エレクトリックギターの音色は「研磨」が左右すると言っても過言ではありません。職人の方々やリペアーをされている方々は、一つ一つ異なる木材に対して品質安定の面で苦労されているかと思います。デザインについては塗装が大事ですが、見栄えの良い塗装をする為には必ず研磨が必須であり、研磨は音色のような品質にも直結します。このように、エレクトリックギターの品質安定において重要な「研磨」について紹介します。
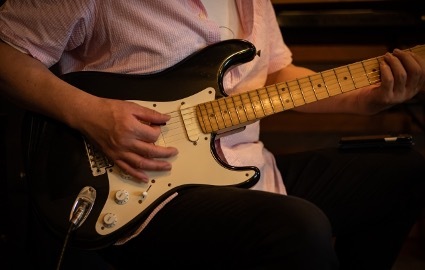
エレクトリックギター作りと音色の関係
エレックトリックギターは、ピックアップを内蔵し、それによって弦の振動を電気信号に変換するギターです。略称はエレキギター及びエレキと言います。
中でも日本国内でのギター作りは信州長野県が盛んであり、ギターの出荷額において長野県は全国で1位です。元々古くから木工産業が盛んな地域でしたが、職人達の研究や試行錯誤から作られました。
このギターの製造工程では、木材の加工から始まり、塗装と研磨の工程にどれだけ力を入れるかで品質が決まってきます。同時にエレクトリックギターの音色も左右します。ギター作りの職人は、研磨屋と言っても過言ではないほど研磨工程は重要です。次にご紹介するエレクトリックギターの製造工程において、いかに正しい研磨工程を行うかによって品質が変わってきます。
ギターの製造工程
ギターの製造工程はメーカーやブランドによって違いはありますが、一般的には以下の通りに分かれます。
1.木材ボディ部門
2.木材ネック部門
3.塗装部門
4.組み込み部門
この4つに分かれ、それぞれの部門の職人が専業として作業を行います。
勿論、一貫して製造している場合もありますが、一人の職人がこれら全ての作業を行うと、自分の製作しているギターに客観性を持つことが難しくなり、品質にバラツキが出る可能性があります。常に品質の安定を目指し、高品質のギターを製造するためには厳しいチェックが必要となります。
製造工程を分業制にすることにより、工程ごとに専任の職人から職人へギターが手渡され、高い技術と豊富な経験を持つ職人が何段階もの検品工程の役割を果たしている形になります。
また、職人が専業で作業に当たることで、自らの分野において特化した専門技術を持ち、その職人たちの手から手へ各工程を経て作られるギターは、技術の積み重ねでしか得られないクオリティーを得ることができます。
次に、各工程について詳しく述べます。
1.木材ボディ部門
① 木材乾燥
② 一定の長さにカットして貼り合わせる
③ NCルーターで外形加工
④ 曲面製作と穴開け
⑤ 木地研磨
ボディ材として使用されている代表的なものは、マホガニー、アルダー(ハンノキ)、アッシュ等が使用されています。この木材を乾燥させ一定の長さにカットして貼り合わせて四角いボディを作ります。(図1) 図1の素材からNCルーターでボディの外形を粗削りし、各工程を経て基本的なボディが出来上がります。
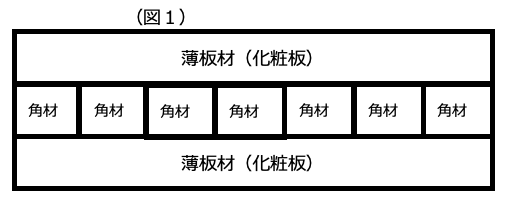
その後、表面を滑らかにするために、ベルトサンダーで研磨を行います。
➡研磨布ベルト PRWJ-BDS #150、#180、#240
この工程で手を抜くと、その後の塗装工程にまで影響が出てしまいます。コストを考えて紙のベルトを使用する場合もありますが、紙特有のカール現象でギターの複雑な曲面にベルトの角で傷を入れないために、敢えて柔軟性に長けている研磨布ベルトで研磨作業を行います。穴加工部分は、サンドキャップを使用します。
➡サンドキャップ SC―315、SC-525
仕上げ研磨やベルトが行き届かない部分は、手研磨用の研磨紙を使用します。
➡ニュータックロールPタイプ P150、P180、P240
➡FRCC-SDS P150、P180、P240
2.木材ネック部門
主に使用される木材はメイプルです。これを粗削り加工して指板の接着を行います。ネックは特に音色に影響が出るので、細部のシェイプには手作業の割合が高く、工程も多くなっています。また、曲面も多いことからハンドツールが主に使用されています。
➡DRAC-RDSM #150、180
➡RRAC-RDSM #240、#320、#400
➡ニュータックロールPタイプ P150、P180、P240
➡サンドキャップ SC-315、SC-525
3.塗装部門
ギターに使用される塗料は次の通りです。
・ラッカー
ラッカー塗装は最も薄い膜厚で、ある程度の厚さになるまで何回も繰り返し塗り重ねます。仕上がりの透明感、上品な艶、自然な目瘦せ具合等が良さであり、一般的にサウンドでも良いと言われています。
・ポリウレタン
ウレタン塗装は膜厚が薄く、柔らかい塗装です。均一に塗装をするには熟練が必要であり、完成した際には高品質なギターとなります。
・ポリエステル
ポリエステル塗装は最も多く使用されています。膜厚は厚く、表面硬度も硬く、木地研磨の精度が塗面にさほど影響が少なく、量産に向いた塗装です。
・オイル
➡オイル塗装は無垢材の使用に限ります。
これらはモデルによって使い分けられています。例外はありますが、アコースティックはラッカー、高級品はウレタン、量産品はポリエステル、無垢材はオイルで塗装されています。
一般的な塗装工程は次の通りです。
① シーラー吹き
② 乾燥
③ 毛羽取り研磨★
④ 目止め
⑤ 乾燥
⑥ 下塗り(サンディングシーラー)
⑦ 乾燥
⑧ 中研ぎ研磨★
⑨ 中塗り
⑩ 乾燥
⑪ 研磨★
⑫ 着色
⑬ 乾燥
⑭ 上塗り
⑮ 乾燥
⑯ 仕上げ研磨★
⑰ バフ掛け
という長い工程を踏みますが、研磨工程は③、⑧、⑪、⑯になります。
③毛羽取り研磨
シーラーを吹いた後、木地の表面が毛羽立ってくるので研磨で除去します。
➡DRCC-BDS P320、P400
⑧中研ぎ研磨
この工程はベルトのカールによって入る傷を嫌うため、カール防止対策を行っています。この対策によりギター製造において大きな貢献をしています。
➡DRCC-B・BDS P320、P400、P600
⑪研磨、⑯仕上げ研磨
この工程でもベルトカール防止対策で大きな貢献をしています。仕上げ段階での傷=やり直しになるため、職人は非常に気を使います。
ラッカー品
WTCC-BDS P800、P1000、P1200
ウレタン品
➡WTCC-B P800、P1200
ポリエステル品
➡DRCC-BDS P800
➡WTCC-B P800、P1000、P1200、P1500
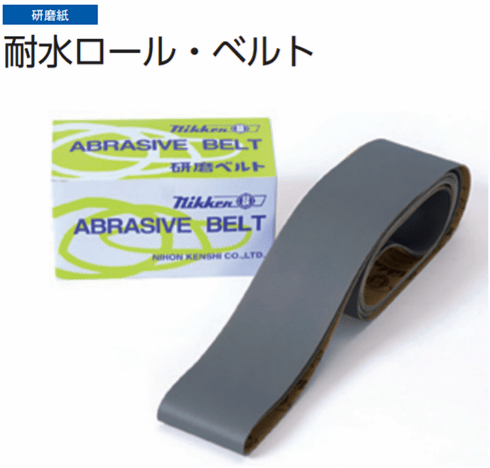
木地からトップコートまでわずか400µm、最終的に仕上げるのに職人はわずか100µmを削ります。少しでも削り過ぎたり、傷を入れてしまうと着色はおろか、サンディングシーラーまで達してしまい、木地研磨から全てやり直すことになります。長年の経験を持つ職人でも気を抜くとオーバーしてしまいます。職人は常に、『塗装の厚みを感じながら研磨』しています。わずか400µmの厚みを感じているということになり、それだけ精度が求められる業界です。
4.組み込み部門
各アッセンブリの組み込みを行います。見えない場所でも非常に丁寧に行われています。全ての組み込みが終わると、最後に拭きあげ作業が行われて、出荷に備えます。以上がギターの製造工程です。
エレクトリックギター作りへの貢献
ギター市場は一時期衰退傾向でしたが、コロナ禍によるおうち時間が増えることにより市場復活の兆しが見えてきました。
ギター製造の職人はギターを一生懸命作る中でギターに対する謙虚な姿勢を貫いています。これこそメイドインジャパンのギターが信用されている理由です。その信用に対して研磨工程で貢献したいと思い、私たちは日々提案を行っています。
参考文献
・ウィキペディア エレクトリック・ギター
・長野県魅力発信ブログ ギター(電気ギターを含む)出荷額 日本一<平成30年工業統計調査(確報)>