Mipoxの半導体関連ウェーハ向け受託研磨サービスは新製品・新技術開発に貢献します。開発する中で製造設備投資の負担が大きい、時間的効率が悪い、さらには製造・技術開発プロセスを1から進めることが難しいと判断し開発を断念するときもあるのではないでしょうか。
そのような時、外部に製造プロセスを委託する「受託」という選択は打開策としての最良な選択肢の1つになります。Mipoxの受託研磨サービスではお客様に合うベストな材料及び装置で研磨加工ができます。
今回は半導体ウェーハ関連の受託研磨加工をしているMipoxの受託研磨サービスの強みとなる特徴と、どのような技術で素材の加工をしているのかを紹介します。
目次
Mipoxの受託研磨サービス
当社の受託研磨サービスの特徴は大きく分けて以下の3つがあります。
- 研磨加工に必要な大半の材料を 自社製の研磨材や装置の一部は自社製の研磨装置を使用して加工ができること。
- 研磨加工対象において半導体用ウェーハの他、装飾品~金属製圧延ロール材などの部品に至るまで幅広くカバーしていること。
- 各加工材料の特性を知り尽くした専門の技術者によってお客様にとって一番良い条件下で研磨加工ができること。
これらの特徴が当社の大きな強みでありお客様のご要望に合わせ研磨材及び研磨装置を自在に調整、選定することができ、最良な加工結果を得ることを可能にします。
また、研究開発をともなう案件の場合、開発(テスト)~試作、量産化の進捗に応じ、研磨プロセス(ノウハウ)の開示、研磨装置などをともなう技術(設備)移管、量産開始までのサポートも柔軟に対応しているなど、お客様に受け入れられやすい体制を整えています。
代表的な半導体関連ウェーハ向け用途とは
1.セラミックス(多結晶材料、複合材基板)の表面平坦化、精密平面研磨加工
一般的に平面研磨の精度向上に限界があるとされているセラミックの多結晶材料、複合材料(代表的な材料としては窒化アルミニウム、アルミナセラミックス、多結晶SiCなど)に対し、当社は通常のポリシング加工の域を超えた高精度の平面を得ることが可能な加工方法を確立しており、自社の受託研磨加工に適用しています。
セラミックスの精密平面研磨加工は、加工結果が液体研磨剤(スラリー)の性能に依存する割合が高いです。良好な加工面を得るためにはスラリー中の主成分である砥粒(粒子)の粒径分布精密制御とその分散、濃度、及び各材料の配合比率を加工対象物に合わせて最良の配合比率にすることが必要です。
スラリー製造技術は、当社の主力製品である研磨フィルムと共に当社の得意分野であり、主力製品であるHDD向け研磨材の開発によって培われた技術を受託研磨加工にも展開しています。
当社の精密平面研磨加工は、各材料(素材)の新たな用途を作り出すことに貢献しています。例えばSiCを用いたパワーモジュールのヒートシンク機能を担う部品としての新用途や、高出力LED製造用に用いられる高機能ウェーハなどで多くの実績があります
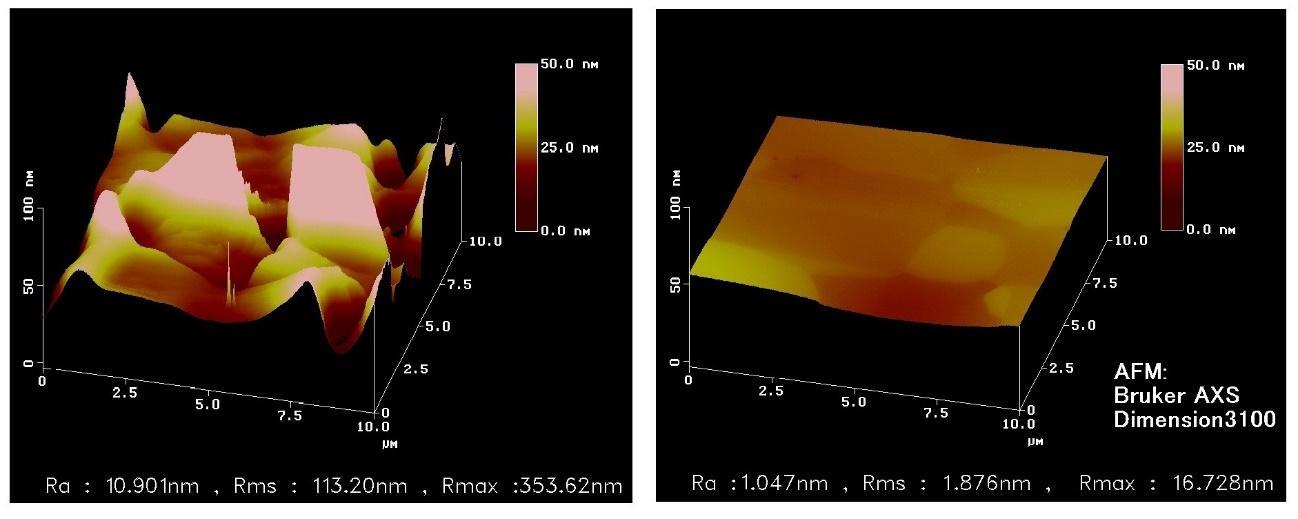
2.パワーデバイス用単結晶基板(GaN ・ SiC)べべリング加工及びミラーエッジ加工
当社の受託研磨サービスでは、平面研磨プロセスと深い関わりをもつエッジ部加工もしており、パワーデバイス単結晶基板用途向けの自社製専用加工機を開発し導入しています。
エッジミラー処理は単結晶シリコンウェーハの製造プロセスではごく一般的となっている状況ですが、単結晶SiCとGaN基板においてはその物性の特徴によって高品質のエッジを高い歩留まりかつ高効率で作成することは困難とされていました。
当社では自社製の研磨材特に「研磨フィルム」を主に適用する加工方法を開発し、べべリング加工、ミラーエッジ化の両プロセスを確立し、単結晶SiC・GaN基板が抱える技術課題を解決しています。
単結晶SiCとGaNウェーハのミラーエッジ化は、ウェーハの強度確保、表面研磨時の安定性向上(エッジ脱落防止)の効果があります。そして、エピタキシャル層生成時の欠陥抑制の効果が確認されている実績があり、近年特に注目されているプロセスの一つです。
また、当社の受託研磨サービスでは、一般的な丸型ウェーハに限定せず、角型ウェーハにも対応しているため、例えばダイシング後の基板に対するべべリング加工も対応可能である事が強みの一つです。
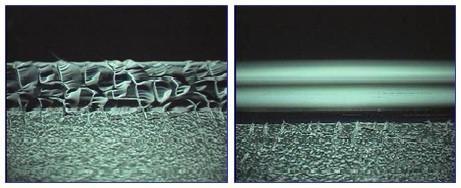
3.エッジトリミング加工(薄化時のウェーハエッジからの割れリスク低減)
ウェーハエッジ部の断面は通常 台形状もしくはR形状になっていることが多いですが、ウェーハを薄化するにつれて次第に鋭利な形状になるため非常に破損しやすい状態となります。
そのため、裏面研削の薄化工程の際に、チッピング(微細クラック)が多数発生し、ウェーハの破損リスクを高めてしまうことが一般的です。しかしながら当社の受託研磨加工サービスでのエッジトリミング処理を施すことにより、そのリスクを大幅に低減させることが可能です。
エッジトリミング加工は、多層の積層をともなうプロセスには不可欠である事に加え、薄研削工程の時間短縮にも効果の高いプロセスです。当社はこのプロセスを、自社製研磨テープを用いた独自の方法で達成しており受託加工として対応しています。
「倣い加工方式」の優位性を活かしたプロセスを採用しているため、元々のウェーハ外周に対し同心を保ったままトリミング処理ができます。
さらにはウェーハに保護テープ(保護膜)が装着されている場合もその影響を受けることなく加工を行うことが可能です。このプロセスはシリコンウェーハ以外にも、破損しやすい化合物半導体(InP)にも応用されています。
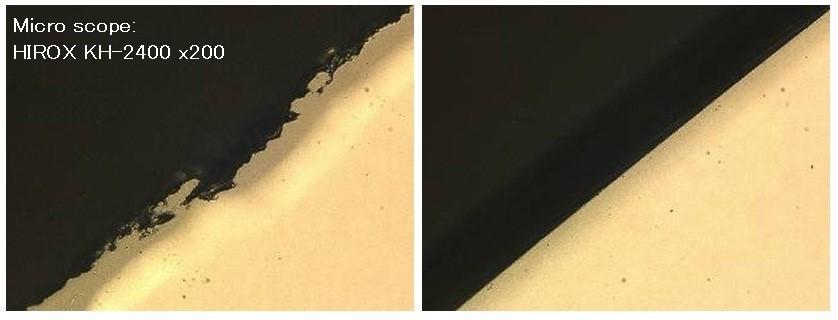
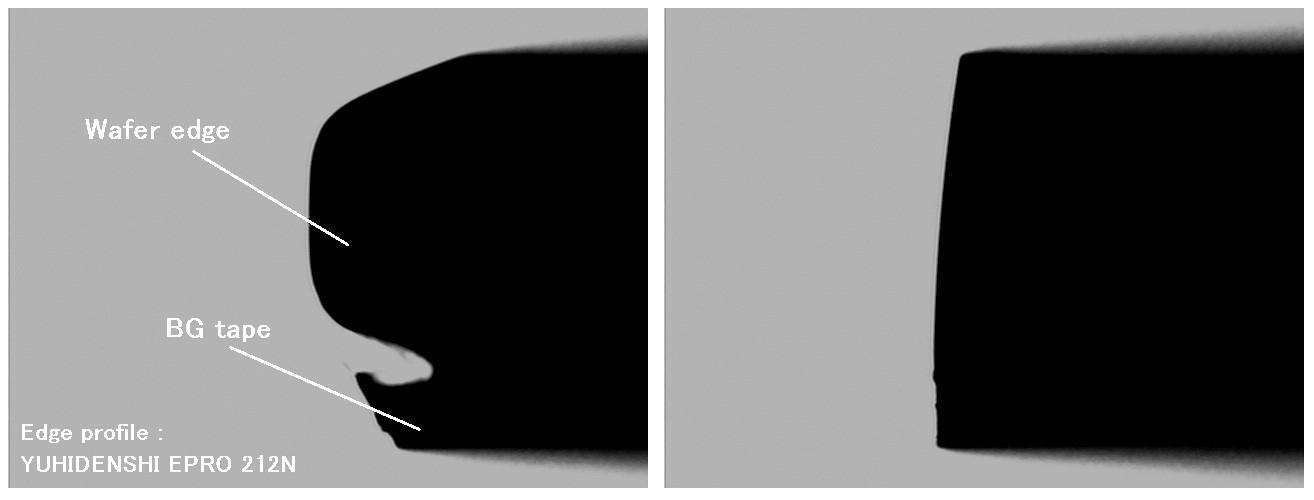
まとめ
上述したように、当社は自社製研磨材を最大限に活用して完成させた研磨プロセスを、幅広い加工対象(領域)をカバーした「受託研磨サービス」として展開しています。
研磨加工は業界を問わず専用の加工機が各メーカーから販売され機械化が進んでいる状況ですが、依然としてノウハウ(経験)に依存する割合が高い状態です。したがってお客様が単独で限られた時間の中で、良好なプロセスを短期間で確立することは効率的に限界があると考えています。
当社はお客様の良好なプロセス確立のサポート的役割を果たすため、自社内で蓄積し続けているプロセス技術(ノウハウ)を「受託研磨サービス」としてオープンにしています。 当社の「受託研磨サービス」が、お客様それぞれの製品開発スピードアップ、新技術開発時の効果的な打開策として貢献できれば幸いです。
Mipox株式会社の事業
当社「Mipox株式会社」は、主力製品の「研磨フィルム・クリーニング用フィルム、液体研磨剤(スラリー)」をはじめとする各種研磨材メーカーです。精密電子用研磨材を主に、長年築き上げてきた研磨材製造技術を応用し「受託事業」へ展開しています。
事業展開としては各種フィルム製造技術を集めた「コーティング受託(受託塗布)」、自社製の各研磨材製品を活用した「受託研磨サービス(受託研磨加工)」、メイン事業である「研磨製品事業」と組合せてお客様へ各製品、サービスを提供しています。