金型製造において、研磨材は作り始めから仕上げまでの一連の工程で広く使用されています。研磨材は、金型の表面を滑らかにし、必要な寸法精度や表面粗さを達成するために使用されます。この記事では金型製造における研磨材の使用状況について説明します。
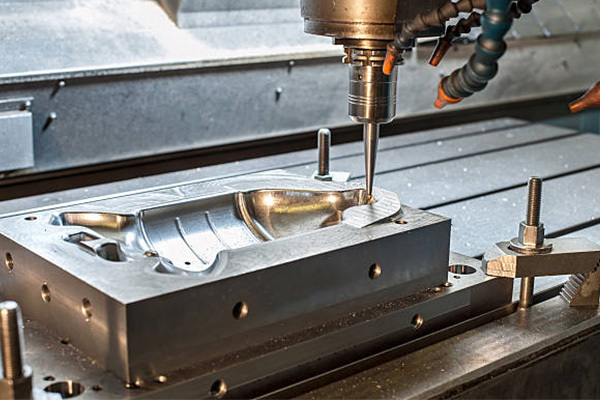
金型とは
金型(かながた)は、製造業において特定の形状や構造を持つ部品や製品を大量に生産するための工具または型具です。金型は、主に金属、プラスチック、ゴム、ガラス、樹脂などの材料を成形する際に使用されます。以下に金型の基本的な概要を説明します。
金型の種類
金型には、用途や材料に応じてさまざまな種類がありますが、主に以下の4つに分類されます。
- プレス金型: 金属板を打ち抜いたり、曲げたり、絞ったりして形状を成形するための金型です。自動車の車体部品や家電製品の外装部品などの製造に広く使われます。
- 射出成形金型: プラスチックなどの樹脂を溶かして金型に流し込み、冷却・硬化させて形状を作る金型です。家庭用品や電子機器のケース、車両の部品などの製造に使用されます。
- 鋳造金型: 溶融した金属を型に流し込んで成形するための金型です。エンジン部品や金属製のフレームなど、高強度が必要な部品の製造に使用されます。
- 鍛造金型: 金属を高温で加熱して柔らかくし、プレスやハンマーで叩いて成形する金型です。歯車やシャフトなど、強度や耐久性が求められる部品の製造に使われます。
金型の製造と加工
金型の製造には高度な技術と精密な機械加工が必要です。金型は通常、設計図に基づいて高精度の機械や工具を使用して作られます。加工方法には、旋盤加工、フライス加工、研削加工、電気放電加工(EDM)などがあります。
金型の使用例
金型は、多くの製造業において不可欠なツールです。以下はその代表的な使用例です。
・自動車産業: 車両の外装パネル、エンジン部品、インテリア部品などの製造に金型が使用されます。
・家電製品: テレビや冷蔵庫、洗濯機の外装や内部部品を成形するために金型が使われます。
・日用品: プラスチック製の容器や家具など、多くの一般消費財も金型を使用して大量生産されています。
金型の重要性
金型は、製品の品質、精度、コスト効率に大きな影響を与えます。金型の精度が高ければ高いほど、製造される製品も高品質で均一なものになります。また、金型の耐久性が高ければ、生産ラインで長期間使用できるため、コスト削減にもつながります。
金型は、現代の製造業において欠かせない重要な技術であり、製品の大量生産を支える要素となっています。
金型製造における研磨材の目的と役割
・表面仕上げ: 金型の表面を均一に整え、鏡面仕上げや高精度な表面を得るために使用されます。特に、金型の表面に残る微細な傷や不均一な部分を取り除くために研磨材が使われます。
・寸法調整: 研磨材を使って、金型の寸法を微調整し、規定された精度に合わせることが可能です。これは、最終的な加工で必要な寸法に到達するための重要なステップです。
・バリ取り: 金型のエッジや隅の部分に残るバリ(鋭い突起)を取り除くためにも研磨材が使われます。
具体的には下記のように製造現場で研磨材が活躍しています。
・自動車部品の金型製造: 車両のボディパネルやエンジン部品の金型で、特に高精度が求められる部分で研磨材が使用されます。
・電子部品の金型製造: スマートフォンやコンピュータのケースなどの金型で、表面の微細な仕上げが求められる場合に使用されます。
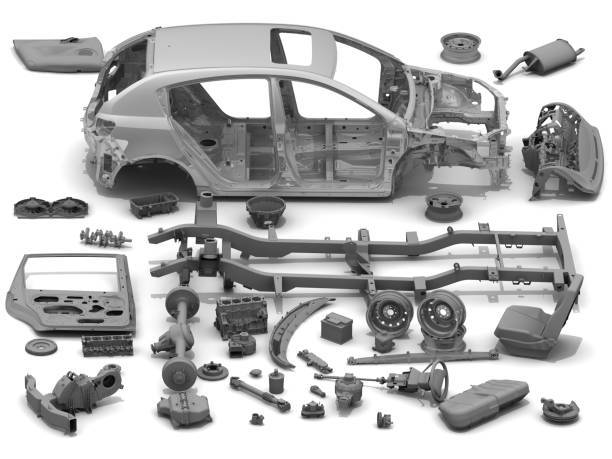
使用される研磨材の種類
- アルミナ(酸化アルミニウム)系研磨材
特徴: 酸化アルミニウムは、高い硬度と耐久性を持つ研磨材です。鋼や鉄などの硬質金属に対して優れた切削性を発揮し、長寿命で使用できます。研磨布紙の基材には、通常、耐久性が高いコットンやポリエステルが使用されます。
用途: 鋼や鉄などの硬い金属を対象とした金型の仕上げに使用されます。特に、初期の粗削りや中間仕上げに適しています。
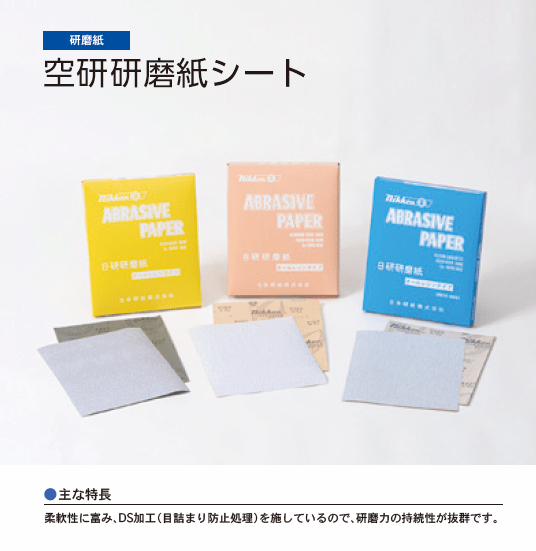
- シリコンカーバイド(炭化ケイ素)系研磨材
特徴: シリコンカーバイドは、非常に硬い研磨材で、アルミナよりもさらに硬度が高いですが、脆さがあります。そのため、短期間で鋭い切削力を発揮する一方で、長時間の使用には適さないことがあります。基材には紙や布が使われます。
用途: アルミニウム、銅、真鍮などの非鉄金属やプラスチック、ガラス、石材などの仕上げに使用されます。非常に滑らかな仕上げが求められる金型の最終工程にも使用されます。
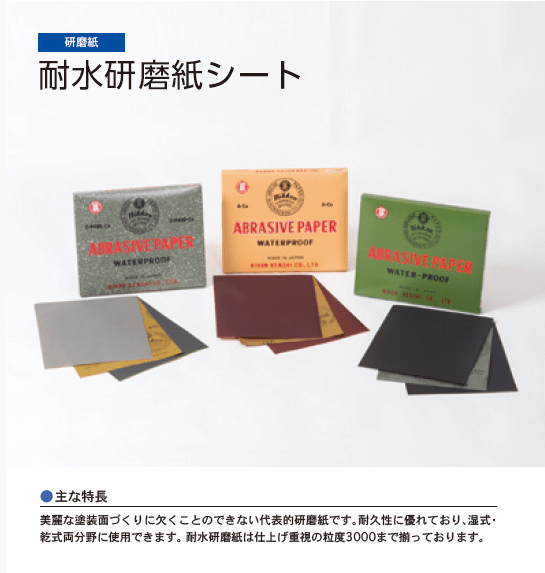
- ジルコニア系研磨材
特徴: ジルコニアは、非常に強靭で、自生作用を持つ研磨材です。これにより、使用中に新しい鋭いエッジが現れ、長期間にわたり高い切削力を維持します。 用途: 高硬度の金属(例えばステンレス鋼)や重度の研削が必要な場面で使用されます。粗削りから中間仕上げに適しており、頑丈な金型の加工に役立ちます。
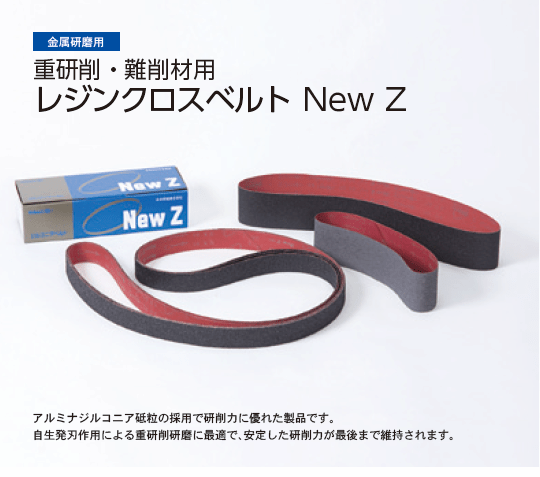
- ダイヤモンド系研磨材
特徴: ダイヤモンドは、自然界で最も硬い物質であり、極めて高い切削力を持つ研磨材です。ダイヤモンド研磨材は、高価ですが、硬度が非常に高い材料や、極めて細かな仕上げを必要とする作業において優れた性能を発揮します。
用途: 超硬合金やセラミック、ガラスなどの非常に硬い材料の研磨に使用されます。また、鏡面仕上げや微細な形状の精密仕上げにも適しています。
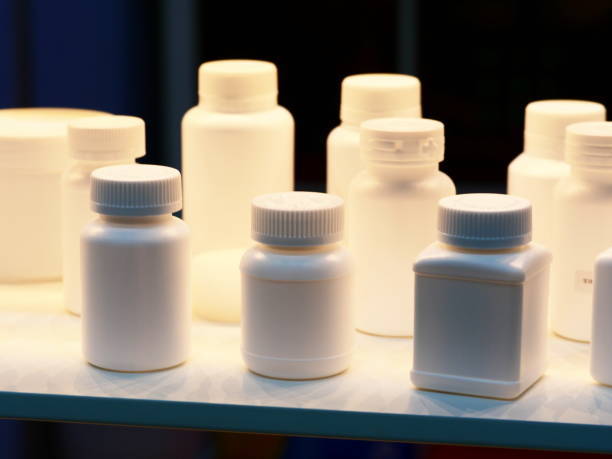
金型研磨における研磨材の使用方法
・手作業での研磨: 金型の微細な部分や細かい仕上げを行う際には、作業者が研磨材を手に取り、慎重に研磨を行います。この方法は、細かい部分まで均一に仕上げることができるため、多くの金型製造現場で利用されています。
・機械による研磨: 大きな面積や一定の平坦さを求める際には、研磨機に研磨材をセットして使用します。これにより、均一な圧力で効率的に研磨することが可能です。
金型研磨において研磨材を使用するメリット
金型製造において研磨材を使用することには、いくつかの重要なメリットがあります。研磨材は、金型の仕上げ工程で広く使用されており、その効果は金型の性能や製品の品質に直結します。
1:高精度な仕上げが可能
・表面の滑らかさ向上:研磨材を使うことで、金型の表面を非常に滑らかに仕上げることができます。これは、金型から作られる製品の品質にも大きく影響します。例えば、光沢のある仕上げや高い表面精度が要求される場合、研磨材は不可欠です。
・寸法精度の向上: 金型の最終的な寸法を微調整する際にも研磨材が活用されます。研磨材を使うことで、ミクロン単位での調整が可能となり、高精度な金型を実現します。
2:コスト効率の改善
・再加工の削減: 研磨材を使用することで、金型の表面品質が向上し、不良品の発生を抑えることができます。これにより、製品の再加工や手直しの必要性が減り、全体の製造コストを削減できます。
・金型寿命の延長: 適切な研磨材を使って金型を仕上げることで、金型自体の摩耗を抑え、その寿命を延ばすことができます。これにより、金型の交換頻度が減少し、長期的なコスト削減に寄与します。
3:柔軟性と適応性
・多様な材質に対応: 研磨材は、金型の材質や形状に応じて適切なものを選ぶことができ、幅広い材料に対応可能です。金属、プラスチック、ゴムなど、さまざまな素材の仕上げに使えるため、製造現場での汎用性が高いです。
・難しい形状の仕上げが可能: 研磨材は柔軟性があるため、手作業での研磨が可能であり、複雑な形状や細かな部分の仕上げに適しています。機械では難しい部位でも、研磨材を使うことで均一に仕上げることができます。
4:品質向上と一貫性の確保
・安定した品質の実現: 研磨材を使用することで、金型表面の一貫した品質を確保できます。これにより、製品のばらつきを最小限に抑え、高い生産性を維持することができます。
・仕上がりの美観向上: 高品質の研磨材を使用することで、金型表面に光沢を与え、美観に優れた製品を製造することが可能です。これにより、製品の付加価値が高まり、競争力が向上します。
5: 作業効率の向上
・作業の迅速化: 研磨材は手軽に使えるため、金型の仕上げ作業が迅速に行えます。特に、部分的な修正や細かな仕上げを短時間で行うことができ、生産ラインの効率を高めます。
・研磨作業のコントロール性: 手作業で研磨材を使うことで、細かな調整が可能となり、作業者が仕上げの程度を直接コントロールできます。これにより、製品ごとに異なる要求に柔軟に対応できます。
これらのメリットにより、研磨材は金型製造において不可欠なツールとなっています。製品の品質を向上させ、コストを削減し、作業効率を高めるために、適切な研磨材の選定と使用が求められます。
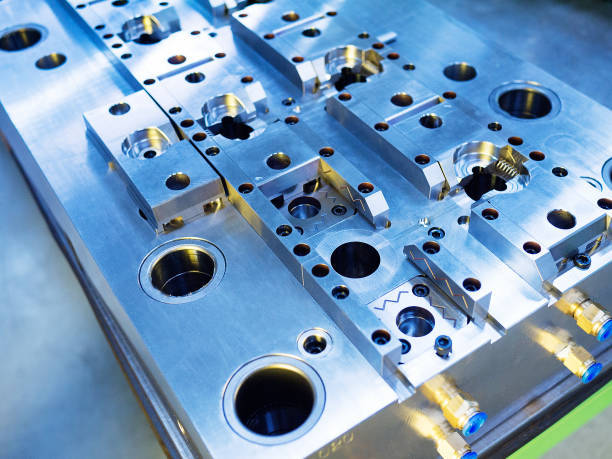
まとめ
金型製造において研磨材は、製品の品質や耐久性に大きな影響を与える重要な要素です。適切な研磨材を選び、効果的に使用することで、金型の仕上がり精度を大幅に向上させることができます。また、研磨材の選定と使用法には細心の注意が必要で、定期的なメンテナンスを行うことでコスト削減と作業効率の向上が期待できます。研磨材の選び方と使い方を正しく理解し、金型製造における最高のパフォーマンスを引き出せます。そして当社はこれまでに培ってきた知識と経験を活かし、お客様の課題解決に向けて製品開発を進めております。この分野のさらなる発展に貢献できるようmipoxも日々進化を続けています。