はじめに
日本の自動車業界をとりまく環境がここ数年で急速に変化しています。車離れや不正により元々不振であった国内市場に加えて米国、欧州に端を発したEVシフトの推進と停滞。そして中国の台頭。成長を続けてきた新興国市場においても現在の購買層の需要は頭打ちが見え始めており、昨今の急激な為替の変動がさらなるリスクを顕在化させている状況です。
しかし、こういった潮流のなかにあっても自動車産業は日本の基幹産業であり、自動車1台あたりに使用される部品は数万点におよび数々の関連産業の裾野をささえています。その需要は当社においても重要な位置を占めており、カーメーカーを頂点とした子会社、下請け、孫請け…町工場にいたるまで主要な取引先が数多く存在しています。今回はその自動車産業の裾野の1社であるY社に焦点をあててレポートしてまいります。
概要
Y社は西日本に立地するブロー成形を主体とする樹脂製品製造会社となります。もともとは自動車のエンジン周辺の樹脂部品でスタートしましたが、成形技術の応用で自動車用スポイラーを手掛け始めました。
しかし外観部品であるスポイラーは求められる品質基準がエンジン樹脂部品より大幅に高いため、当初は生産効率が上がらず失敗の連続となっていました。現在Y社ではカーメーカー向けに5車種のスポイラーを製造しており、仕上げの精度は車種ごとに異なりますが製造工程はほぼ同じとなります。あと、同社では塗装は行われておらず塗装前の下地最終品を出荷しています。
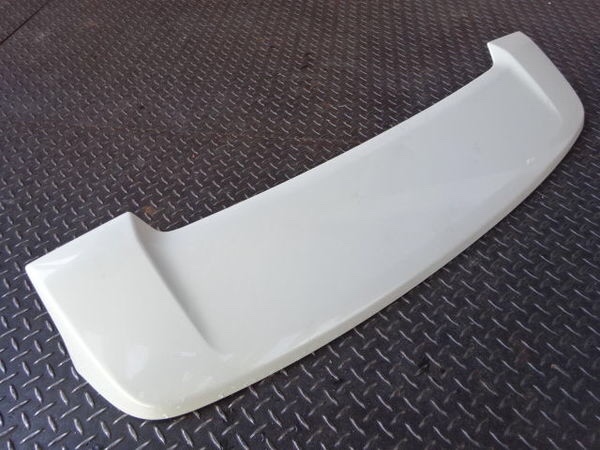

原料は熱可塑性樹脂であるABS樹脂が使用されています。硬度、加工性、耐衝撃性、曲げ疲労性などの機械的特性に優れ、油、薬品に侵されにくいといった自動車の外観部品に最適な特性を持っていますが樹脂の中では硬く、粘いといった研磨には難しい素材でもあります。
ブロー成形機によって風船のように膨らんだABS樹脂が金型によっておおよそ完成品の形状で出てくるのですが、ブロー成形の特性上必ずバリやヒケといった現象が発生するため研磨工程が必要となります。
バリ取り~エッジ研磨
- 研磨方法:ロボットによる湿式研磨
- 研磨材:フィルムマジックWRAF-DM #320 125m/m
- サンダー:コンパクトツール913W-5 9,000rpm オービットダイヤ5mm
バリについては成形時の金型の合わせ面から樹脂がはみ出ることが原因でスポイラー外周の約2/3に渡って発生します。このバリ取りは2工程に分かれており
①カッターによる大まかなバリの切除
②切除しきれなかったバリの削除とエッジ部分の整形を兼ねた研磨
となっています。
①の大まかなバリ取りについては現在クラフト用カッターを使った手作業でカットする方法を用いていますが、以前から研磨による削除ができないかとの要望がありました。ただバリの高さが4~5㎜と長めなのに対して厚みが0.01~0.015㎜と極薄のため#320の粒度ではバリが腰砕けになり削除しきれないというのが現状となっています。それ以上粗い粒度の使用は削り込みすぎや後工程の増加といった問題が発生するためカッターによる前工程が外せない状況です。
②の細かなバリとエッジ部分の整形研磨はすべて自動ロボット研磨となります。約3分/1個のペースでロボットアームがサンダーを3次元的に動かして研磨を行います。研磨材に求められる性能は非常に高く、仕上げ面の安定性、耐水性、耐久性、基材の適度なコシの4点が重視されます。
そしてそのすべての条件をWRAF-DMが満たしており、特に耐水性、耐久性と適度なコシにおいてはPETフィルムの基材が最適と評価されています。他基材と比較して復元力に優れた基材特性がスポイラーのエッジ部分に対して相性が良く、さらに要求される仕上げ面をクリアしてのスペックインとなっています。
中研磨~仕上げ研磨
- 研磨方法:手持ちサンダーによる乾式研磨・湿式研磨
- 研磨材:マジックタックRRAC-DDSM #400 125m/m
フィルムマジックWRAF-DM #600 125m/m - サンダー:#400用 ダイナブレード 11,000rpm オービットダイヤ5mm
#600用 コンパクトツール913W-5 9,000rpm オービットダイヤ5mm
中研磨工程はスポイラーの平面部分の研磨が主体となりますが1次検品の結果によっては必要がない場合もあり、検品で問題がなかった場合は中研磨をスキップして仕上げ研磨工程へ移行します。
ブロー成形はその特性上、平面部分にそれなりの頻度でヒケ、気泡、フローマークが発生するのですが1次検品時にそういった不具合があった場合にのみ、不具合個所の修正研磨を行います。これを中研磨と呼んでいます。
この工程だけ乾式研磨となるのは、修正にパテを使用することと研磨をしながら修正箇所の目視確認がしやすいとの理由によります。ただ乾式ゆえの仕上げ面が若干粗くなる傾向があるため、エッジ研磨のWRAF-DM #320に対して#400と1番手粒度を細かくしているところがポイントとなります。
この工程での研磨材は仕上げ面の安定性と乾式での耐目詰まり性が特に重視され、テストデーターで最も良好な結果となったRRAC-DDSMが採用されています。ここで修正を行った製品と1次検品で問題がなかった製品が次の仕上げ研磨工程へ移されます。
仕上げ研磨工程については現在Y社で製造されているスポイラーに求められる最終仕上げ面粗さは#600(約30μ)となっており、この工程でWRAF-DM #600による湿式研磨をスポイラー全体に行います。この作業により前工程のペーパー目の除去と塗装前の足つけを施され全ての研磨工程は完了となります。
研磨はMipoxにご相談ください
ここまでY社のスポイラー研磨についての作業内容と経緯についてお話しさせていただきましたが、これらの手順については初めから正解があったわけではなく、ユーザー様と試行錯誤を繰り返して辿り着いた現時点でのベストな着地点です。冒頭でもふれました自動車産業の構造そのものが変化している昨今、Y社においても例外ではなく品質、納期、コスト等の要求はさらに厳しくなり様々な見直しが迫られています。生産現場では原材料樹脂の変更、金型の精密化、ブロー方法の変更でバリの発生を無くし極力研磨をしなくともよい高精度な状態へ持っていこうと研究が進んでいます。
そういったなかで今後も様々な角度から現場の声をお聴きし、ニーズに対してその時点でのベストな製品やノウハウをご提案する事で皆様のお役に立てることを楽しみにしています。今後ともMipoxをよろしくお願い申し上げます。