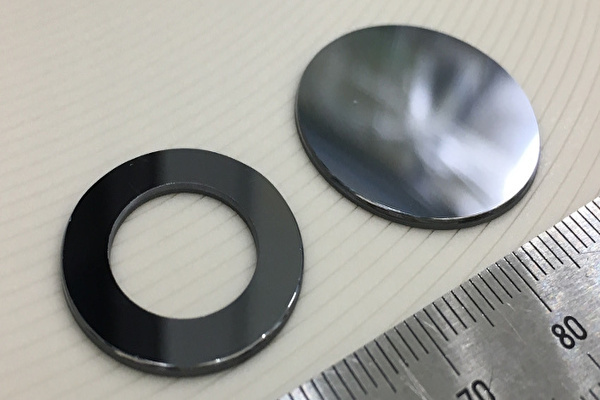
半導体製造のコストダウン・生産効率の向上などを主な目的とし、大口径化の一途を辿ってきた半導体用基板(シリコンウェーハなど)ですが、その一方で少量生産・試作に適した極小径寸法規格のウェーハ(ハーフインチ)を用いた工法があり、その存在感は年々増しています。同じ用途専用の製造設備にも力を入れるようになり、
国内外で開催されている半導体製造装置・材料関連の展示会でも注目されています。
ハーフインチウェーハ(規格外小径サイズウェーハ)を使用するメリットは
「半導体製造に必要なユーティリティコスト(クリーン環境の維持)の低減」
「試作時の廃棄コストメリット」
「設備投資が極小、同業界への新規参入を簡単にする、活性化させる」
など、多くあると言われています。
目次
ハーフインチウェーハを最大限活用するためのエッジ加工技術
多方面から期待されているハーフインチウェーハですが、一方でそのメリットを最大限に活用する上で見えてきた問題点 も確認されています。
解決手段の一つとしてMipox研磨フィルム方式によるエッジ加工技術が適用される事例が増えていますので、
その一部を3点紹介します。
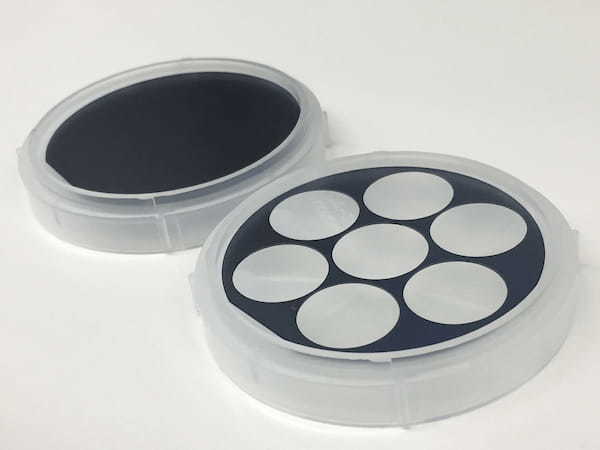
1.あらかじめ薄化されたハーフインチウェーハの破損防止
ハーフインチウェーハは直径(面積)が小さいため、各プロセス中に生じる反りの影響やハンドリング時の破損リスクが低いとされています。通常規格のウェーハを用いる場合に不可欠となる後工程(バックグラインド・BG)を意識する必要性が低く、あらかじめ薄化されたウェーハを前工程に投入する手法(構想)が主流となっています。
そのため、バックグラインド時のエッジトリミング処理は不要となる一方で、薄化されたウェーハへのR面取り・エッジミラー処理を施す必要があります。
そのため機械的な負荷を極力避け、相応の除去効率と表面粗さ低減を両立させなければならない難易度の高いエッジ加工が要求されます。単結晶シリコンは脆性破壊しやすいGaAsのウェーハに対し、特に高い効果を得られます。
また、現状流通しているハーフインチウェーハは、他規格ウェーハからくり抜き(切り出し)して製造されているものも多数ありますが、エッジ部に深く刻まれた切断跡の除去・面取り・ミラー化が必要になりますので、上述の内容同様にエッジ部の管理が重要となります。
2.スピンコート(フォトレジスト塗布工程)におけるエッジクラウン防止
ハーフインチウェーハは直径寸法が小さいことが災いし、スピンプロセスの際に必要となる遠心力を稼げない(稼ぎ難い)というデメリットがあります。特に問題となる事が多いプロセスが「フォトレジスト塗布工程」で、ハーフインチウェーハはエッジ部近辺に凸状の盛り上がった部分(エッジクラウン)が生じやすいことが一般的です。この現象は、ただでさえ小さく限られた同ウェーハの有効面積をさらに狭めてしまう事になるため、用途・状態によっては致命的な問題となります。
解決する手段としては、ウェーハ表面とエッジ部をつなぐ箇所の曲率をリニアに変化させ、なだらかな面取り形状にする事とミラー化が有効(フォトレジストを流れやすくする)とされており、Mipox研磨フィルム式エッジ研磨加工の優位性を大いに発揮できる工程の1つとなっています。
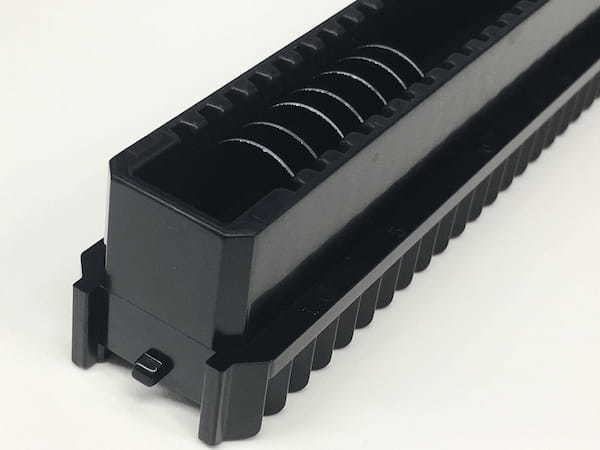
3.エッジクリーニング工程としての活用
ハーフインチウェーハに限らず、通常規格(2~12インチ等)についてもウェーハの外周部(エッジ部)及びその周辺は、エッチング工程で生じた荒れや成膜・メッキなどの各工程で付着した残渣が残りやすい(洗浄し難い)箇所であり、それによって後の工程に様々な問題を引き起こします。
ハーフインチウェーハは、外周部とコア部(ウェーハ中心部)が極端に近いため、前述の影響を直接的に受けやすい状態にあります。
その影響を軽減させるためには、
あらかじめエッジ部をミラー化させ残渣を付着させ難くする方法 と、
付着してしまった残渣をウェーハに負荷を極力かけずに除去するクリーニング処理
この2つが主流であり、いずれの方法もMipox研磨フィルム式エッジ研磨で対応することが可能です。
(2で紹介したフォトレジスト塗布工程で生じた(振り切れなかった)残渣の除去にも有効です)
最後に
ハーフインチウェーハに限らず、各種ウェーハのエッジトリートメント用途に応用可能な「Mipox研磨フィルム式エッジ研磨プロセス」をご活用頂ければ幸いです。