製造業の現場では、「環境対応」「作業安全性」「生産性の向上」が重要課題となっています。その中で、溶剤を使わない粉体塗装が、塗装業界の新たな選択肢として注目されています。
粉体塗装の原点と進化
粉体塗装は、もともと厚膜塗装や耐候性・耐薬品性が求められる用途で発展してきました。建材や屋外設備、重機部品、家電筐体など、過酷な環境下での長期耐久性が必要な分野に適していたのです。しかし、近年では膜厚制御技術の進化(新型スプレーガンや粒度制御技術の改良)により、薄膜で均一な塗膜形成が可能になり、これまで不得手とされてきた細かい部品や装飾部材、軽量素材などへの適用も進んでいます。この進化により、粉体塗装は「厚膜・耐久性」の枠を超え、「高精度な薄膜塗装」や「高意匠性」を求める用途でも検討されるようになっています。
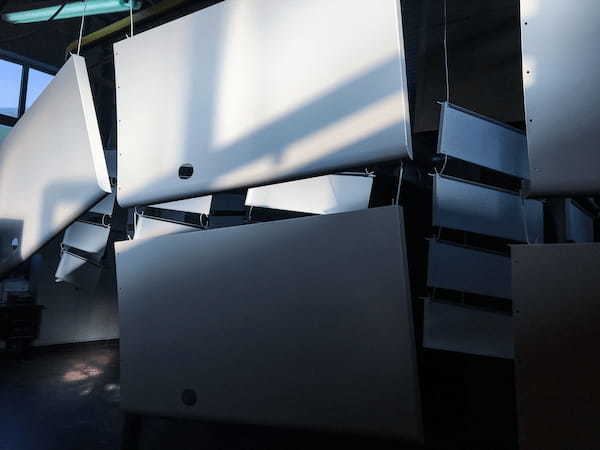
溶剤塗装・水系塗装との比較
従来の溶剤塗装は、作業効率や適用範囲の広さから根強い人気がありますが、VOC排出や火災リスク、健康リスクが課題です。水系塗装はVOC削減に貢献する一方、乾燥時間が長く、塗膜品質の安定性に課題が残ります。 粉体塗装は、塗料自体に溶剤を含まず、VOC排出ゼロに近い環境負荷の低さ、火災リスク低減、塗料の回収・再利用による経済性が特長です。膜厚制御技術の進歩で「粉体=厚膜」のイメージを刷新し、より多様な用途への展開が期待されています。
塗装種別 | シェア(推定) |
---|---|
塗装種別 | 約75~80% |
水系塗装 | 約15~20% |
粉体塗装 | 約5~10% |
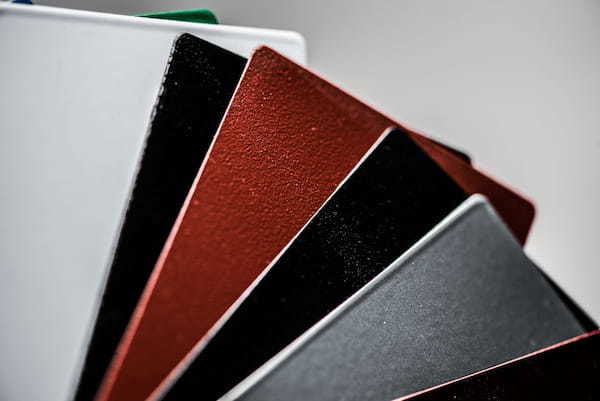
業界動向と導入事例
粉体塗装の市場シェアはまだ一部(約5~10%)ですが、特に自動車部品、農機、建機分野では環境規制や作業効率向上ニーズを背景に導入が進んでいます。例えば建機シャーシや農機具フレーム、車軸、足回り部品では、従来の溶剤塗装では塗膜内の残留溶剤を完全に揮発させるために乾燥工程に時間を要する一方、粉体塗装は塗料自体に揮発成分を含まず、焼付け工程での乾燥が短時間で完了します。これにより、ライン全体の工程時間短縮やVOC排出削減、品質面での均一な塗膜形成と高い耐久性を実現しています。これらの事例は、現場のコスト削減と環境対応の両立に直結する成果を示しています。
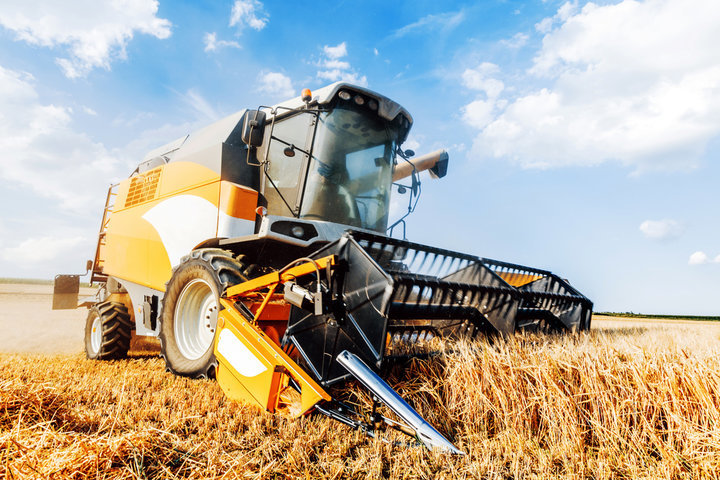
現場目線でのメリットと課題
粉体塗装は、自動化との親和性が高いことも大きな強みです。均一な塗膜形成と短い乾燥時間で、省人化・作業負担軽減、品質安定に寄与します。一方で、専用設備や加熱乾燥設備の初期投資、熱に弱い素材への対応などの課題も残ります。しかし、膜厚制御技術の進歩や自動化技術との融合により、これまで以上に多様な用途への対応が期待されています。
これからの塗装現場に求められる技術
環境負荷削減や省エネの流れは今後さらに加速します。粉体塗装は、これまで厚膜用途に限定されがちだった技術から、溶剤レス・高意匠・薄膜化対応の次世代塗装技術へと進化しています。今後、国内外の環境規制強化や顧客要求の高度化に伴い、粉体塗装は市場全体での存在感をさらに高めていくでしょう。 (※1:市場シェアは推定値。日本塗料工業会資料や業界動向に基づく)
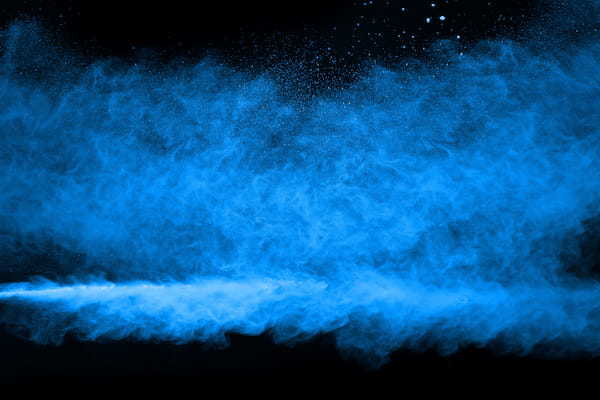