現在、多くの製造現場ではショットブラストを使用して表面処理を行っていますが、この伝統的な方法にはいくつかの問題点があります。
ショットブラストは、消耗品の研磨材(メディア)が必要であり、消耗品であるためその処理にはコストがかかります。また、部分的な加工が苦手で、非加工部分にはマスク処理が必要です。さらに、装置が大きいためインライン化が難しく、設置スペースも多くを占めます。環境負荷が大きい処理方法と言えるでしょう。
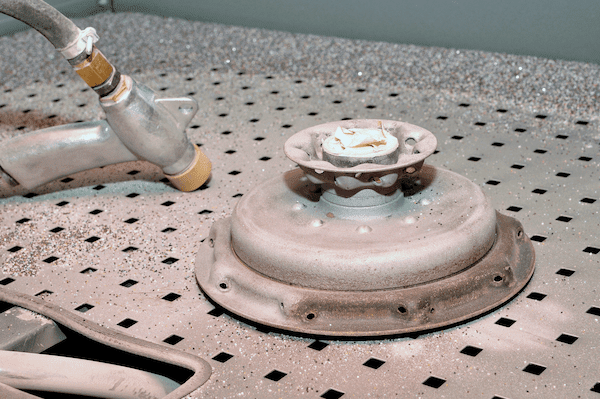
これに対して、レーザー剥離技術は多くのメリットを提供します。まず、レーザー光で表面加工を行うため、電気代のみで稼動し、消耗品のコストが不要です。弊社のデモ機試算では1時間の消費電力はわずか200円でした。(1500Wのレーザーガン使用)
ドライプロセスであるため、洗浄工程も不要です。さらに狙った部分のみをピンポイントで加工可能です。また、装置が小型化できるため、インライン化がしやすく、設置スペースも節約できます。
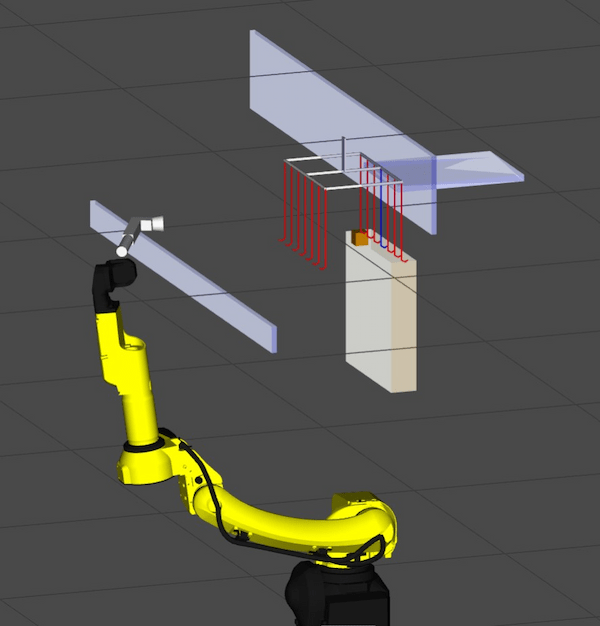
具体的なアプリケーション事例としては、塗装密着性の向上や塗膜剥離があります。レーザーで金属表面を荒らすことで、塗装の密着性が改善します。レーザークリーニングはサンドブラストの現実的な代替手段として注目されています。レーザークリーニングは、材料へのダメージを最小限に抑えながら、表面を効果的に短時間でクリーニングし、コーティングや溶接の前処理や錆除去を行い、塗料を剥離します。
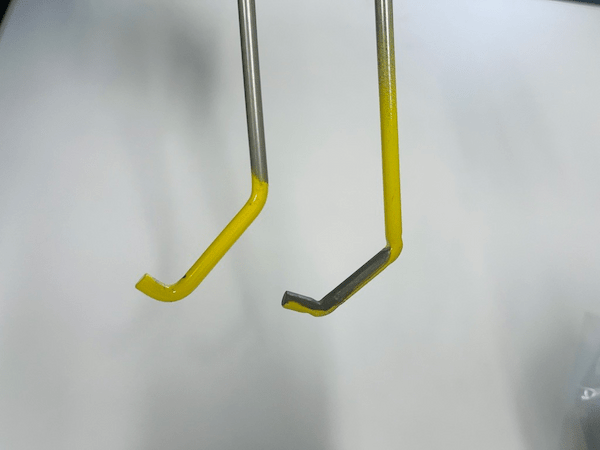
これにより、環境に優しく、費用対効果の高いソリューションを提供します。レーザーアブレーションを使用することで、基材にほとんど影響を与えずに特定の物質を除去でき、エネルギー効率も高いです。
レーザークリーニング技術は、塗膜剥離、錆除去や酸化物、油、グリースの除去など、さまざまな用途に利用できます。汚染物質を気化させて除去するイメージです。鉄球で鉄材をショットブラストした場合表面の削り取りは0.1mmから数mmになりますが、レーザー技術では10分の1以下の0.01mm未満です。基材にほとんど影響を与えずにクリーニングが可能です。塗装ハンガーの買い替え頻度も劇的に減ります。
レーザークリーニングのメリットとしては、自動化が容易で再現性と再生産性が高いこと、消耗品が不要でほとんどの用途で特別な保護具やオペトレが不要であることが挙げられます。また、非常に局所的なエリアを処理できるため、効率的なクリーニングが可能です。Mipoxのレーザークリーニングシステムは、モジュール化されたユニットを提供しており、ユーザーのニーズに合わせたカスタマイズが可能となっています。
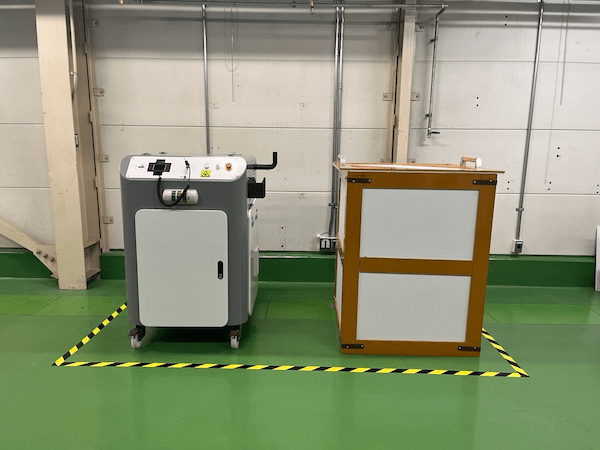
以上のように、レーザー剥離技術はショットブラストに代わる技術として、多くのメリットを提供します。コスト削減や加工精度の向上、小型化によるスペース効率の改善など、多くの利点があり、製造業界において効率性と環境負荷の低減を両立する最適なソリューションと言えるでしょう。