自動車のドアサッシュは、多くの工程を経て製品化されていきます。当社では、ドアサッシュの研磨工程についてドアサッシュメーカー様と共に問題解決してまいりました。
ドアサッシュメーカー様からは、「ドアサッシュの研磨時間を短縮したい」、「前工程での目残り、ペーパーの研磨力が安定させたい」などいろいろなお悩み、ご相談を頂いてきました。
ここではドアサッシュの製造工程について、また溶接工法、ドアサッシ研磨方法、当社での問題解決への取り組み、競合他社を含んだ使用研磨材について述べていきたいと思います。
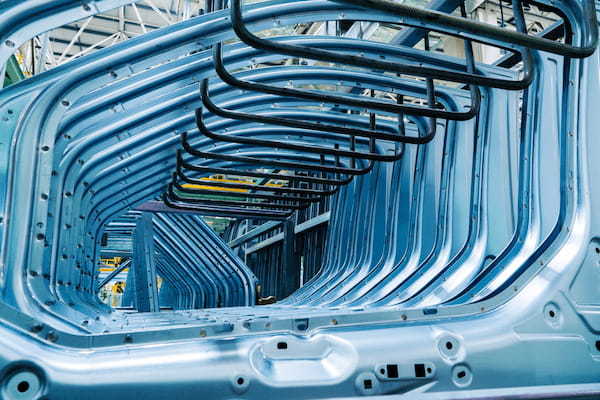
ドアサッシュ工程(フロントドアサッシュ)の流れ
Aアッパーアッシー工程 | Bサイド工程 |
---|---|
1 断面成型工程(ロール機) | ①断面成型工程(ロール機) |
2 曲げ工程(ベンダー) | ②曲げ工程(曲げ治具) |
3 加工工程(プレス機) | ③加工工程(自動プレス機) |
4 切断工程 | ④溶接工程(スポット溶接機) |
5 -1溶接工程(ドアミラー取り付け部品を溶接)(MIG溶接機)⇐AとBを溶接 | ⑤溶接工程(AとBを溶接)(TIG/MIG溶接機)コーナー裏面仕上げ レジンクロス |
6 フォーム合わせ・歪みチェック(ゲージ台) | |
7 仕上げ(裏面溶接ビード除去)(ベルトサンダー)(レジンクロスベルト) | |
8 仕上げ(溶接ビード除去)(ポリッシャー)(ファイバーディスク) | |
9 アクション仕上げ(前工程の目消し)(シングル・ダブルアクションサンダー)(マジックペーパー) | |
10 検品・箱詰め、カーメーカー、車体メーカーへ出荷 ※カーメーカー、車体メーカー塗装工程へ | |
11 ED(電着塗装)→マスキング→塗装工程→ブラックアウト塗装 | |
11‐2ED(電着塗装)→塗装工程→シール入貼り付け→ガーニッシュ取り付け |
溶接工法
溶接工法は研磨工程と密接に関係しています。ここで新工法のプラズマ溶接工法について触れておきたいと思います。プラズマ溶接工法はドアサッシュメーカーとM産業株式会社とM溶接システムと共同開発されました。
これはM溶接システム製のプラズマ溶接機を自動車用ドアサッシュの溶接システムに適応させたもので三社共同開発を行いました。従来の自動車ドアサッシュの溶接工法に比べ製品の品質向上とコスト削減が図れたといえます。
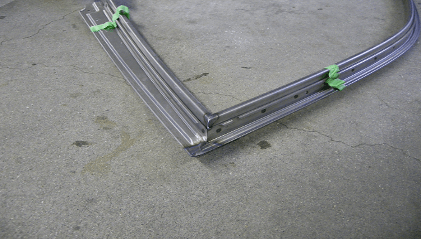
新工法は、プラズマガスによる溶接時の溶接材料を従来のフィラーワイヤーに替えて、パウダー化した溶接材料をシールドガス内の溶接ポイントに直接噴射させます。
従来に比べプラズマガスアークの溶接指向性が安定します。ソフト化し作業効率が上がるほか、溶接部の肉盛りが従来の1/2~1/3に減少し肉盛り高さが低い滑らかな溶接部となるため、見栄えもよくなり、後工程である溶接部の仕上げ作業時間の低減が可能となります。これによりドアサッシュメーカーの主力製品である自動車ドアサッシュの品質向上とコスト低減をはかることを目標に採用しています。
ただ、新工法のメリットをドアサッシュメーカーでは特殊技能者による溶接部の仕上げ作業の低減、廃止と作業環境の改善を目指すとしていますが、溶接部のピンホール問題、研磨工程が思ったほど削減できないなど、まだまだ課題があるとされています。
ドアサッシュ研磨工程
事例1
溶接→コーナー裏側溶接除去仕上げ(MipoxNEWZ―B04 #60)→溶接ビード表面除去(戸田Z100ディスク)→ディスク目消し仕上げ (Mipox DRZD-DDSM #80 SD24)
事例2
溶接→コーナー裏側溶接除去仕上げ(Mipox NEWZ―B04 #60)→溶接ビード表面除去(NCAサンマイトディスク #100)→ディスク目消し①(三共理化学SGED‐HP#120)シングルアクションポリッシャー使用→ディスク目消し②(Mipox DRZD-DDSM #80 SD24)
事例1では溶接ビード除去後のディスク目消しを当社DRZD-DDSM1工程で行っています。事例2では、1度三共理化学のハイピッチ#120シングルアクションサンダーを使用して行い、最終的に当社DRZDをダブルアクションサンダー使用し行っています。違いとしては、事例1は作業性を重視しています。
事例2は仕上げ面重視といえます。事例2は、1工程多くなりますが、ディスクの目消しをしっかりと行い、仕上げ面の安定につなげています。事例1は、#80マジックタック1工程で前工程のディスク目消しを行うため、しっかりと研磨できる研磨紙が必要といえます。そういった意味では当社マジックタックDRZDの研磨安定性、作業性は責任重大と考えます。
マジックタックDRZD―DDSM SD24の優位性について
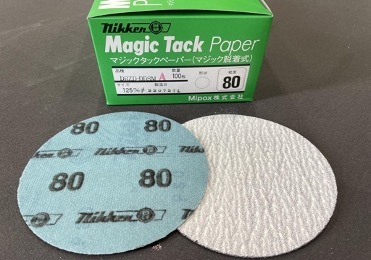
品種 | マジックタックDRZD-DDSM |
砥材 | ジルコニア・アルミナ混合 |
粒度 | #60・#80#100#120(粗い←#60>#80>#100>#120→細かい) |
サイズ | 100φ・125φ(その他サイズ製作可能) |
基材 | Dw研磨紙 (薄い←Aw<Cw<Dw<Ew→厚い) |
特徴 | 鋭い切れ味だが、マイルドな仕上がりを両立。 ハンドツールからの振動も少なく、一日の作業で疲れにくい |
ドアサッシュメーカーでのファイバーディスク目消しはDRZD-DDSM SD-24 が多く採用されています。
これは、ユーザー要求を製品に反映させることにより顧客満足を得ることができた結果と考えます。
結果的に各ユーザー様で新規車種が立ち上がるたびにDRZD-DDSM SD-24が採用されることとなり、ドアサッシ業界でのシェア拡大につながりました。具体的なユーザー要求は以下の通りです。
1 コーナー部分アール加工研磨時に起きる研磨紙の層間剝離防止
2 耐久力・研磨力アップ(作業時間の短縮)
3 製品のバラつき防止
4 仕上げ面の安定
5 作業者のユーティリティ(作業性、研磨しやすさ)
1はSD24(層間剝離防止)を施すことで層間剝離を防ぎ、結果的に研磨紙自体の腰を強くすることができました。結果、耐久力、研磨力アップも実現。
2は、高品質ジルコニア砥材を使用し研磨力、耐久力を大幅にアップ。
また、3は、SB-処方(熱処理)を行うことで熟成不足(樹脂硬化不足)の防止が実現。また、梅雨時期に指摘されていた湿気による研磨力の低下を防ぎ、製品の安定化に成功しました。
④は他社がしばしばカーメーカーの塗装ラインでクレームを起こすのに対して弊社のDRZDは非常に仕上げ面が安定しており、仕上げ面も細かい点が優位に働いています。これらの処方を行うことで仕上げ面の安定を可能にしてドアサッシュユーザーでのドア仕上げクレーム(工程表⑪車体メーカーの塗装で起こる)を低減することで弊社シェアアップが実現しています。
他社メーカー製品
マジック研磨紙製品
R社 リコマジックHM-2
DRZDと外観、仕様スペックともに酷似していますが同じ粒度#80でも仕上げ面が少し粗く同じDw研磨紙でも少し厚いものを使用しています。研磨力・耐久力ともDRZDと同等の結果を得ています。
また、現場作業者からはDSのホコリが少ないという特徴が評価を得ています。ただ、厚めのDw研磨紙を採用していますので研磨作業時に強く抑える必要があり、1日中の作業ではDRZDとの比較で使いづらさを訴える作業者もいます。
S社ハイピッチペーパーSGED‐HP
特徴としては、DRZDが高品質ジルコニア砥粒を使用しているのに対してSGEではセラミックス砥材と安価なアルミナ砥材を混合使用しています。また、DRZDがDw研磨紙を採用しているのに対して、Dwより厚みのあるEw研磨紙を使用している点も特徴としてあげられます。
高価なセラミック砥材を使用しているため、当社のDRZDと同等以上の研磨力ですが、作業者によっては使いづらさを訴える場合があります。これは、紙の厚いEw研磨紙を採用しているため、ワークに押し当てると強く反発してペーパーの制御に力を要する点がデメリットとして挙げられています。ただ近年では力の強い外国人作業者の増加により採用されるケースも多くなってきています。
ファイバーディスク製品
T社 ファイバーディスク | N社 SFF ファイバーディスク | |
---|---|---|
サイズ | 180x22.2 | 180x22.2 |
形状 | 8角 | 8角 |
砥材 | ジルコニア | キュービトロン |
特徴 | 溶接ビードの除去に使用、 仕上げ面の安定と研磨力には定評あり | 研削力アップも仕上げ面は戸田研磨製品比較で少し粗い、 作業性に定評がある反面、後工程のマジックタックの負担増との見方もあり |
最後に
以上ドアサッシュ製造工程、研磨状況を述べてきました。競合他社が高研磨力と研磨時間短縮に重点を置き、製品開発行ったのに対して、当社では仕上げ面の安定と作業者の使用感を大事にしつつ研磨時間の短縮、製品の安定化に重点を置き、製品開発してきました。
今後は、これまで行ってきた開発項目を大切にしながら、更に作業性作業時間を短縮できるように製品開発を行っていきたいと思います。今後のMipoxマジックタック製品の新製品にご期待ください。また、お悩みご相談などあればいつでもお気軽にお問合せ頂ければと存じます。