鋼材の製造過程で生まれる黒皮(酸化皮膜)。「硬くてなかなか除去できない」とお困りの研磨業者の方も多いのではないでしょうか?そこで今回は、黒皮を効率的に除去できるNPZと呼ばれるMipoxフラップホイールをご紹介します。よく使用されてきたレジンクロスや通常のフラップホイールとの違いや、導入事例などをお話していきます。
目次
黒皮(スケール・酸化被膜)に研磨ついて
ここでは、黒皮とは何か?なぜ研磨する必要があるか?について簡単にお話しします。
黒皮とは
鉄などの金属が、溶けて真っ赤になっている状態を見たことがあると思います。あの溶けた状態が冷えて固まると表面が黒くなり固着します。これは、空気中の酸素(O)と鉄分(Fe)が結合してできた酸化被膜(Fe3O4)です。 この酸化被膜を黒皮と言います。金属の種類によって硬さ、厚み、色、粘りなどが違います。ステンレスやアルミの酸化被膜の色は白色です。白色ですが、ステン、アルミの黒皮と言ったりします。
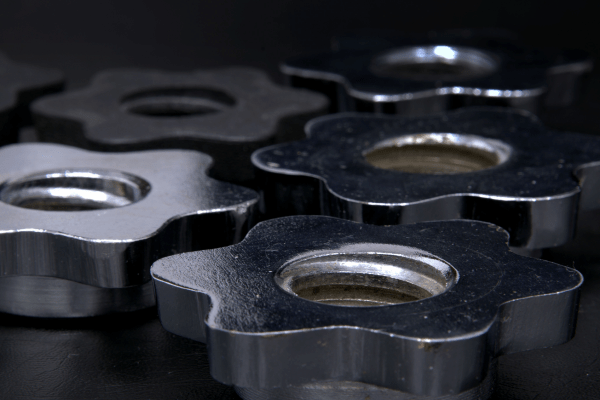
黒皮研磨の必要性
この黒皮ですが、金属を錆などから守る役割もあります。しかし、金属の塗装、メッキ、溶接などの加工を行う場合は、邪魔な存在となります。除去しないと塗装もメッキもうまく乗りません。また、溶接などでもうまく接合できないのです。酸洗いなどでも除去できますが、廃液処理コスト、酸洗いに不適な形状な場合、物理的な研磨での除去を希望される場合も多いのが現状です。 また、黒皮は表面の硬さも硬く、通常のフラップでは滑ってしまい研磨時間が長くかかります。 また、黒皮の除去でよく使われてきたレジンクロスベルトでは、仕上げ面粗さが初期と後期で違いが出ます。一方弊社の強みのある製品の一つにフラップホイールというカテゴリーがあります。この製品ラインナップの中でも、高研磨力、高耐久力に特化したNPZという製品なら鋼材の黒皮除去に適しています。レジンクロスと比べて寿命も長いため取替頻度も少なくて済みます。
NPZとは
ここでは、NPZは、他の研磨材とは何が違うのか、レジンクロスや通常のフラップホイールとはどう違うのかをお話します。
レジンクロス研磨について
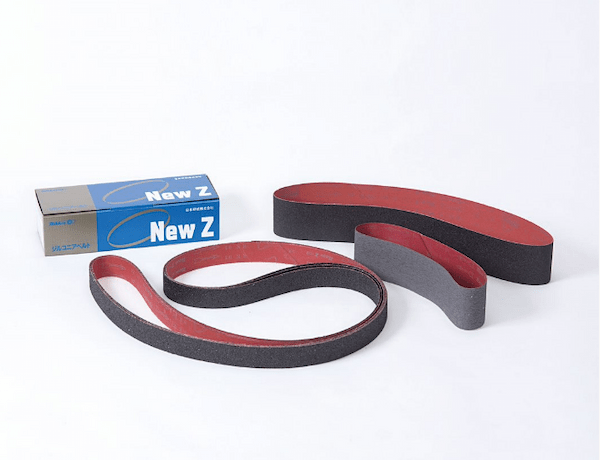
まず、レジンクロスベルトですが、研磨材と被削材が面で接触しますので研磨力は一番高いといえます。しかし研磨材が布基材の表面にしか着いていないため、しばらく研磨しているとダリング(磨滅)と呼ばれる砥材が丸くなってしまう現象が起こります。ダリングすると、ダリング前より研磨力は大幅に落ちます。仕上げ面も初期よりかなり細かくなってしまいます。 結局、取替頻度が高くなってしまうのが実情です。取替頻度が高いと段取り替えに時間が掛かり、生産性が上がらず大量生産には不向きとなってしまいます。
フラップホイール研磨について
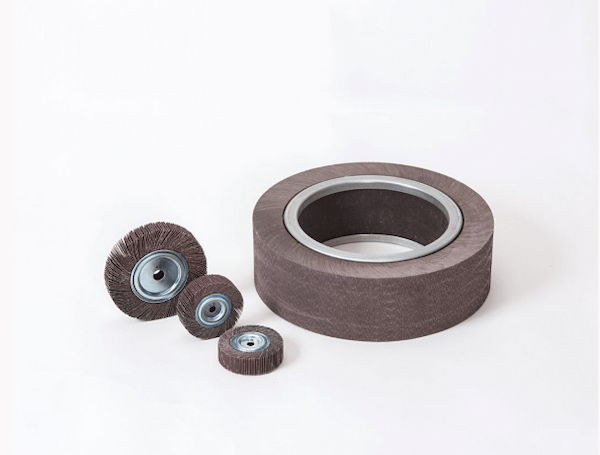
一方、フラップホイールという研磨方法もあります。レジンクロスのベルト材料を短冊状にカットした製品を放射状に金属金具に植え付けてホイール状に組んだ製品です。フラップ研磨であれば、ホイール自体が摩耗します。摩耗しながら、新しい砥材が次々と出てきます。耐久力が高いため取替頻度が少なくて済み、自動機向けといえるでしょう。 またホイールの外周は、ぱたぱたと柔らかい状態となっています。丸棒・パイプ形状などにはある程度のアール面へのなじみが発生します。曲面になじみながら研磨できるのもメリットといえるでしょう。 ただ、研磨力がレジンクロスベルトと比べて低いというデメリットがあります。特に硬い黒皮を短時間で除去したい場合は、時間がかかってしまいます。
NPZの優位性
NPZとは
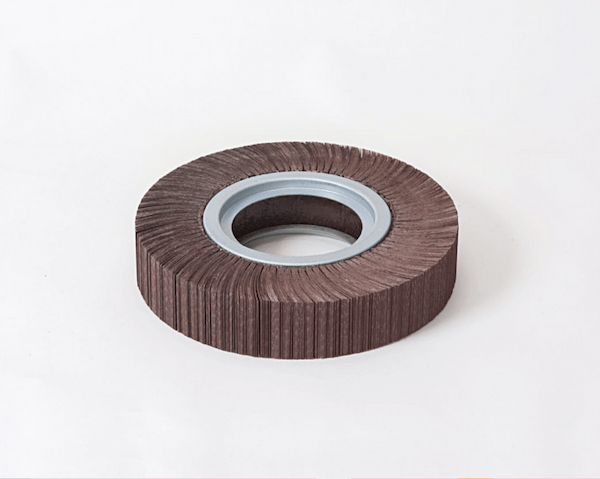
NPZとはどのようなホイールか、どのようなメリットがあるのかについてお話します。 簡単に言えばレジンクロスベルトとフラップホイールのデメリットを対策した製品です。NPZは、フラップホイールの羽(基材)枚数を極限まで高めたホイールです。 通常フラップホイールの羽(基材)打ち込み基材枚数は、金具外径を大きくすることで増やしていました。金具径を大きくすると羽(基材)枚数は増えます。 しかし、羽(基材)の長さは短くなります。基材長さが短くなると耐久力が落ちるという欠点がありあます。羽(基材)の長さを短くすることなく羽(基材)の打ち込み枚数を増やすにはどうすればよいかという課題解決が必要でした。そこでMipoxでは以下の2種類の方法で課題解決を行い、羽(基材)枚数を増やすことに成功しました。 ① NPZ-L(ライトタイプ) 羽(基材)をブロック状にプレスして組み立てる処方
② NPZ-H(ハードタイプ) 羽(基材)の根元を特殊な形状に加工して羽(基材)枚数を増やし、基材打ち込み総量をさらに増やしたタイプ。 ※現在新規での販売を休止中。
NPZのメリットについて
極限まで羽(基材)の打ち込み枚数を増やすとどのようなメリットがあるのでしょうか?まず、打ち込み枚数を増やすとホイール外周での羽基材が動きにくくなります。まさにカチカチの状態です。 フラップというより砥石に近い風合いです。フラップ特有の「なじみ・追随性」はなくなりますが、基材の逃げがなくなります。よってワークからの荷重を逃がすことなく高加圧での研磨が可能になります。高加圧で研磨できることで研磨力が上がります。 また、羽(基材)の総打ち込み枚数も高くなります。羽(基材)の総量が上がることで耐久性も格段に上がります。このようにNPZは、レジンクロスの耐久性、フラップホイールの研磨力などのデメリットを補った商品といえるのです。
NPZ導入事例紹介
ここからは関西地方に製造拠点を置くK社が通常のフラップからNPZを導入するに至るまでの流れについてお話していきたいと思います。K社は、主に鉄・角棒・丸棒の引き抜き加工を行っています。引き抜き加工時に起きるキズと黒皮除去で通常のフラップホイールを使用していました。ただ、生産量の増加に伴い、研磨加工のスピードアップが課題となっていました。そこで販売店様を通じてMipoxへ相談が入り、ご訪問した次第です。
NPZ-L DAでのテスト【NPZ-L DA #60 305x45x170】
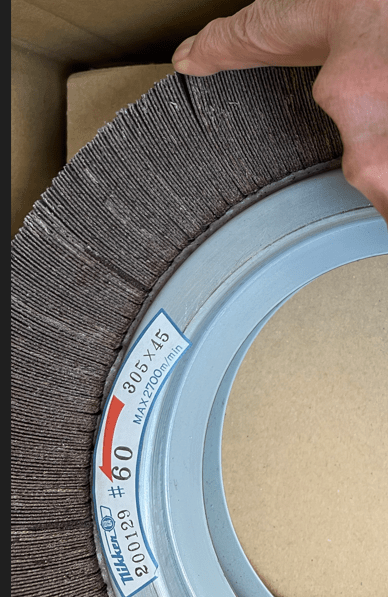
ラインのスピードアップが課題となっていましたが、通常のフラップでは、これ以上ラインスピードが上げられないと判断しました。そこでNPZ―Lの基材DRAX#60(コットン基材)を選択しテストしました。研磨力、研磨スピードアップはクリアしました。しかし、耐久性でNG。耐久力対策が必要となりました。 ※基材摩耗性はコットンの方が合成繊維より摩耗性が高い傾向にあります。
NPZ-L WAS-23でのテスト【NPZ-L WAS-23 #60 305x45x170】
コットン基材を使用したDA基材の耐久力対策として合成繊維を使用したWAS-23基材をテストアイテムとして選定しました。しかし思うような結果を得られませんでした。合成繊維の基材摩耗がうまくいかなかったのです。研磨材のみが脱砂してしまいました。基材が残り研磨力が落ちてしまいました。途中でワークに焼けが入りテスト中止となってしまいました。
NPZ-L DA/WAS-23コンビでテスト【NPZ-L DA/WAS-23 #60 305x45x170】
DA基材・WAS-23基材どちらの基材でも基材特性が出すぎてしまいました。そこで、「単純に混ぜてしまったらいいとこ取りできないか?」と考えました。この考えがピタリと当たりました。上述の通りNPZ-Lでは、数枚ずつの羽(基材)をブロック状に植え込んで組み立てていきます。通常は、基材種類は1種類でブロックを組み立てます。今回、羽(基材)をコンビ【DRAX/WRAX S-23】にすることで研削性のアップと耐久性のアップが実現しました。 ただ、羽(基材)コンビにしますと製品の製造管理が大変になります。コストも高くなります。できれば奥の手として取っておきたい手段です。
最後に
ここまで黒皮除去の必要性や説明、NPZと通常のフラップやレジンクロスとの違いのほか、実際の導入事例で顧客課題が改善できたことなどについてお話してきました。Mipox製品の中には、まだまだ特徴のあるものがたくさんあります。今後も継続的に作業の問題を解決する方法や製品の紹介などをしていきます。Mipoxの製品紹介を今後も楽しみにしてください。