半導体業界は常に高性能かつ高効率なデバイスの製造を目指しており、その中でシリコン酸化膜(SiO₂)の品質管理は重要な課題となっています。酸化膜の品質は、半導体デバイスの性能と信頼性に直結しており、特に酸化膜が形成されるエッジ部の管理が欠かせません。今回はシリコンウェーハの酸化膜について、その重要性とエッジ部/ノッチ部の膜除去の必要性、またMipoxでの解決策について詳しく紹介します。
目次
ウェーハの酸化膜とは
酸化工程の目的は、ウェーハ上に絶縁膜の役割を担う酸化膜を形成し、回路間にリーク電流が流れるのを遮断することです。 酸化工程で形成された酸化膜は、半導体の製造過程において強固な保護膜となります。 ウェーハは大気中または化学物質内で酸素に触れると酸化膜を形成します。これは鉄が空気に触れると酸化して錆ができるのと同じ仕組みです。
膜を形成するメリット
絶縁効果
酸化膜は非常に優れた絶縁性をもっています。このため、電気信号が隣接する回路に漏れることなく伝達されるので、半導体デバイスの性能が安定します。
表面保護
酸化膜はウェーハの表面を物理的、化学的なダメージから保護します。 これにより製造中や使用中に汚染や損傷が発生しにくくなりデバイスの寿命が延びます。
精密な加工が可能になる
酸化膜はフォトリソグラフィーやエッチングといった半導体の精密加工工程でマスキングレイヤーとして利用されます。これにより非常に細かいパターンを正確に作りだすことができます。
高温でも安定
酸化膜は高温下でも安定して機能します。これによってデバイスの動作範囲が広がり信頼性の高い製品が作られます。
エッジ部/ノッチ部の膜除去が必要になる理由
ウェーハのエッジ部/ノッチ部に形成される酸化膜は、不均一な厚みや応力が集中して剥がれやすく、デバイスの信頼性や製造プロセスに悪影響を及ぼすことがあります。 また、剥離した膜が装置内に飛散すると不良品の原因や装置の汚染、歩留まりと各プロセスに影響を与えていくためエッジ部/ノッチ部の酸化膜除去は必要不可欠です。
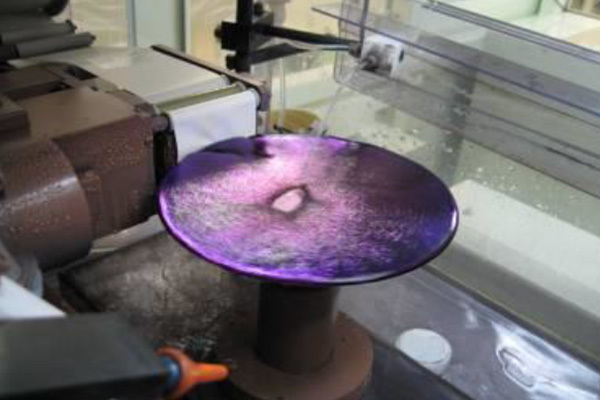
Mipox独自のフィルム式研磨装置による膜除去のよるメリット
・弊社独自のフィルム式研磨装置では高効率かつ高精度なエッジ部/トップエッジ部/ノッチ部の膜除去が可能です。
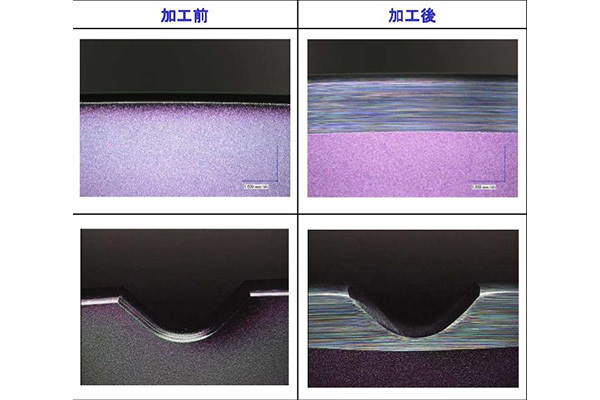
・様々な形状にフレキシブルに対応できます。
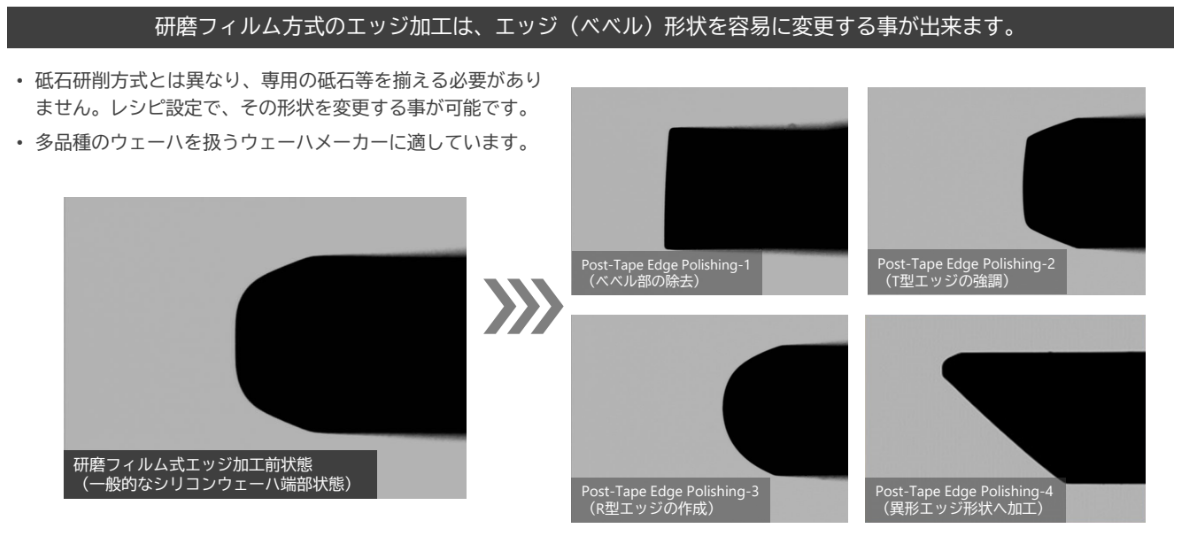
それ以外にもノンケミカル加工で環境に優しく、また自社製の研磨テープを使用するため交換が簡単なため運用が効率になります。
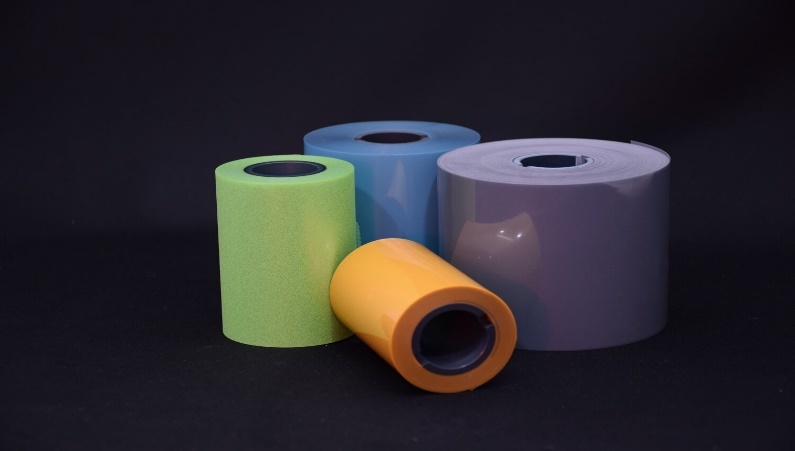
主な装置ラインナップ
-SFF シリーズ: 小型フォームファクターに対応。 -NME シリーズ: 8インチと12インチのウェーハ用に対応。 -HT シリーズ: 高生産効率を実現するモデル。
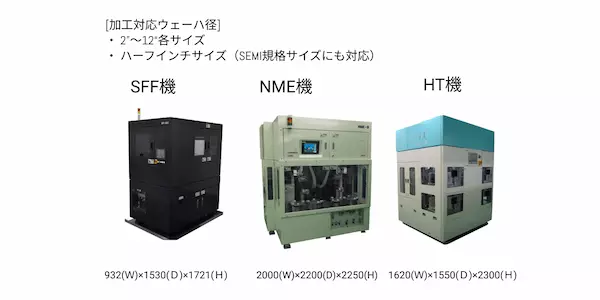
まとめ
ウェーハのエッジ部やノッチ部に付着する不要な膜を除去することは、製品の品質と歩留まりを向上させるために非常に重要です。弊社のフィルム研磨装置は、高精度かつ効率的に不要な膜を除去し、多くの半導体メーカーで実績を上げています。これからもお客様のニーズに応えるため、最先端の技術を提供し続けてまいります。