3次元CADデータを実際の立体として造形することができる「3Dプリンター」は、建築・デザイン・ファッション業界から義足等の義肢装具(医療)、自動車(機械)、個人向けのホビー用途に至るまで、広い分野で使用されています。 3D造形の技術自体は数十年以上前から存在しますが、プリンター本体の機能向上や低価格化により、さらに身近なものになってきています。 今回は、現在主流の”平滑化方法”である「研磨布紙」を使用した研磨方式とその効果・問題点、またもう一つの“溶解方式”について説明します。
3Dプリンターの“now”
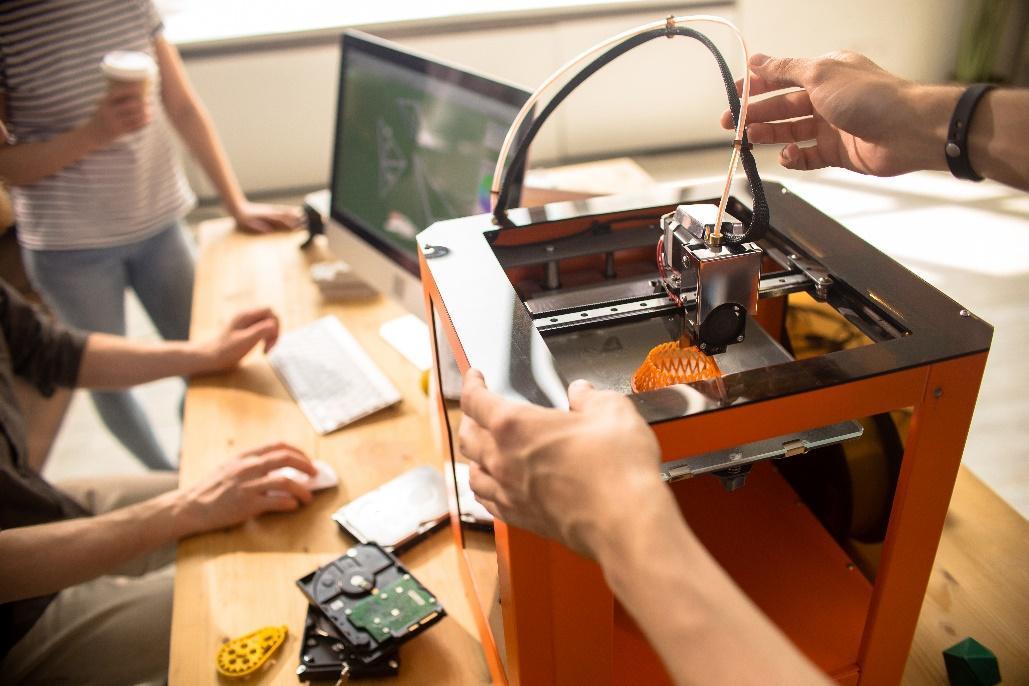
3Dプリンターのメリットは「造形の自由度が非常に高い」ところにあります。一体成形(一度の造形)で加工が完結することや、従来の切削などの加工方法では不可能とされてきた中空形状の造形についても特別な技術(ノウハウ)が無くても作成できるようになりました。
中空造形が可能となったメリットは大きく、航空産業向けや自動車向けの部品に対しワンランク上の強度や大幅な軽量化が可能となりました。加えて、試作品から量産に至るまでのモノづくりには不可欠とされてきた「金型」が関わる工程に対しても大幅な時間短縮とコストダウンが実現可能となり、生産現場とも相性が非常に良いです。
3Dプリンター技術の現状
一見万能に見える3Dプリンター(3D積層造形)ですが、実際はユーザーの期待に応えきれていないのが現状です。特に造形後の「表面状態(外観)の悪さ」と、「平滑化処理(滑らかにする対策)の困難さ」にユーザーが落胆することが多く、3Dプリンター技術の魅力を損なわせている大きな原因の一つになっています。
モノづくりにおける「試作品」や「デザインモデル(製品イメージ先行確認用)」は、3D造形物の表面精度(粗さ精度)の高さが要求されます。しかし現在の3D造形技術では「表面の状態」や「質感」をコントロールすることは難しく、用途の目的(要求)を満たすことは困難と言わざるを得ません。
また、耐久性が求められる金属素材等のプロダクション系造形物についても、3D造形したそのままの表面状態では強度が著しく低下し、製品寿命が期待出来ない等の影響が懸念されます。その為、プロトタイプ・デザインモデルとしての品質(精度)を向上させた方が良いという認識が一般的です。
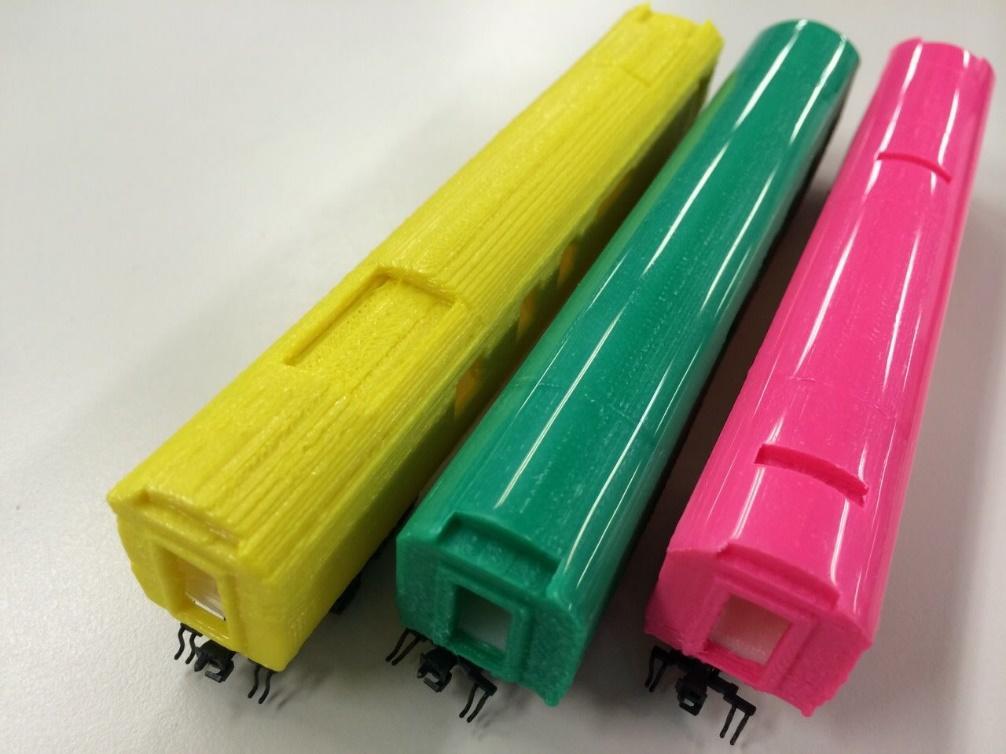
3Dプリント造形技術の問題点
形方式によりその影響度合いの差はありますが、どの方式でも造形をおこなうプロセスで積み重ねた層が段状になり「積層痕(せきそうこん)」として表面に残ります。この積層痕は3Dプリント造形物の表面品質を悪化させている主な原因となっています。 粉体焼結方式の場合は粉末状の原料にレーザーを当てて焼結させ立体を造形していくため、焼結させた箇所と接している粉体が造形物に転写され、造形物の表面がさらに粗くなる傾向にあります。
ほぼ全ての造形方式が立体断面を平面にプリントし、素材を積み重ねて行く方法を採用しています。
3Dプリントの造形方式 | 素材 |
---|---|
A)FDM(熱溶解積層法)
B)インクジェット C)粉体焼結方式 |
1 ABS
2 PLA 3 アクリル 4 ナイロン 5 チタン |
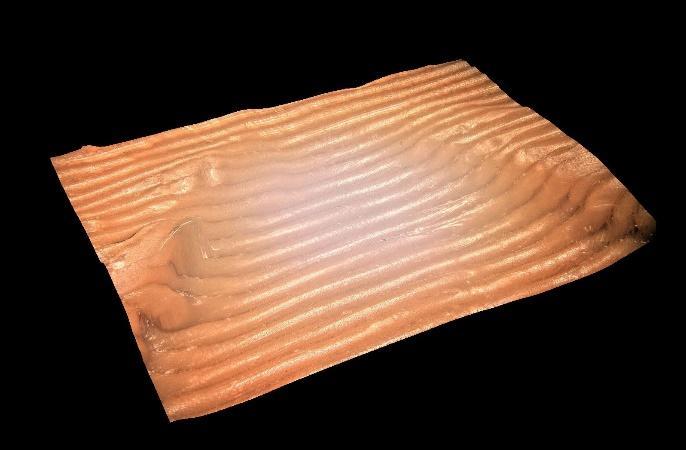
3Dプリント造形物表面の平滑化方法
積層痕を除去する方法は大きく分けて2つ
1 造形物の表面を削り取る方法「研磨方式(微小切削)」
2 熱や化学反応を利用した「溶解方式(表面流動)」 ※ABS材等の樹脂素材に限定
パテ等を使用した塗布(塗装)方式も存在しますが、目的が全く異なるため今回の説明からは除外します。
研磨方式
前述した3Dプリント造形技術の特徴(優位点)により、造形物の形状が複雑であることが多くなります。 また、3Dデータ上の設計寸法と実造形物の寸法差異(収縮、ひけ等の変形)の影響を受けるため、その形状や変位(変形)に追従する事ができる柔軟性、弾性に富んだ工具(研磨材)が適当であり、通常は研磨フィルム等の「研磨布紙」が用いられます。
・有機溶剤や薬品を使用しないため、通常の環境下(屋内)で作業が可能
・研磨布紙の種類(番手)の選択によって、研磨面の品質を自在に変更可能
・研磨加工量(寸法精度)を比較的自由にコントロールできる
・3D造形時の歪(ひけ、収縮など)を修正することが可能
・研磨加工が必要な部位(箇所)に限定し加工することが可能
・作業効率は溶解方式と比較して悪い。非常に細かい箇所への適用が困難
溶解方式
アセトンの有機溶剤を用い、造形物表面へ塗布、又はその溶剤中、又はその雰囲気中へ直接投入し、表面を溶かして造形物表面の平滑化を図る方法があります。 また、高温の雰囲気中へ投入し、熱による溶解(平滑化)を促す2つの方法が一般的です。溶解方式の処理を効率的(効果的)に行うため、溶解処理前に予め研磨布紙による平滑化を施す場合もあります。
・揮発性の高い溶剤を使用するため、取扱い(特に人体への影響)に注意が必要
・処理後の表面粗さ(精度)をコントロールすることが困難
・溶解により造形物が多少変形する。形状(寸法)修正能力は無い
・造形物の全ての表面を処理
・不必要な箇所まで処理
・作業(処理)効率は研磨方式と比べて高い
・造形物の細部まで平滑化処理が行き届く
今後3Dプリンターの「個人ユーザー」は膨大な市場となる可能性を持っています。しかし個人ユーザーは勿論、企業の現場(工場)のどちらにおいても有機溶剤等の危険物を用いるプロセスは望ましくないのが現状です。そのため「研磨布紙」を用いた研磨方式が造形方式を問わず主流となっています。
3Dプリント造形物専用研磨材
市販されているサンドペーパー(紙やすり)やベルト状に成形された研磨材(サンダー)等の一般的な研磨布紙を用いることで造形物表面の平滑化(表面を滑らかにする)はある程度可能ですが、研磨表面の毛羽立ち、白化現象が発生します。そのため光沢を放つような高品位の表面に仕上げることは困難です。 この場合「3Dプリント造形物専用」の研磨材を用いることで、容易にかつ高効率で高精度の表面を仕上げることが可能です。 図2は3Dプリント造形物本用途で標準品となっているMipoxの研磨材「TuneD3(チューンドスリー)」で加工した事例を図2に示します。FDM方式ABS材を用いた造形物に対し高品位な平滑化を達成しています。

3Dプリント造形物専用に設計されたTuenD3は、一般的な研磨布紙とはその構造が大きく異なります。 3Dプリント造形物用途に最適な弾性をもたせ、研磨くずを自ら取り込む機構(吸着口)を研磨材表面に設けることで、「表面仕上げ」の問題を大幅に改善、高品位な表面を簡単に仕上げられるようになっております。 さらに、研磨加工中に適度な摩擦熱が確保(維持)されることにより溶解作用が促進され、研磨方式・溶解方式を併せ持つ研磨メカニズムを得られるようにしています。
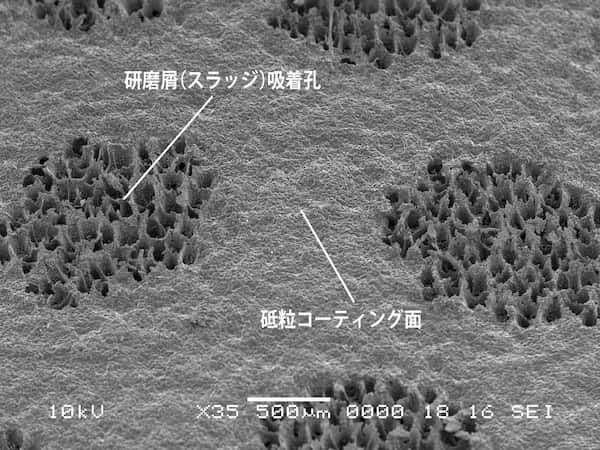
3D造形物の高精度(鏡面研磨)加工は、特に透明アクリル材(図4参照)を用いた造形物に求められることが多くなってきております。 今後進むと思われるレンズ等の光学部品の3D造形技術に対しその期待が高いです。 研磨方式の欠点である、作業性の悪さを補うためのツール開発も進んでおります。 研磨布紙を効率良く機能させるための新機構設計、ロボット等を使用した自動化の検討も進められており、弊社においても積極的に取り組んでいます。
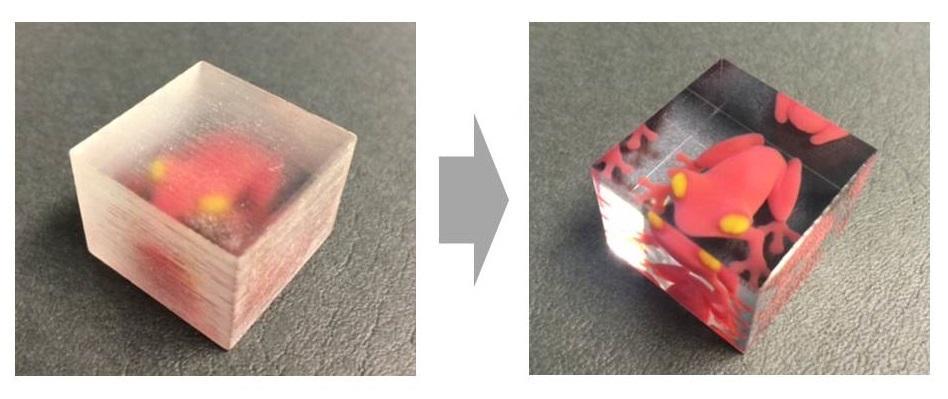
3Dプリント向け研磨材
Mipoxの研磨材及びプロセスは、今回紹介した3Dプリンター用途の他、自動車業界からデータストレージ関連、医療機器関連に至るまで、多種多様の業種、工程で採用を頂いています。 研磨という限られた領域(技術)ではありますが、私たちが今日まで築き上げてきた技術を通じて、3Dプリント技術の魅力を最大限に引出し 魅力溢れる本市場形成の一端を担えれば幸いです。
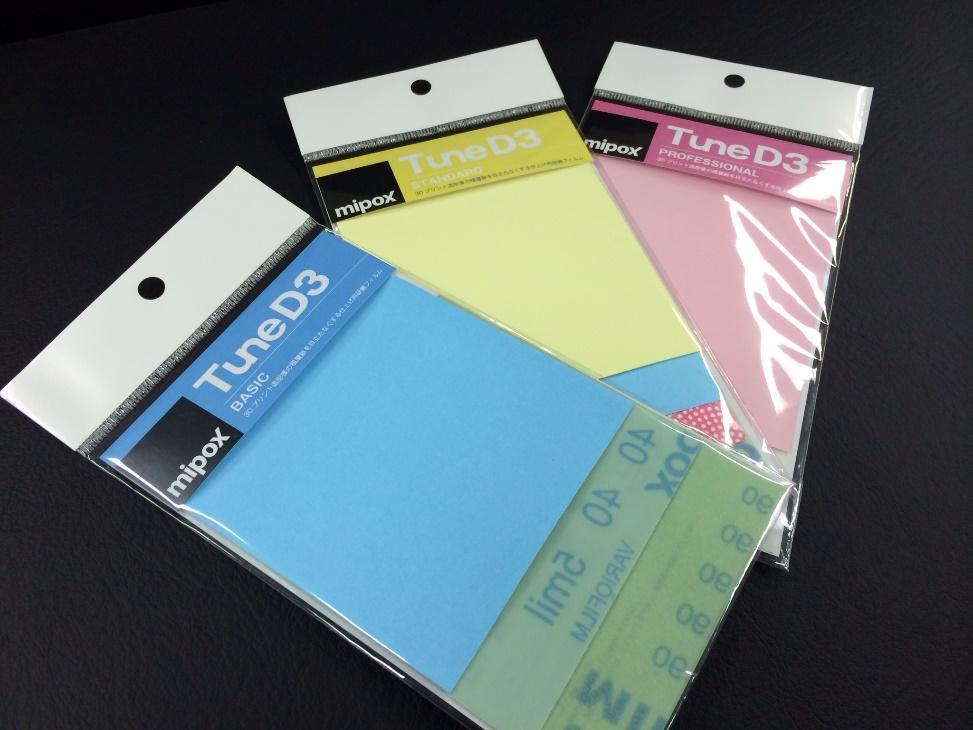