はじめに
ステンレス素材は、高い耐食性・強度・リサイクル性から、厨房設備・建材・化学プラントなど、多くの業界で採用されています。しかしその一方で、硬度が高く「難削材(なんさくざい)」と呼ばれることもあり、研磨加工には高度な技術と多大な労力が求められます。
本記事では、そんなステンレス製缶の研磨工程において、作業負荷を軽減しながら、高品質な仕上がりを実現する弊社の製品をご紹介します。 作業効率と品質の両立を実現したい現場の方は、ぜひ参考にしてください。
初期研削・平面出しに最適な「DRZD-DDSM」
ステンレスの初期研削では、以下の2点が主な課題です。
高硬度ゆえの加工負荷の大きさ
摩擦熱による焼け(変色)の発生
これらを放置すると、表面修正などの手戻り作業が増加し、工数やコストが増大してしまいます。
そこでおすすめするのが、弊社のDRZD-DDSMです。
特長: ジルコニア砥材による高研削力で、ステンレスの平面出しを効率化
DS加工(独自の目詰まり防止処理)により、焼けを防止
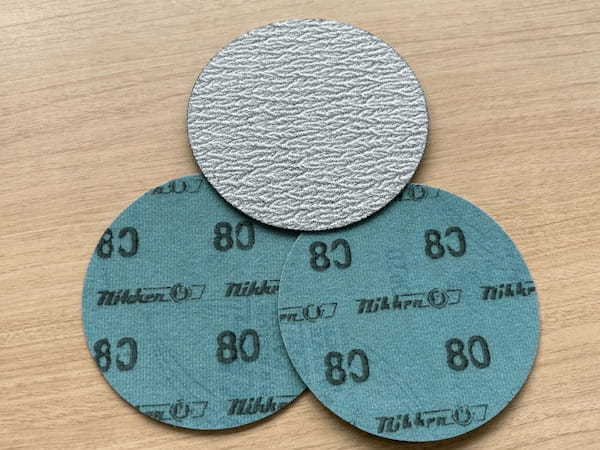
粒度は #60〜#120 まで展開し、用途に応じた選定が可能
難削材や黒皮除去など、高負荷な研削作業でも多くのお客様にご採用いただいています。
ベルトサンダーによる表面・ヘアライン研磨には「レジンクロスベルト」
製缶製品の最終仕上げでは、ベルトサンダーを用いた表面研磨やヘアライン処理が求められるケースが多くあります。 特にヘアライン仕上げは、見た目の高級感を保ちつつ、キズや汚れの目立ちにくさを実現するため、重要な工程です。
ここで活躍するのが、弊社のレジンクロスベルトです。
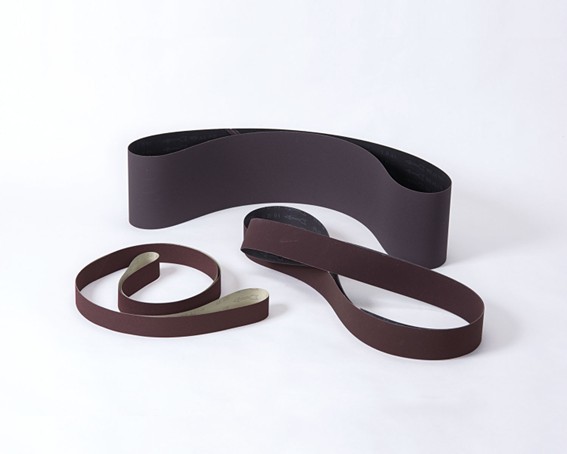
レジンクロスベルトの特長: 基材・砥材・樹脂のカスタマイズが可能
ワーク形状・仕上がり要件に合わせて最適設計
表面均一性と長寿命を両立
お客様ごとの加工内容に応じた提案で、課題解決型のサポートを提供しています。
まとめ:課題解決につながる製品選定を
本記事では、ステンレス製缶の研磨工程でお困りの現場向けに、初期研削から仕上げ研磨まで対応する弊社製品をご紹介しました。
弊社製品の導入メリット 作業効率の向上
作業者の負担軽減
品質の安定化
現場課題の解消
「今の研磨作業、もっと効率化できないか?」 「焼けや手戻りが多くて困っている」
そんなお悩みがあれば、ぜひ一度、下記お問い合わせフォームまたは営業担当までご相談ください。 お客様の課題に寄り添い、最適な製品と加工方法をご提案いたします。