2000年から2010年頃に急速に普及した携帯電話(フィーチャーフォン、ガラケー、スマートフォン以前の携帯電話)の金属ボディーは、当初は電波を遮るため、携帯電話に使用することが難しいとされていましたが、技術の進歩により実現可能になりました。 今回の記事では、かつてステンレス素材の携帯電話(ガラケー)を手研磨によって研磨加工していた事について説明します。
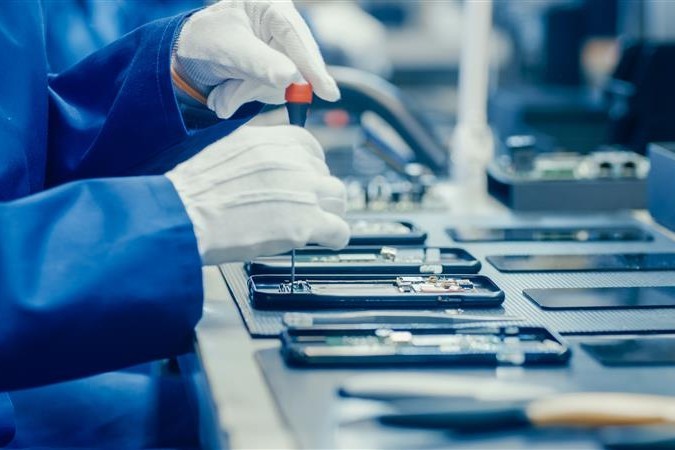
1.携帯電話ボディーケース(金属)の研磨加工の目的
携帯電話は従来、樹脂ボディーが主流でしたが、電化を通す技術(分連続蒸着)により、金属ボディーへの移行が可能となりました。この技術により、金属の特融な高級感あふれるデザインが実現され、携帯電話の外観が大きく変わりました。また、金属ボディーは、ガラケーのデザインや耐久性に大きな影響を与える重要な要素となり、機能と同時に要求度が高いものでした。
2.金属ボディーケースの研磨加工の主な工程
携帯電話ボディーケースの研磨は、以下のような工程があります。
- ボディー(ケース)原板受け入れ作業:(隙間ゲージでの計測)でサイズ不良の排除
- ケースバリ取り作業:プレスキズや返りバリの除去
- 検査:バリ面や表面
- 鏡面研磨:バフ研磨:サイザル等を使用して鏡面まで研磨していく
サイザル(中仕上げ)⇒綿バフ(仕上げ)⇒ネルバフ(超仕上げ) - ヘアライン研磨:不織布製ベルトを使用して均一なヘアラインを付けていく作業
- 洗浄:油分や表面上の不純物を洗浄
- 乾燥
- 外観検査:隙間ゲージでの計測と鏡面度合いの=全数目視検査
- 塗装工程:製品の色を塗装する工程
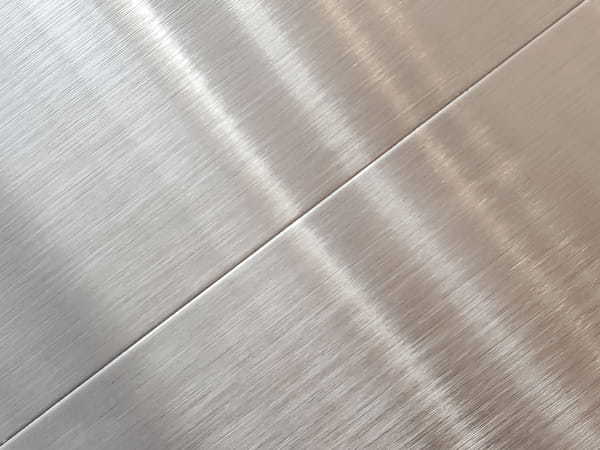
4.研磨材の種類
研磨作業において、使用する研磨材の種類は仕上がりに大きな影響を与えます。ここでは、代表的な研磨材の種類とその特性について説明します。
- 繊維状超弾性研磨材(ホイル):プレス加工された金属板の打ち抜きバリ部除去用として使用。その他(プラップホイル、クロスベルト)
- バフ:サイザル、レーヨン、綿素材のバフを使用し研磨面状況に合わせて使い分ける。研磨剤:青棒、白棒、トリポリ、ライム系
- ヘアライン用研磨材:不織布ベルト(パンチングベルト)等
5.研磨加工の課題
研磨加工は、製品の仕上がりに直結する重要なプロセスですが、さまざまな課題が存在します。以下に、具体的な課題を挙げてみます。
「素材に合わせた研磨手法」
原板自体は精密加工されており、プレス精度のばらつきは0.2mm~0.3mmの為、研磨熱に対して非常に弱い状況でした。そのため、バフの当て方により形状が変形してしまい、不良となってしまう可能性がありました。また、回転数の管理、方向、抑え圧などをマニュアル化して、生産量を上げる必要がありました。
「日当たり生産の重視」
あるメーカーでは、1日当たりの生産を2万個が義務付けられており、30日稼働で合計月60万個を次の工程に送り出さなければなりませんでした。次の工程が停止すると莫大な違約金が発生するため、ラインに入っている作業員の管理が非常に困難でした。
「仕上げ精度」
仕上げ面のばらつきにより塗装時に色むらが発生するため、バフや研磨剤(ライム)の種類等を素材によって使い分けて使用していました。(作業員にマニュアル化して周知)
「検査の重要性」
生産する上で不良を出さないことは重要ですが、次工程に流出させないことも非常に重要な作業になり、研磨工程を請ける企業の最後の信頼性を守る砦といえます。検査は全数、拡大鏡を使用して行います。また、塗装後にしか判別できないような細かい傷、ムラ等を判定していく技術は、まさしく職人技といえます。
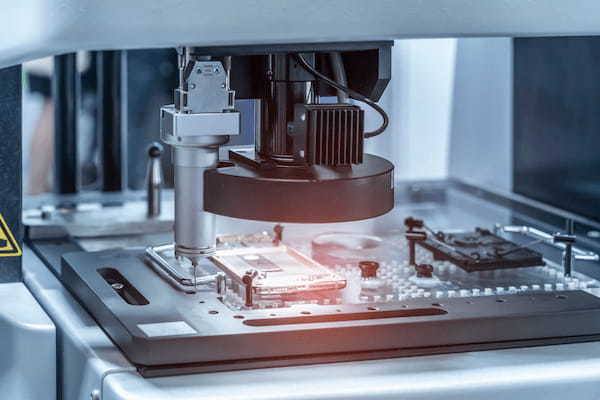
6.まとめ
研磨加工は、金属ボディーの品質を向上させるための重要な工程です。鏡面研磨やヘアライン研磨など自動化が困難な工程は、職人の手研磨によって行われていました。
また、生産効率や仕上げ精度の管理が求められ、特に大量生産が義務付けられる中で、作業員の管理の難しさから、管理者の能力も重要でした。
現在は、スマートフォンにおいてメタルボディーの採用が減少傾向にありますが、数世代前の携帯電話(いわゆるガラケー)における金属ボディーの歴史は、携帯電話のデザインと技術の進化を如実に映し出しています。