水槽製造のメーカーA社では、平面研磨での作業時間短縮、コスト削減(ダイヤ研磨材単価・作業人件費)及び現場施工時の作業員によるスクラッチ対策の2点について課題を抱えていました。今回は、A社での当社及び競合メーカーの対策を絡めながら述べていきます。
アクリル水槽を研磨加工する重要性とは
まず、水槽のアクリル樹脂をなぜ研磨行うのかについてですが、2つの必要性があります。
1つ目は平滑性の向上、2つ目は透明度の向上、この2つのクオリティーを上げることで、水族館で魚、サンゴ礁。水草などを美しく見ることができます。
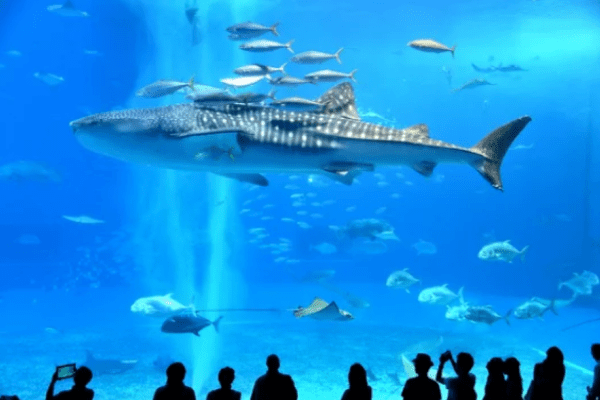
アクリル水槽の研磨工程では、初めに門型の据え置き研磨装置の超硬刃で平滑性を出していきます。
そのあとにダイヤ電着研磨材で研磨を行い平面の透明度を出していきます。この工程は透明なアクリルに仕上げるのにとても重要な工程となります。
その後、手作業で研磨職人により曲面箇所の研磨、透明度アップの順で作業を行っていきますが、当社のダイヤ研磨材、耐水研磨シートなどが重要な役割を果たしています。
平面研磨工程
アクリル水槽研磨工程はおおまかに平面と曲面の二つに分けられます。
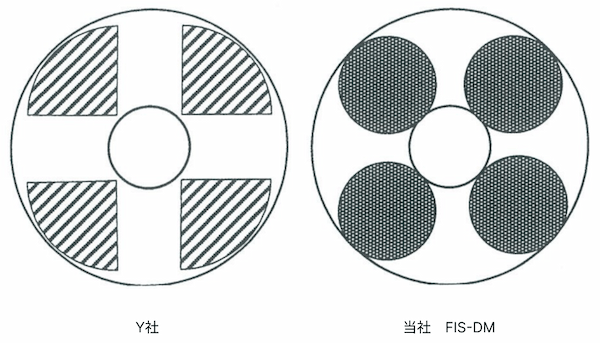
- 当社電着ダイヤ研磨材FIS‐DM 75φ#100
- X社電着ダイヤ 200φx50(中心穴)#200#400#800#1000
- 当社RRCC-S#600#800##1000
- X社各種コンパウンド
平面工程
この工程は、仕入れたアクリルパネルの表面の凹凸を平らにする最も重要な作業です。
研磨には、床研磨機を独自に改良した専用機を使い研磨していきます。A社は工程3.で手研磨工程に作業員を確保したく、この工程での研磨力を重要視しておられました。以前は、Y社ダイヤ研磨材パット180φを1/4にカットして図2のように使用しておられました。しかし、当社製品FIS‐DMはより研磨力があり、作業時間をY社比1/4に短縮できたため採用に至りました。
自動研磨工程
トライ品FIS‐DM 75φ 各粒度ランニングコストを考えX社サイズ200φ中心穴50φに対し、75φ5枚貼り付けによる研磨法を提案しました。(図3参照)
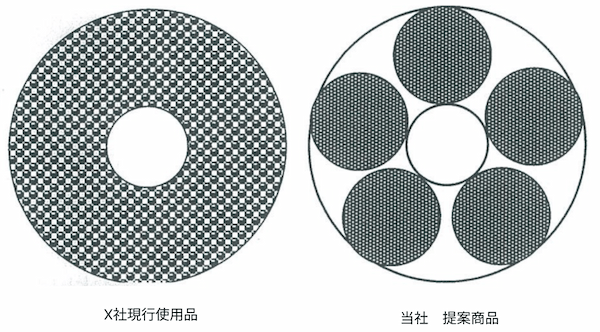
狙い通り、コスト面は抑え、研磨力良好・耐久性同レベルの製品を実現しましたが、マジック剥がれが発生しNGとなりました。原因としては、図4のように研ぎ漏れのないよう設定しているため★部分がアクリル板エッジ部に引っ掛かりパットから剝がれたようです。
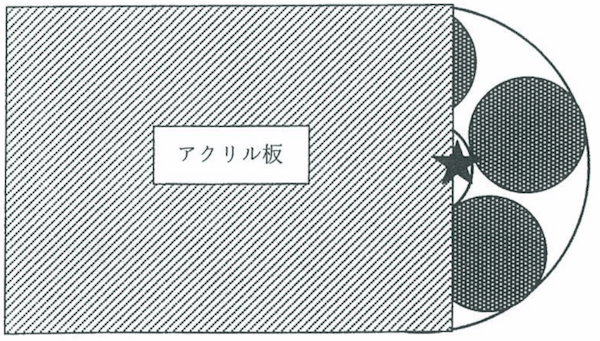
問題なく研磨できる場合もありますが、エッジ部に引っ掛かった際のダメージが大きく、安定して研磨できるX社現行品の方が扱い易いとの評価となりました。当社製品は、装置設定も10cm単位と非常に大まかな装置の為、設定値も調整不可という結果になりました。工程1.の作業時間の短縮、コストダウンを実現したにも関わらず採用には至りませんでした。
手研磨工程
磨き工程前の最終段階でスクラッチ等のキズは致命的です。115x280サイズのサンダーと手作業による研磨を行います。以前使用していたX社水研ぎシートソフトタイプは、カールが原因で#800・#1000で度々スクラッチが発生していました。しかし、当社製品RRCC-Sをサンプリングしたところ、ソフトバック基材を採用した抜群のフィット感とカールしにくい特徴を生かした使用感でスクラッチの発生率はかなり減りました。
R面研磨工程
R面の研磨は研磨装置による自動研磨ができない為、どんな広い面積であっても作業員が手作業で研磨にあたります。
- Z社ソフトバック耐水研磨紙#120
- 当社RRCC-S#240#320
- 当社RRCC-S#400#600#800#1000
- WRAC-DM 150φ6穴 #400#600#800#1000
- X社各種コンパウンド
詳細説明と取り組み
耐水ペーパーの工程は平面研磨工程同様、X社水研ぎシートソフトタイプから大部分を当社製品への切り替えに成功しました。しかし、工程1.の#120はRRCC-Sシリーズに規格がなくX社のままでした。WTCC-Sでテストを行うも基材が硬く、馴染みにくいためNGとなりました。その後、Z社がソフトセミ耐水研磨紙を開発。テストを行いX社製より追随性良く研磨力良好との結果で採用されました。その後、当社のRRCC-S対抗でテストを行うもカールによるスクラッチが原因で切り替えに至っておりません。
工程4.での使い分けに関しては、R面の外面、内面によって異なります。外R研磨時は耐水研磨紙を使用し、内R面研磨時は耐水ペーパーエッジでのスクラッチを防ぐため中間クッショナーを入れてWRAC-DMを使用していました。しかし、現在WRAC工程はZ社の柔軟フィルム研磨材を使用しています。詳細はこのあとの「現場納入後の作業」にてご説明します。
現場納入後の作業
アクリルパネルは納入後、水槽の形に組み立てる作業があるため研磨作業があります。※図5参照 作業内容としては、組み立て作業時に発生した接着剤のカス除去の為、直角面を工程4.から再研磨を行います。直角ギリギリのところまで研磨処理を施しますが、ペーパーエッジ部分が、少しでも横の立ち上がり面に触れてしまうとスクラッチが発生してしまう為、ペーパーの工夫で解決できないかと相談がありました。
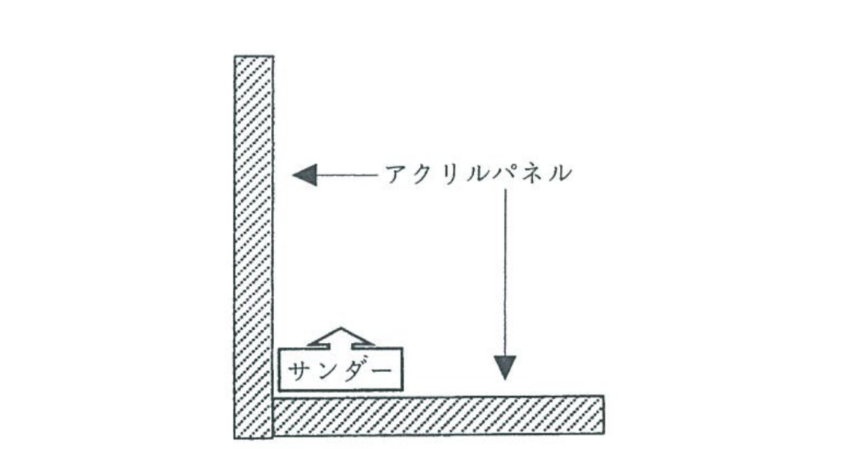
そこへZ社が柔軟フィルム研磨材中目・細目125φとD社揺動サンダーとセットで持ち込みテストをしました。 結果、柔軟フィルム研磨材シリーズの柔軟性が活かされ、立ち上がり面に触れてもスクラッチが起こる確率が減りました。その上、工程4.をZ社柔軟フィルム研磨材シリーズの2つの工程でカバーでき、省力化できたと高評価を得て、それに伴いR面研磨時もZ社品に変更となりました。
当社の対策SUWF-DLM試作品の開発
当社の中でも最も薄いフィルム基材を使用した製品で追随性を強化しました。特殊砥材を使用し作業性アップ、砥材率もオープンにして目詰まり対策を行った製品です。通常規格#240までありますが、試作品として#500#600#800を製造してトライを行いました。
結果、紙基材のWRACよりかなり追随性は改善されましたが、Z社製の柔軟フィルム研磨材には及ばず、採用には至りませんでした。ただ、研磨性能ではZ社柔軟フィルム研磨材よりも優位性が認められました。
今回、切り替えには至りませんでしたが、他のアクリル研磨ユーザーなどにも横展開できる可能性を確認できたのは、大きな収穫でした。
最後に
以上、アクリル水槽研磨について述べてきましたが、今回例に出したA社では、平面研磨での作業時間短縮及び作業コスト削減についての課題は当社提案により解決できました。
ただ、現場施工時のスクラッチ対策では、Z社に後れを取ってしまった結果となりました。しかし、今回試作したSUWF-DLM#500#600#800は、平面もしくは緩やかな局面形状のアクリル板に対しては有効と思われます。
このように当社含めた研磨材業界では他社と技術競争を行いながら技術向上を加速させていきます。今後のMipoxの動向にご注目下さい。