近年のスポーツ自転車のブームに伴って、自転車に関連した商品やメディアへの紹介を目にする機会も多くなりました。今回は自転車の主要部品である変速機・ブレーキ・ギア・ペダルなどを製造している部品メーカーA社の事例を交えながらアルミ製クランクのバリ取り研磨自動化について説明します。
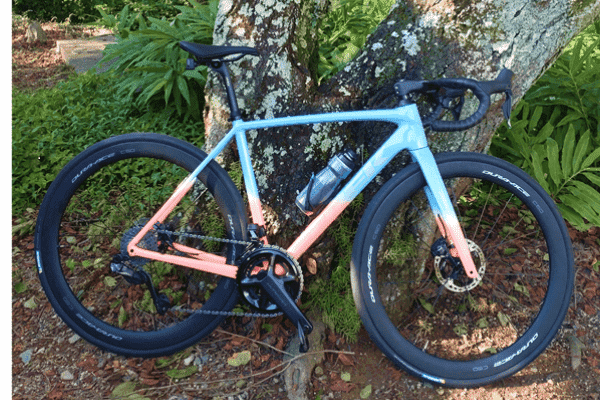
アルミ製クランクのバリ取り研磨とご提案
一般に往復運動を回転運動に変える装置をクランクと言い、自転車の場合はペダル軸とクランク軸を連結している棒部分をクランクと呼びます。特にスポーツ自転車の部品は出来るだけ軽くすることが望まれているためクランクにおいても内部を中空構造にして軽量化したものが主流となっています。少し前までの中空クランクはパイプから成型したもので強度が比較的弱く、設計の自由度も低いため形状が制約されていました。しかし現在はアルミ合金を金型で鋳造しクランクの適所を中空構造にする事によって、軽量で十分な強度を得ることができるようになっています。それに伴い形状の自由度も増して外見にオリジナリティーや高級感を持たせることも可能になっています。 A社では以前から生産量アップとコストダウンを行うべく自動生産ラインを模索しており、今回A社Y工場においてアルミ合金製中空クランクの自動製造ラインを新設する運びとなりました。その中で研磨工程については研磨加工時間12秒/個以下、日産量5,000個が目標値として設定されました。 研磨工程はクランクの金型鋳造時に発生するワーク表面のバリ取り研磨が主となります。当初は従来から採用している研磨ベルトでのロボット研磨を検討しテストを進めていましたが、自動化によるラインスピードの短縮化、ベルトの取替え頻度の問題、またアルミ粉塵の防爆対策などのリスクが顕在化し、ベルト研磨方式での実現は困難との結論に至っています。代替案としてNPフラップホイール(研磨輪)での研磨方式を採用することとなりました。
研磨テストの推移と結果
前述したように当初はベルト研磨によって加工を行うことを検討しており、当社の金属用研磨布ベルトPRWJ/SRAJ/SRAJ-S11/WRAX-S23 の基材を選定して粒度#240/#320、サイズ50X1850mmにて研磨テストを実施。しかし、いずれの研磨ベルトも目詰まりによるライフ不足が発生しクランク40個/ベルト1本 の頻度での取り替えとなり日産量5,000個には到底至らず結果NGとなっています。そこで次のアクションとして金属研磨、特にステンレス丸棒研磨で定評があり、自生作用による研磨ライフ改善を期待してNPフラップホイールを提案。研磨ベルトと同じ4種類の基材でホイールを作成しテストを実施しました。
クランクNo. | 基材型式 | 粒度 | 研磨結果 |
---|---|---|---|
① | SRAJ | #240 | 仕上げ面良好だが研磨力不足。 |
② | PRWJ | #240 | 仕上げ面普通。研磨布のコシが若干強すぎる感じ。 |
③ | SRAJ-S11 | #240 | 仕上げ面良好だが研磨力不足。 |
④ | WRAX-S23 | #240 | 仕上がり面粗い。研磨力良好。研磨時間最短。 |
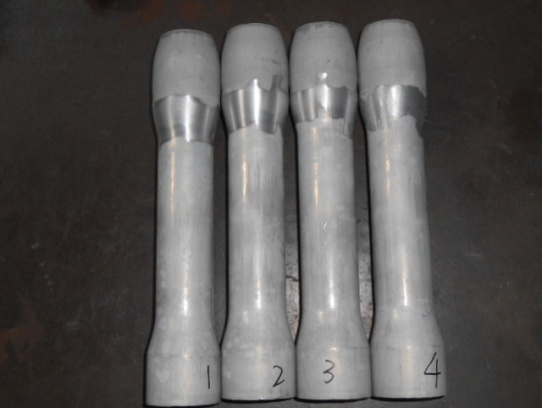
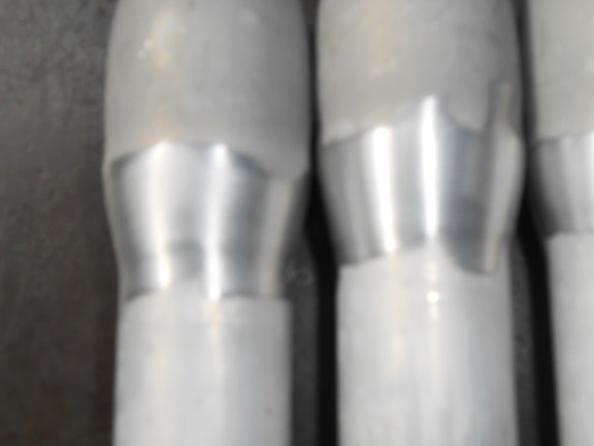
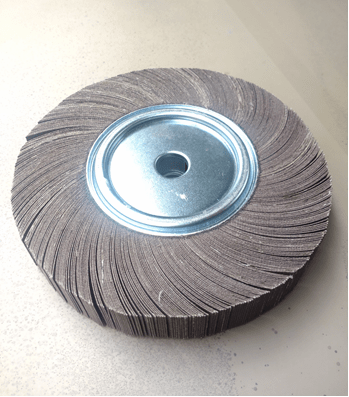
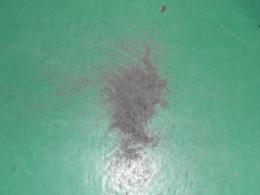
テストの初期段階では表面の仕上がりばかりを気にしてしまったこともあって①が最高評価でしたが、のちに①②③は仕上げ面過剰品質の判定となっています。目標値である日産量個数に対してホイールの交換頻度とクランク1個あたりの研磨時間が最も重要視され、最終的には④の仕上がり面は粗いが基準はクリアーしており研削量が多く耐久性のあるWRAX S-23の基材に決定しました。研磨スピードも10秒/本にて日産量5,000個をクリアー出来る見通しとなり、テストは無事成功となりました。 また、粉塵対策として湿式研磨を推奨していましたが、量産時の湿式は設備、リードタイム的に実施困難との判断となり、テストにおいてもすべて乾式研磨で作業を行なっています。アルミ研磨粉の防爆対策は量産ラインでは集塵機能付き研磨機とすることで対応しています。
研磨はMipoxにご相談ください
今回のように従来の研磨方法である研磨ベルト方式からY工場では取り組んだ事のないNPホイール方式を提案できたことにより、固定概念にとらわれない発想の転換で満足行く結果にたどり着く事が出来ました。あらためて本当にお客様が望んでいるものは何かを考え、綿密な打ち合わせや意見交換することの大切さを感じとることができました。今後も様々な角度から現場の声をお聴きし、それに対して製品やノウハウを具現化していく事で皆様のお役に立てることを楽しみにしています。今後ともMipoxをよろしくお願い申し上げます。