近年、ハイブリッドカー(HV)や電気自動車(EV)は急速に発展をしています。約10年前に策定があった経産省の「次世代自動車戦略研究会」などで取り上げられた「次世代自動車戦略2010」この頃に考えられていたよりハイブリッドカーに関してはより普及しており、EVについてもすでに実用段階、今後より一層の普及が進むことは確実となっています。
目次
自動車内装部品を支える基板の重要性
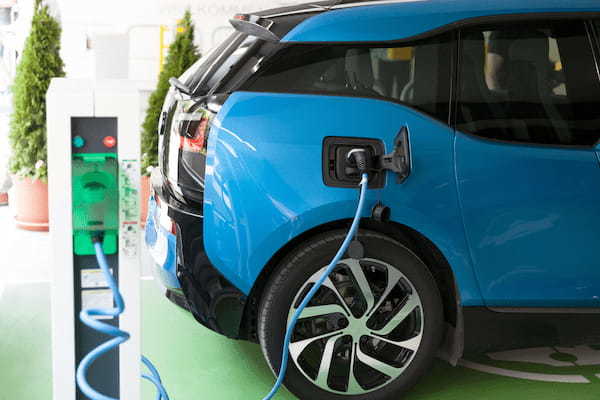
2000年代以前の自動車では畳1枚分と言われていた自動車内部の電子基板は今や2倍以上の面積となっており、今後もさらに増加すると考えています。
理由としては、主に下記の3点があげられます。
- まず、5G・6Gといった高速通信網とリンクすることで考えられる発展
- 二次電池から燃料電池などの一次電池へのパワーソースの革新
- 自動運転技術の高度化・AI制御による操作系の転換
現在、自動車という存在自体が変革の過渡期の真っ最中、と言っても過言ではないでしょう。そんな中で、変わらない存在があります。内装部品を支える基板材料です。もちろん、全く変わらないということはありえません。これら基板材料もまだまだ進化の段階であると考えていますし、将来には3Dプリンティングと電子基板と機械設計がすべて合一のものとなったフレーム内への電子回路の鋳込み技術などもSFの中の夢物語ではなくなっていると考えています。
信号デバイスに使用される基板へのアプローチ
車載基板の中でも、すでに重要な位置を占めているのがECUなどの信号デバイスに使用されている基板です。
現代の自動車は機械的に制御されるよりも電子制御デバイスが圧倒的に多くなっています。また、その電子制御デバイスを構成するチップ内にも電子基板は内包されています。
電子基板の小型化
他にもBluetooth接続のオーディオ・モニター式のインフォメーションメーター・前後のドライブレコーダーやそれに付随するカメラ、コーナーセンサーやクリアランスソナーなど電子部品は増加していますが、その使用面積は膨大ではありません。電子部品や、これを支える基板自体が小さくなっているからです。
※ちなみに、現在、昔ながらの足の生えた電子チップやカーボン抵抗は製造現場では、ほぼ使用されていません。非常にマニアックなオーディオ部材であったり、無理やりハーネス内などに後付けで使用される等にとどまります。
小型化の問題点
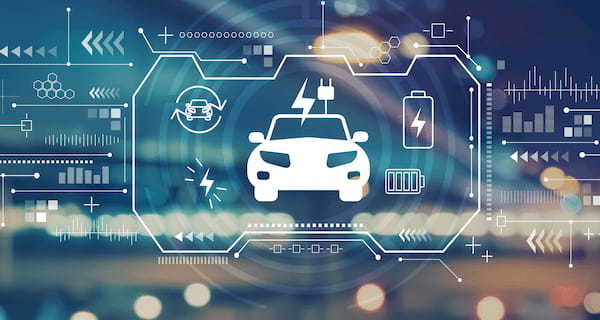
電子基板や電子部品は小型化、高性能化し、その密度を高めて車内に潜んでいます。ですが、信号デバイスというだけあり、小型化することで一つ重要な問題が浮上します。
パターン密度が細かくなることで迷走電流や外部モーター・オルタネーターからのノイズに非常に弱くなります。基板のパターン自体がアンテナの役割をしてしまうのです。また、デバイスの高性能化により高速での信号のやり取りが発生することでパターン設計も気を配る必要があります。
これらの電子基板の基板側からの問題に対するアプローチとしては、こうした迷走電流や異常なノイズの影響を受けないためにも正確な基板パターンの作成が求められます。
それは層間厚みの厳密化、スルーホールのエッジにおける電解銅箔と無電解めっき銅の密着性向上、基板自体のひずみ低減による物理的ストレスの低下などさまざまですが、「設計通りの回路パターンを設計通りに作る」ことが何より重要になります。
電子回路基板製造の課題
電子回路基板を製造する際には様々なストレスが発生します
- 貫通・非貫通のスルーホールを作る際のレーザーやドリルによるストレス
- 孔バリや穴埋めインク除去の際に発生する研磨負荷
- 水洗と水洗後の乾燥による膨張収縮
- パターン形成時の薬品処理による表面脆化・変質
近年の製造課題
特に大きなものが孔バリやインク除去、表面変質層除去のための研磨負荷によるものです。
基板が十分に柔軟であったり、もしくは強靭であれば、これらの物理ストレスは大きな影響を与えないのですが、近年の高密度化で基板は徐々に薄く軽くなりました。また諸々の特性向上の為にも硬くストレスに弱い傾向があります。
たとえば研磨負荷によるひずみ、面厚のムラ、回路パターンの崩れや変形が発生します。
このため、近年は特に研磨負荷を抑えた状態でなるべく研磨工程を終わらせる必要があります。
また、近年重要視されている要件が表面の粗度ではなく、表面の均一性、平坦度です。従来は平坦度に関してはそれほど注目がありませんでしたが、基板厚みの薄化や多層化の影響で平坦度を重要視する必要が大きくなっています。
平坦度を高めるには、工程中のワークに対する裏面とワークの状態のマッチングが重要になります。ワーク状態が良好であれば硬いクロムめっきロールやセラミックコートのロールを使用し、逆にワーク状態が良くない面の場合はウレタンロールを使用するなどワークの状態をそれぞれの工程でよく確認することが重要です。
最適な研磨に必要な研磨製品
最適な研磨をするには、研磨ロールの剛性も重要になります。
まず不織布ロールですが、一般的な不織布ロールには3種類あり、スパイラルホイール・プレスドホイール・フラップホイールが相当します。
スパイラルホイール
スパイラルホイールは構造上中芯に不織布を巻き付け、樹脂を含侵させることで成型されます。このため、樹脂の浸透具合、不織布の密度に左右されますが不織布は基本的に安定した密度に作ることが困難です。このため、性質上剛性の不均一が発生しやすくなります。
プレスドホイール
対してプレスドホイールですが、こちらも不織布の密度に左右はされますが積層することで、ある程度安定した密度に均一化することが可能です。また、スパイラルで避けられない巻きの継ぎ目も存在しません。
フラップホイール
フラップホイールは最も柔軟です。剛性面では他二種類には及びませんが柔軟性は随一です。このため、最も均一な仕上がりとなります。こういった平坦度を求める基板製品に対し、不織布ロールを使用する場合はフラップホイールが最も適しています。
セラミックロール
砥石タイプのいわゆるセラミックロールはどうでしょうか。
セラミックロールは最も重い研磨砥石が最も外周に配置されています。砥石自体の硬さについては問題ありませんが、砥石を支えているゴム層やスポンジ層に問題を抱えているセラミックロールが少なくありません。
良質なセラミックロールではゴム層内に補強布や金属繊維で補強している場合がほとんどですが、安価な製品ではこれらの補強がない場合があります。
通常の一般的な厚い基板に対しては問題ないことが多いですが、平坦度を求める基板製品に対しては大きなエラー原因になる場合があります。回転時にロール形状が変形し、太鼓のように胴部分の径が大きくなる場合が発生します。
こうなってしまう製品の場合、基板の中央部分と両端部分で厚みムラが無視できない場合が多々発生します。弊社セラミックロールタイプではゴム層に補強のための特殊基材をサンドイッチすることでこれらの変形について解消しています。
また、より特殊な製品になりますが弊社FSPシリーズ製品では一般的なセラミックロールと比べてアソビが極めて少なく、極めて均一な仕上がりとなります。平坦度でお困りの場合には一助になればと考えております。ご一報ください。
パワーデバイス の躍進
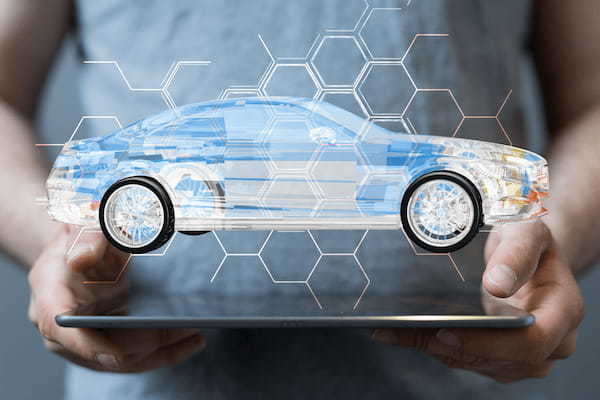
ハイブリッドカーや電気自動車に欠かせないのが近年躍進を見せているパワーデバイスです。パワーデバイスを支えているのもやはり基板です。
通常のデバイスとパワーデバイスの差は何といっても出力です。通常の半導体部品とは数桁違う負荷耐性があります。もちろん、支えている基板もやはり特別性です。
例えばパワーLEDですが、通常の一般的な高輝度LEDと比較するとパワーLEDが0.5A~数Aを入力できることに対し、普通のLEDは20mA程度が一般的です。
入力電圧はほぼ変わらないことから数十倍の負荷がかかっています。これらを支えるのは高放熱基板であり、基板パターンがそもそも分厚い高銅厚基板です。高放熱基板は例えばアルミベースやアルミナベースの耐熱性の高いベース材と絶縁材・銅箔で作られています。
または、チップ裏の放熱パッド部分に直接メタルパッドをソルダリングできるような設計になっています。
高銅厚基板はそのまま回路パターンが非常に分厚くなっています。高電流が流れる際にジュール熱(Q=RI2t)が発生しますが、この回路パターンの銅厚みを増やすことで回路内の単純な抵抗を減らすことで基板自体からの熱の発生を防ぐ設計となっています。
パワーデバイスの問題点
これらのパワーデバイス向け基板ですが様々な問題があります。前述の信号向け基板と異なり、まず基本的に銅厚が厚いこと自体が問題になります。パターン形成後に表面の清浄化をする工程では銅厚が厚いことで引っ掛かりが発生します。パターン自体が洗濯板のような効果を発揮してしまい、引っ掛かりによるパターンの変形、研磨ロールの過摩耗、異物の挟み込み等が発生します。また、基板の放熱設計上、今後、基板材料に放熱対策として硬質材料を添加する必要が増えます。
最後に、基板の凹凸が増えた状態で多層構造を作る必要があります。この際のレベル出しや構造体内部のボイド問題が現在以上に増加する見込みがあります。弊社でもこれらパワーデバイス向け開発を随時進めております。
HV・EVの今後の方向性
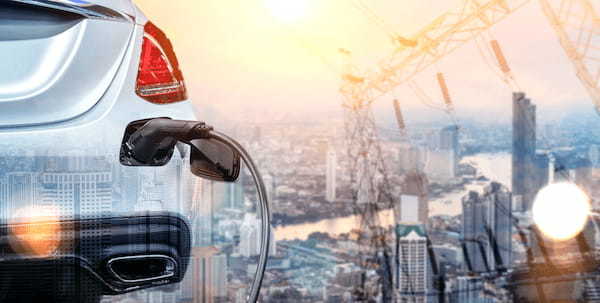
今後益々HV・EVは加速度的に増加が見込まれています。ここに5G・6Gなどの高速通信技術と自動運転技術が組み合わさることで外部データセンターでのモビリティの遠隔制御が実現すると考えています。
このためにも電気自動車の信頼性を高めることが先決となります。電気自動車の信頼性の核心部分は半導体部品ですが、これらを支える基板製品も非常に重要です。また半導体部品自体に内包される基板(パッケージ基板)も小型化、高精度化が求められています。今後の社会や未来の為に私たちMipoxは塗る切る磨くで世界を変えていきます。今後ともよろしくお願い申し上げます。