さまざまな木工塗装製品における樹脂塗膜の鏡面仕上げに欠かすことのできないバフについてスポットを当ててみたいと思います。 木工樹脂塗膜とは、主にギター、ピアノ、自動車木目調内装パネル、キッチン家具などで多用されるポリエステル樹脂クリアー塗膜のこと。本記事ではその特性を踏まえた鏡面研磨仕上げ用バフの開発や改良方法をご紹介します。
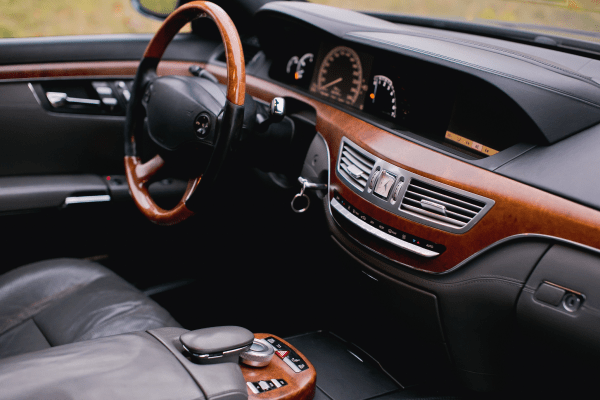
バフの種類と特性
一口にバフといっても多種多様であり簡明に分類し示すことは困難ですが、バフの種類と特性を理解する上で考慮すべき分類要素は次のようになります。
- 構成要素
- 基材
- 縫い方
- 処理法
それでは、一つ一つ詳しく見ていきましょう。
1.構成要素
ばらバフ、バイヤスバフ、鉄バフ、縫いバフなど、その形状・構造を表しています。
2.基材
綿布、サイザル麻布などの使用材料をいいます。 バフの剛性、弾性と直接的に関係し、また基材の吸水性といったような性質は接着性または接着剤との親和性、あるいは研磨剤の保持性能などの特性に関係します。
3.縫い方
ミシンがけの方式で、渦巻き状、同心円状などをいいます。 ミシン目の間隔によってバフの硬さを変えることができ、研磨時のなじみ性や仕上げに合わせ調節できます。
4.処理法
基材処理法のことで、樹脂加工や薬剤処理によってバフの耐久性、研磨力、バフ研磨剤の保持力、潤滑性などを向上させます。
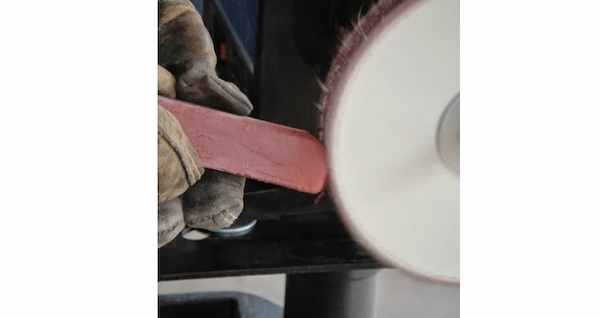
Y社での取り組み
Y社は木目調ウッドパネルを製造しているメーカーです。同ユーザーを担当し、バフの問題点に向き合い対応したことで、知識と経験を得ることとなりました。 そこで、ここからはY社でのバフの改良活動をご紹介したいと思います。 研磨としてはポリエステル塗装面のサンディングとバフ鏡面仕上げをおこなっています。バフは2種類の綿バフが使用されています。 ロボットおよび手掛けバフにユニットタイプ、最終仕上げの手掛けバフにはバイヤスタイプが使用されております。それぞれのバフの仕様と研磨工程をご紹介いたします。
ユニットタイプ:フラップバフ FF-40 405x130
バイヤスカットした綿布を使用し、多数の指状単位体(ユニット)を放射線状に円板または円環に固定したタイプのバフです。 ユニットの幅、長さ、折り方、ユニット数、植え込み方、ミシンがけの本数などを選定することでバフ自体の硬軟の程度をいろいろと変えることができます。 またこのバフは、複雑な形状や湾曲面をもった加工物に対し、特に有効です。空冷作用にも優れています。
バイヤスタイプ:バイヤスバフ F6-16P 405x125
バイヤスカットした綿布の縦糸、横糸の方向がバフの外周に対し45度になるように構成されていますので、外周布端のほつれが少なく、ばらバフ、縫いバフなどに比べ減耗の程度が著しく少なく、また空冷作用、研磨剤保持力も高い万能性の高いバフです。
Y社でも仕上がりの良さと全体的なバランスの良さが作業者に好評で最終仕上げに使用されています。研磨剤はトリポリ白です。
またF6という表示はバフの側面から見た際の金具外周部のひだの数を示しています。0から10までの設定になっており、数字が大きくなるほどバフのコシが強くなり、研磨力がアップします。
研磨工程
- サンディング DRCC-BDS P500、P600 100x5700
- バフ(ロボット)ユニットタイプ:フラップバフ FF-40 405x130
- バフ(手掛け)ユニットタイプ:フラップバフ FF-40 405x130
- バフ(手掛け) バイヤスタイプ:バイヤスバフ F6-16P 405x125
Y社で発生したバフに対する課題
Y社において、これらバフに対する課題が発生しました。それはロボットでのユニットタイプバフ研磨時における仕上げ不良の発生でした。
前工程のペーパー目が残ってしまう、全体的に艶が出ていないなどの歩留まり悪化を招いてしまいました。
採用テスト当初から懸念はされていましたが、量産に入って顕著になった現象です。
調査の結果、バフ自体のコシが若干弱いことに原因があることが分かりました。ロボットによるバフ研磨圧に対し剛性が不足し、コシ抜けが発生し度々自動停止することもあったようです。
また、バフ自体の摩耗においても部分的にアンバランス(摩耗面がギザギザ、凸凹)になることも判明しました。手掛けバフでは、作業者の職人的技術で自然と調整が利いていたようで問題とはなっていませんでした。
Y社で取り組んだ改善策
ロボットでのバフ作業に対応するため、バフメーカーとも協議を行いました。
綿布の糸の打込み本数の変更や糸の太さの変更も考えましたが、Y社のみの特別品になってしまうこと、また現行価格を維持する必要性などから、最終的には一番リスクの少ないユニットの組み方を変更する方法を選択しました。
具体的には、バフユニット各ブロックの根元部分の重なり代を増やし厚みを持たせることによって剛性をアップさせる方法をとりました。
また、摩耗バランス不良に関しては、原因を追究していく中で、各ブロックの植え込み角度が大きく関係していることが分かってきました。
従来品は各ブロックが中心ファイバーに対しほぼまっすぐに立った状態でありましたが、各ブロックの間が布残りする(ギザギザの原因)傾向にあることも判明しました。
布残りに関しては、ロボット研磨における各ブロックのワークへの入り角度が影響していると考えました。
そこで最適な角度を求めるため、Y社の協力のもと試作品テストを繰り返し一定の成果が認められる角度を見出し、リニューアルしました。
最終的には従来に比べて、摩耗がより均一化され、バランスの改善を図ることができました。
この2点の改善により、ロボットでのバフ作業に対応することができるようになりました。
まとめ
Y社でのバフの課題解決により、前工程のサンディングと合わせ塗装面研磨の一貫工程での研磨材供給を果たすことができました。
サンディングにおいてはストロークサンダーで使用される研磨紙ベルトDRCC-BDS P500 100x5700 帯電防止タイプを中心にスポンジサンダーとダブルアクションサンダー用の研磨材を提案し採用となりました。
鏡面仕上げバフを手掛けることにより、従来に比べ、よりサンディングの重要性と方向性が明確になるという相乗効果も経験できました。
また研磨工程をトータルでサポートすることにより、顧客満足度の充実にもつながった案件であったと言えます。
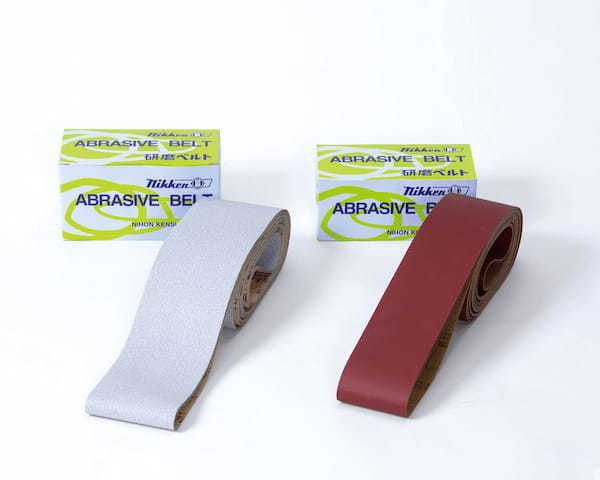