最近の自動車にはほとんど高張力鋼板が使用されていますが、実はこの高張力鋼板が自動車板金屋さんの板金作業を悩ませるワークなのではないでしょうか。
板金作業にはパテという補修製品がつきものです。しかしながら、パテを使う時には大きな難問が待ち構えています。叩き出しだけで面出しができれば理想かもしれませんが、
面出し作業においてパテは必須アイテムなのです。
本記事では、高張力鋼板の特徴やメリットに加え、このパテを高張力鋼板に使用するときの問題を解決できるシステム(ツール)を紹介します。
目次
高張力鋼板の定義とは
高張力鋼板は、「ハイテン」(High Tensile Strength Steel Sheets)とも呼ばれる引っ張り強さが高い鋼板のことです。普通鋼板が引張り強さ270MPa以上であるのに対して、一般的には340MPa~790MPaのものが高張力鋼板と定義されています。しかしながら、この定義は各社・各国によって違いがあるので注意が必要です。あるところでは490MPa以上を高張力鋼とする見方もあり、ドイツでは180MPa以上を高張力鋼と呼ぶこともあります。また、引張り強さ980MPa以上のものは通常「超高張力鋼板」と呼ばれます。
高張力鋼板の種類としては、炭素の他にニッケル(Ni)やシリコン(Si)、マンガン(Mn) などの元素を添加して強化した固溶強化型や析出強化型鋼板、レス成形後に焼入れして強化した複合組織鋼板などがあります。
また、プレス成形する前に材料を加熱して、成形後急冷して強度を高める熱間プレス成形法が開発され、採用が広がっています。
高張力鋼板の特徴3つ
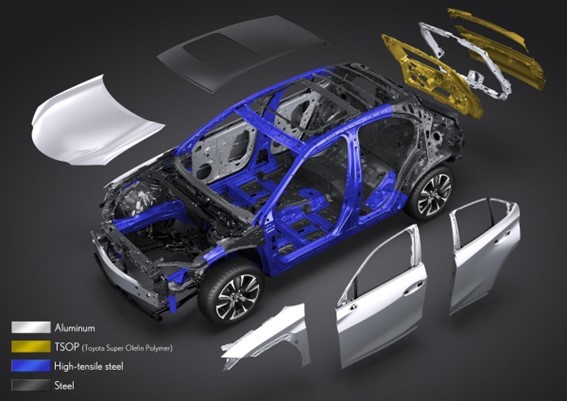
1.軽量化が可能
高張力鋼は強度があるため、普通鋼と同じ強度を確保する際に、薄肉化が可能です。薄肉化をすることで、鋼材の使用量を減らし、軽量化できます。普通自動車や作業車などの移動車両に高張力鋼を使用すると、燃費の向上により経済性を高めることが可能になり、薄肉化できることは、高張力鋼の最大の特徴といえます。
2.耐食性があり錆びにくい
高張力鋼には、高い耐食性があります。
耐食性があることで、野外の建造物に使用して風雨にさらされる場合も、錆びにくいです。この特徴から、石油タンクや、液体を運ぶ水圧管に採用事例もあります。海に浮かぶ構造物や、河川に浮かぶ橋の鋼材にも、耐食性の高さから適用可能です。耐食性があることは、高張力鋼の利点となります。
3.低コストで大量生産に向く
ハイテン材は、優れた鋼材であるため、市場供給量が年々増えています。 市場供給量が増えればコストも下がるため、さらに供給量が増えるという好循環を起こしているのです。つまり、ハイテン材は低コストで大量生産に向いているということです。低コストでありながら高品質であるため、ハイテン材を利用した製品も増えています。
高張力鋼板のメリットデメリット
メリット
高張力鋼板のメリットは、薄くても張りがあるため、これまでよりも鋼板の厚みを薄くできることです。鋼板が薄くてもこれまで以上の剛性があるため、大幅な軽量化が実現できます。
自動車産業で、軽量化に成功すれば、燃費を上げる効果も発生します。つまりハイテン材を利用することで、ボディの剛性が高まり大幅な軽量化を実現し、燃費を上げることができるのです。
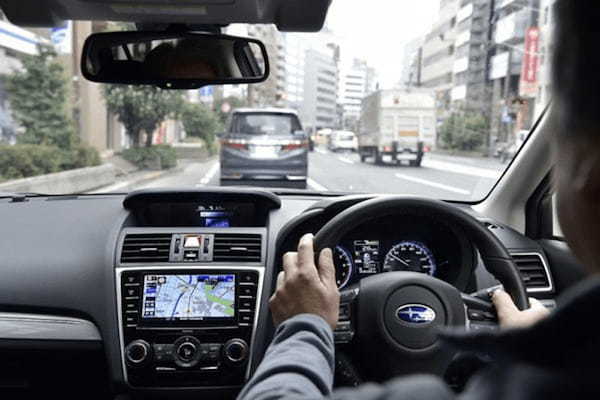
デメリット
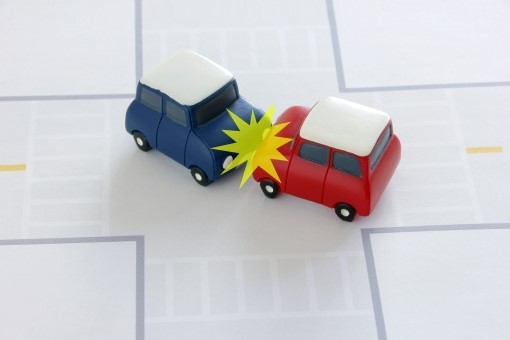
高張力鋼板のデメリットは、強度が高いため成形荷重も高くなることです。 成形荷重は、プレス成形機で成形を押し固めるのに必要な力のことをさします。 ハイテン材をプレスするためには金型自体の強度が求められるため、プレス成形中に破断が起こる可能性もあり、 成形が難しいといえます。剛性の低下を避けなければいけない部分には使えない点もデメリットです。
自動車産業で高張力鋼板の需要が高まっている背景
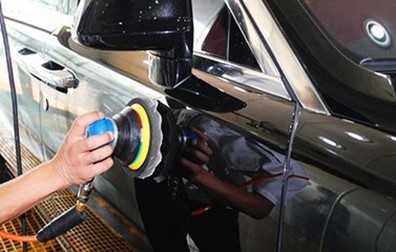
自動車産業においてハイテン材の需要が高まっている背景は、モノコックシャーシーが登場し、車のボディ構造が鉄で作られるようになったことが起因しています。
モノコックシャーシーとは、ボディと車台(シャーシー)が一体化されている構造を制作する技法をさします。
モノコックシャーシーなら、フレームとボディを同時に作るため、従来よりも強度が高く、効率的に車内スペースを確保できて、軽量化も可能です。
モノコックシャーシーのデメリットである形状の複雑化を補うために、加工しやすくて強度が高いハイテン材の需要が年々高まっています。
ユーザー様の悩みの原因
パテを高張力鋼板で使用するとき、当然硬化時に熱が発生します。この熱が面だししている鉄板をゆがませるのです。鉄板表面にはパテがあるのですが、裏面には何もないので、表面と裏面で膨張率が異なり歪んでしまうのです。このゆがみを防ぐためにどうするか…鉄板の表と裏で膨張率が異なるために歪むのなら同じ膨張率にすればいい…ということで裏面にもパテを塗って歪みを防ぎます。最近は裏塗り専用のパテも販売されています。
高張力鋼板はこの熱によるゆがみが弱点なのです。この熱の発生はパテの硬化時ともうひとつパテ研磨での熱の発生があります。
このような手ごわい高張力鋼板ですが、車にとってはメリットが大きいのでこれからも採用は拡大していくのではないかと我々は予測しています。
高張力鋼板の研磨時にできるだけ熱を発生させずになおかつ工程短縮、作業環境改善が可能な研磨プロセスを紹介いたします。
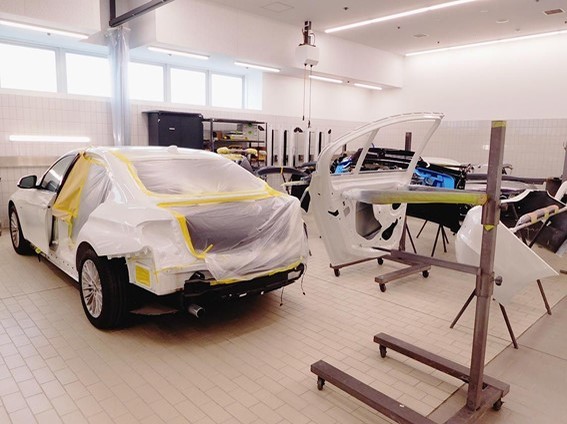
今回、ユーザーの皆さんのお悩みを解決するための手段としてMipoxが紹介する自動車補修の下地板金システム(ツール)は、高張力鋼板にマッチした「スマートサンディングシステム」です。
スマートサンディングシステムの特徴
1.工程短縮&コストダウン
通常14工程がスマートサンディングシステムでは9工程での作業が可能です。その理由は、「研削性の高いダブルアクションサンダーのスマートサンダー(SD-7)」と「研磨目の細かい耐taiQ」との組み合わせにより、従来シングルサンダーの#60や#80の粗いペーパー使用せずに、「塗膜剥離とフェザーエッジ」の作業が同時に実現できることがメリットになります。この提案はシステムで提案できるMipoxだからこそできる提案なのです。このスマートサンダーと耐taiQとの組み合わせによって時間短縮とコストダウンが可能になります。
2.品質向上
①鉄板熱を従来工法と比較し30%下げる事が可能なため鉄板へのダメージ軽減
②フェザーエッジの研磨目も細かくキレイに入るため後工程が断然楽になる
3.作業環境向上
① フル吸塵システム提案により大幅な作業環境清浄度UP
② 吸塵ファイルを販売しているメーカーも少なくなってきています。吸塵ファイルメーカーというのはなく、サンダーメーカーも研磨材メーカーもテリトリーではないのでMipoxが開発しました。
4.コストパフォーマンス
グローバル市場を見据えたサンディングシステムとしての提案によりサンダー/吸塵ファイルともお求め易い価格となっています。
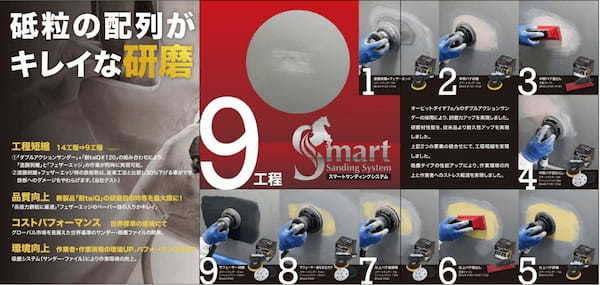
まとめ
高張力鋼板は、軽量化と相反する車体強度を両立させ、燃費性能や衝突安全性能、運動性能の向上させるためには不可欠な材料です。アルミやプラスチック、CFRPなど材料置換も進められていますが、最も一般的なのは高張力鋼板の活用となっています。その高張力鋼板の補修で一番の敵は、鉄板熱によるゆがみになります。鉄板研磨やパテ研磨での研磨熱をできる限り低減し、今後ますます増えていくことが予想される高張力鋼板に対応するために板金技術革新を前進させていきます。
最後になりますが、これからの自動車産業は、EV化と自動車運転化が進むことで、人間にとってより快適な道具へとさらに進化していきます。私たちは、自動車産業の総合的な知見と技術を持つ業界トップランナーとして、その進化にさらに貢献していくことをこれからも目指していきます。