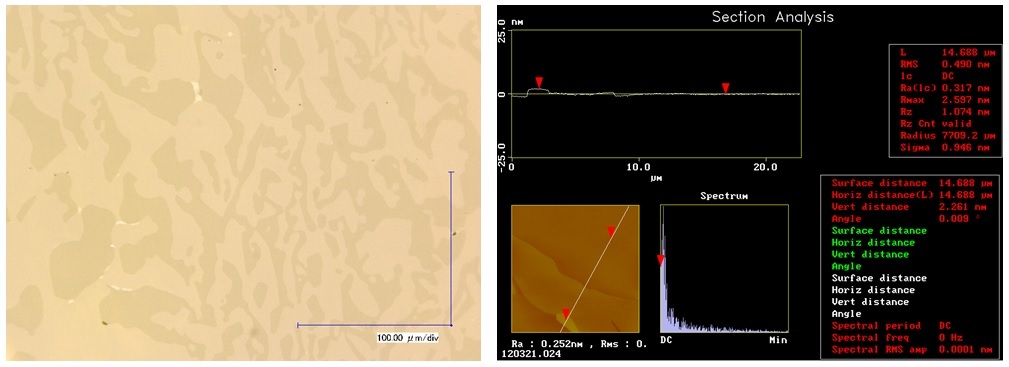
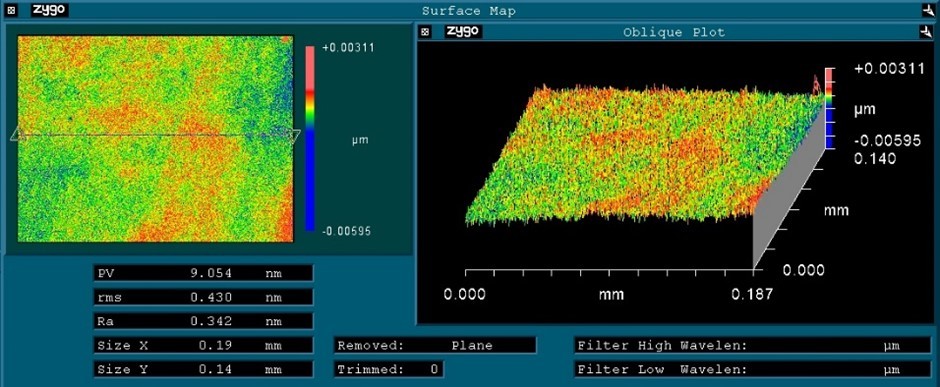
最後に
Mipoxが培ってきた高精度研磨加工技術は、本稿で紹介した接合を目的としたセラミック材料向けに限らず様々な材料に対し新しいデバイス創造に携わってきました。
例えば、単結晶サファイア材料は蛍光灯からLEDへ照明の世代交代を促す主材料となり世の中を一変させました。
Al系合金材料は超高精度の平面・表面粗さを達成する事で今日のAIやIoTに不可欠なデータベース(ビッグデータ)を支える大容量記録媒体となりました。
近年注目されている半導体の高密度パッケージング技術にもMipoxの研磨材・研磨技術が活かされており、期待を頂いています。未知の可能性を秘める各材料の新たな用途・新技術創出に、Mipoxの高精度研磨加工(CMP)技術が貢献できれば幸いです。
【参考文献】
異種材料一体化のための最新技術 サイエンス&テクノロジー社 (2012)
中田一博著 マルチマテリアル時代の接合技術 産報出版 (2016)
異種材料接合の最新技術 東レリサーチセンター (2014)