大型二輪マフラーの代表的素材の一つであるSUS(ステンレス)マフラー鏡面仕上げ研磨の作業効率をアップする方法を当社のサービス事例を通じてご紹介します。
マフラーって何?
まず本題であるSUSマフラー鏡面仕上げ研磨のお話の前に、マフラーについてあまり馴染みがない方のために、マフラーがどのような役割を担っているか、どのような素材でできているかなどについて少し触れておきたいと思います。
マフラーの役割
エンジンから排出される高温・高圧の排気ガスの騒音を軽減する役割を持っています。内部のサイレンサーを通じて排気ガスの勢いを弱めて排気音を小さくします。
マフラーに使われる主な素材
・スチールマフラー (マフラー素材として昔から多用。クロムメッキされることが多い) メリット:価格が安い、クラシックなバイクに合う、加工が容易なためデザイン性に優れる、低音サウンドを奏でる デメリット:重い、錆びやすい、
・SUSマフラー (品質・コスト面でバランスが良くマフラー素材として最もポピュラー) メリット:鉄に比べ安く錆びにくい、鉄より強度が出せるため薄く軽量に仕上げられる、光沢が綺麗 デメリット:チタンに比べて重い、熱で色が変化する
・チタンマフラー (レース用や高性能バイクで使用される) メリット:圧倒的な軽さと強度、錆びない、熱処理で綺麗な焼き色がつく デメリット:加工困難でコスト高
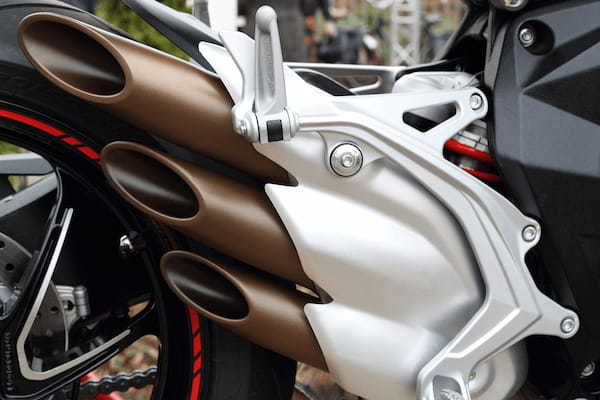
SUSマフラー研磨の特徴と課題
ここからは、二輪マフラーの素材の中で最もポピュラーで親しみのあるSUSマフラー研磨の特徴や課題についてご紹介します。
マフラーの研磨工程
マフラーの研磨は主に溶接部とマフラー表面に大きく分けられます。粗研磨から鏡面研磨仕上げ研磨までの一例を次にご紹介します。
【溶接部研磨工程】 | 研磨ベルト#60 |
鉄バフ#100→#180→#220 | サイザルバフ | 綿バフ |
---|
【表面研磨工程】 | 鉄バフ#200→#220→#250→#280 | サイザルバフ | 綿バフ |
---|
SUSマフラー研磨において、ペーパー(研磨布紙)を使用する工程は溶接部のビード研磨のみです。 レジンクロスベルト#60の後工程を丁寧に鉄バフで整え、サイザル、綿バフへつないでいきます。
マフラー表面研磨に至っては、すべての工程をバフ系で仕上げるという特徴があります。 その理由は、研磨の目的に由来します。溶接ビード研磨以外は、あくまでマフラー表面を形状通りに仕上げるという大前提があります。 しかしマフラーの形状は円筒形を主体とした複雑なR形状が多く、表面全体を鏡面に仕上げるまでには多くの工程とともに作業者の熟練度が要求されます。 そこで重宝されたのが鉄バフです。 鉄バフというのは同心円状にミシン掛けした綿バフにニカワを接着剤として用い、エメリー砥粒を外周部に塗布したバフ研磨材です。メリットとしてはベルト研磨に比べ目が細かくあたりが柔らかいこと、コストパフォーマンスが高いことです。一方デメリットとしては、ニカワ、エメリー砥粒などを塗布する作業に労力がかかることです。
課題 このような特徴をもつSUSマフラー研磨工程ですが、常に頭を悩まされるのが研磨工程数の多さです。 いかに仕上げレベルを維持しながら工程数を減らし、全体の作業効率をアップさせられるかが課題となります。
効率を考えたSUSマフラー研磨の工程
上述したように、SUSマフラー研磨工程には工程数が多いという課題があります。ここでは、こうした課題に対して当社がどのように対応したかをご紹介します。
課題に対する提案 溶接ビード研磨工程において、鉄バフを研磨ベルトに置き換えることで、研磨時間の短縮を考えました。鉄バフに対し、研磨ベルトの研削力の高さを生かす作戦でした。
しかし、マフラーの形状に対して研磨ベルトの馴染不良からくる形状くずれのリスクおよび研磨ベルトのミミ(両サイドのエッジ部のこと)が原因で、ワークにキズが入るリスクが高いこと、そして鉄バフの仕上げ面粗度が研磨ベルトよりも細かいことが分かりました。つまり後工程のサイザルバフ、綿バフ工程を考えると、鉄バフの方が安心して使用できるなどの理由から、研磨ベルトへの置き換えを断念せざるを得ませんでした。
次に考えたのが、研磨工程の最初にくる溶接部のビード研磨用の研磨ベルト#60を#80に変更してスタートにできないか?ということです。現在の工程では研磨ベルト#60を使用することで高い研削力が発揮されます。しかしその分#60という深い目(研磨キズ)を残し、その目を消すために、後工程の鉄バフで#100からスタートし、#180→#220という、3工程を踏まざるを得ません。仮に研磨ベルト#80からのスタートが可能であれば、その後工程は鉄バフ#180→#240の2工程に短縮が可能であると、当社がこれまで積み重ねてきた経験をもとに仮説を立てました。
それとともに後工程のサイザルバフも従来の鉄バフ#220の目を消すところからのスタートに対し、この工程であれば、鉄バフ#240の目を消すところからのスタートとなることから、自ずとこのサイザルバフ工程も作業時間短縮が可能となります。
この考えに至るきっかけとなったのが当時、当社の新製品【セラミックベルト】が発売されたことでした。
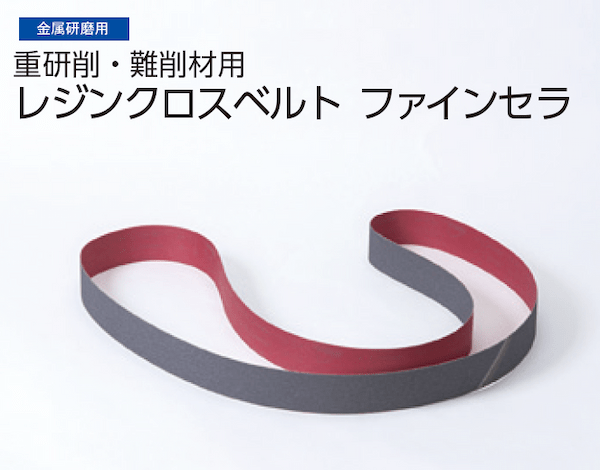
砥材に採用されたセラミックは靭性が高くシャープな粒形を持続することが可能で、セラミック特有の破砕構造により高い研削力を維持し、また衝撃や熱にも強く優れた切れ味と耐久性効果が期待できる製品でした。この研磨ベルト#80を溶接ビード研磨に抜擢し、鉄バフおよびサイザルバフの作業時間短縮の提案行いました。ユーザーにてテストを行い、ほぼ考えた通りの効果が確認されました。その新しい工程を次にご紹介します。
作業効率をアップした研磨工程
【溶接部新研磨工程】 | セラミック研磨ベルト#80 | 鉄バフ#180→#240 | サイザルバフ | 綿バフ |
---|
まとめ
今回の提案により、全研磨工程時間のおおよそ10~15%程度の時間短縮が実現できたとユーザーからも評価をいただきました。 また新製品のセラミックベルトの効果として取り扱いマフラーが複数ある中、溶接ビードの状況次第でセラミックベルト#80からさらに1番手細かい粒度の#100スタートが可能な場合もあることが判明しました。 この発見もさらなる作業効率アップにつながりました。
このような経験を生かしてさらに応用を利かせ、今後もお客様に喜んでいただける提案営業を目指し努力してまいります。本稿が少しでも読者の皆様のお役に立てれば幸いです。そして、もしお困りごとがあれば、当社にぜひご相談ください。