Mipoxの受託加工のラインナップである「接合加工」について以前ご紹介しましたが、接合加工を実施するにあたり、同一素材・異種素材ともに、接合面の状態が非常に重要な要素となります。今回はこの接合面の状態の処理についてご紹介します。
関連記事:Mipoxが展開する半導体ウェーハ『接合加工』と前後の『加工処理』について
目次
接合加工サービス前処理について
弊社は国内でも数少ない接合加工を受託で請け負うビジネスを展開しています。常温接合加工サービスでは、接合加工だけでなく、表面の状態を適正な状態に加工する研磨加工サービスや、接合面の清浄度を向上させてコンタミネーションの混入を防ぐ洗浄加工サービスも併せて実施しています。
弊社で請け負う多くの接合素材は、半導体用途で使用されることが多く、ボイドの発生やコンタミネーション混入などによる接合の不良が大きな問題となる場合があります。そのため、Mipoxでは下記に記載する前加工を実施し、接合状態の向上に努めています。
前処理加工の具体的な内容
表面粗さの改善
一般的な接合方式では、それぞれの素材の接合面と接合面の間に粘着剤や粘着シートを介在させます。これに対し、Mipoxでは素材と素材を直接接合するため、各素材の表面粗さが細かい状態が適しています。素材表面の粗さが粗いままだと、素材同士の接合面に空隙が生じ、接合不良が生じる可能性があります。このため、弊社が得意とする仕上げ研磨加工を実施しています。単結晶素材、多結晶素材、金属、ガラスなど各素材に適した独自配合の研磨剤を用いて、適切な表面状態を作り上げます。
表面清浄度の向上
上記工程でそれぞれの接合面の粗さが適正な状態になったとしても、各表面に異物が付着することで接合後の異物混入が発生し、特定箇所の製品不具合が発生するほか、接合自体ができなくなってしまう恐れがあります。
そこでMipoxでは、接合前の各素材に対して適正な洗浄処理を行います。一般的に用いられるスクラブ洗浄や薬液を使用した洗浄等、各素材に適した洗浄処理を行うことで、接合加工の精度や品質を向上します。
接合加工後の具体的な品質確認
赤外線カメラ画像による接合状態の確認
Mipoxでは、接合加工後の品質確認の一環として、赤外線カメラによる接合状態の確認を行っています。接合素材が透明体の場合は、目視での接合状態確認やボイド有無の確認など、目視や顕微鏡を用いた検査・確認が可能ですが、非透明体の接合後の検査の場合は、目視や顕微鏡では接合状態の確認を容易に行うことができないため、赤外線カメラで接合状態の確認を行います。
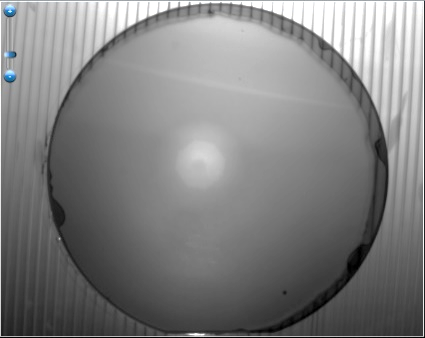
ブレード挿入による接合強度確認
接合加工後は、目視や顕微鏡、赤外線カメラによる接合の状態確認を実施しますが、実際の接合強度についてもブレード挿入による接合強度の試験を実施します。
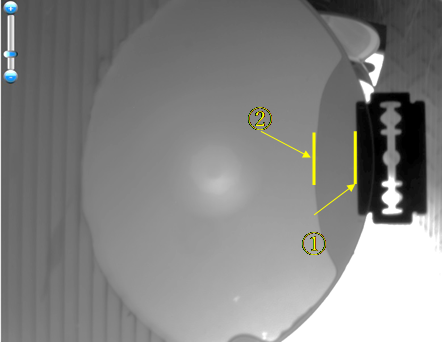
接合加工後のウェーハ外周部の処理加工
Mipoxでは、接合加工後のウェーハに対し、エッジトリートメント処理を行うことが可能です。接合加工後の薄化加工の際に、ウェーハが破損するのを防ぐため、エッジトリミング加工や粗さ調整加工を実施することが可能です。
エッジトリミング加工
接合後の基板の端面部分に研磨処理を行い、薄化工程の際に効率よく薄化できる形状へ加工することが可能です。
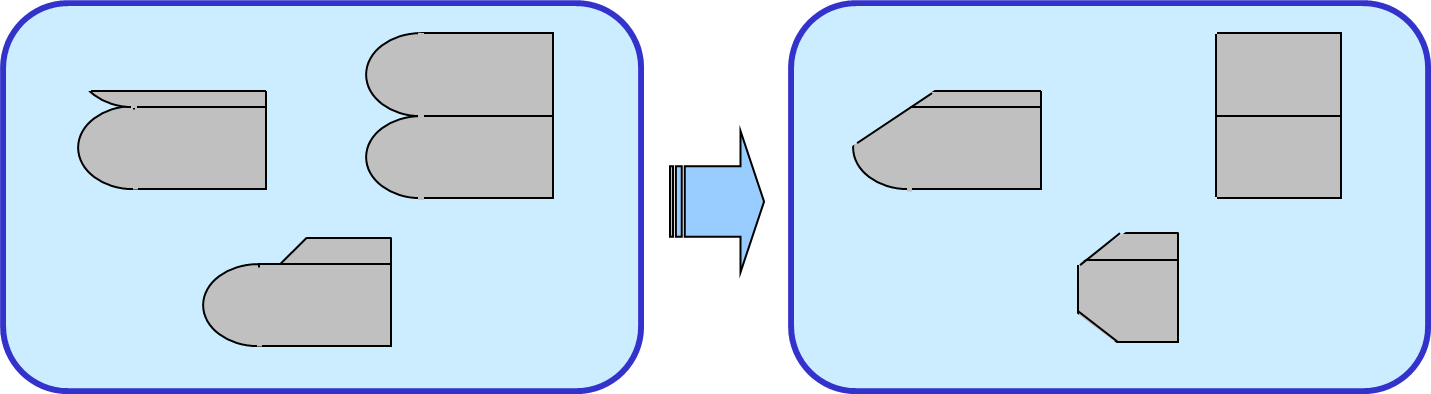
粗さ調整加工
接合後の基板の端面部分の粗さを調整し、チッピングやクラックの防止を行います。
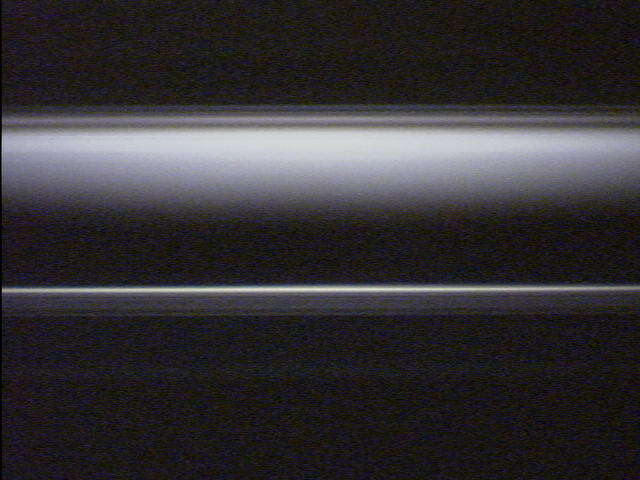
まとめ
Mipoxでは、接合加工の前に各基板の表面状態を適切な状態に施す加工や洗浄を実施します。また接合加工後は、接合状態の確認を実施いたします。接合加工後のウェハ端面形状の調整や、粗さ調整が可能です。