電子製品の基礎的な部品であるプリント基板もまた、日々進化しております。それによってプリント基板の製造工程は複雑化しており、特に多層化の面で研磨工程の必要性が高くなってきています。今回はMipoxが考えるプリント基板研磨の必要性・方向性・またこの為の製品についてご紹介します。
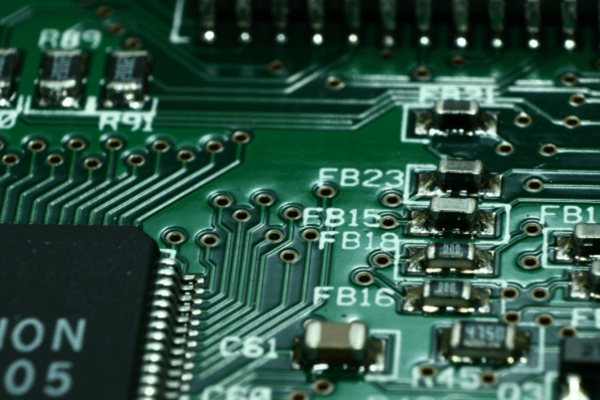
プリント基板とは
プリント基板、あるいはプリント配線板(以下PCB=Printed Circuit Board)の一般的なイメージは、 「電子機器の中に入っているさまざまな部品が付いた緑色や茶色の板」かと思います。弊社では、このPCBを製造する時に必要となる研磨材についても製造・販売を行っています。PCBの概要とPCBに使用される研磨材の一部についてご紹介いたします。
PCBは元々、抵抗器やコンデンサといった電子部品とこれらを接続するソケット・スイッチ等を細い導線で1つ1つはんだ付けして配線していたものを、板上に揃えて一様にはんだ付けしている部品です。特徴は配線自体のミスを無くすことができる・導線の被覆を剥いたり焼いて取り出したりの手間をなくすことができるなどの特徴から、現在の電子機器には必ず含まれている部品の1つです。
プリント基板は大きく分けて、【リジッド基板】と【フレキシブル基板】の2種類に分類することができます。
まずはじめにこれらについてご説明いたします。
リジッド基板
リジッド基板とはごく一般的な緑色や茶色をした、一見プラスチックのような板でできた基板です。安価品から高級基板まで、グレードも様々です。ごく安価で旧来からある紙と耐熱性の樹脂を使用した「紙フェノール基板」と、現在もっとも一般的なガラスメッシュとエポキシ樹脂の積層材でできた「ガラスエポキシ基板」があります。
LEDや発熱量の大きな部品を使用するための「アルミベース基板」「セラミック基板」など概ね材料名+基板、という呼びかたが一般的です。リジッド基板は強度があるため部品を基板上に配置して、はんだ付け(ソルダリング)するために使用されます。
フレキシブル基板
フレキシブル基板は主にヒンジ(ノートパソコンや昔の折りたたみ携帯電話にあった蝶番のような機構)などで用いられる柔らかいリボンのような部材です。元は電線を束ねたハーネスを薄肉化したものです。ポリイミドのベース材料と銅箔でできており、主には先のようにヒンジなどの可動部品内に仕込まれる、リジッド基板同士を接続するハーネス替わりに使用されることが多くなっています。
これら基板は今後も部品の集積化などで小型化や複雑化は進みますが当面の間、電子機器には搭載されると考えております。5Gなどに代表される無線技術は日進月歩で発達していますが、これらの技術を使用するためにも基板という基幹部品を除外することは難しいと考えています。
弊社のPCB向け研磨材料はこれらの内リジッド基板を主なターゲットと見据えて開発を行っております。なぜなら、今後の国内、海外問わず社会の技術発展のために重要な技術の一旦であると考えているからです。
基板トレンドの2極化
現在、基板トレンドでは以下に示す2つの方向性があります。
- 大電流・高電圧基板
- 高周波化・複雑化基板
大電流・高電圧基板
まず、1. 大電流・高電圧基板 についてですが、これは「電気自動車(EV)」「パワーエレクトロニクス」などに主に使用される基板です。経産省では次世代自動車・普及促進に向けた取り組みやEV・プラグインハイブリッド(PHV)の普及促進を行っております。
弊社の研磨布紙事業では旧来から自動車産業と密接につながりを持って機構・外装・修理などの取り組みを行ってまいりました。パワー半導体や大型の蓄電池を使用し、高電圧・大電流を取り扱う大電流・高電圧基板は旧来からあるPCBと異なり、非常に厚みのある銅箔厚みがあります。
具体的にどれくらい差があるかですが、一般的な電子基板では銅箔が0.01mm~0.04mm程度の導体厚みです。対して大電流・高電圧基板では0.2mmから数mmの厚みの銅箔厚みがあります。電流量を増やすために導体抵抗を小さくする必要があるためです。また、これらの銅箔段差に加えて放熱対策のためにさまざまな工夫を各社様が行っております。例えば放熱の為に空冷穴を各部に設ける、伝熱性の高い基板材料を使用する、パワー半導体の直下に放冷のためのヒートシンクを基板自体に設ける、など様々です。
対する弊社の取り組みですが、1つに本件の製造上の難点として、銅箔段差があります。基板上には「プリント配線板」という配線と基板上にエッチングなどで作られた銅配線があります。導体厚みが薄い際には問題にならなかった銅箔段差ですが、大電流・高電圧基板では例えると「洗濯板のような段差」の表面を舐めるように研磨する必要があります。基板が洗濯板、研磨材が洗濯物、のような状態になるため、逆に研磨材の方がぼろぼろになってしまうこともあります。この時、研磨材がぼろぼろになってしまうと「ほつれ」が研磨材から脱落してしまいます。「ほつれ」が研磨工程の後にある洗浄工程で除去できれば問題はありませんが、研磨材を内包しているため、研磨材の突起が引っかかるなど非常に除去が難しくなっています。
これに対し、弊社では①「ほつれ」が十分に小さく、洗浄工程で簡単に落とすことができるような研磨材の開発、②「ほつれ」がそもそも発生しない研磨材の開発、を行っています。前者は不織布研磨材「LUB」、後者はペレット研磨材「FSP」「TLF」があたります。
高周波化・複雑化基板
高周波化・高密度基板についてですが、前述の大電流・高電圧基板と変わって今度は信号系を取り扱う基板になります。
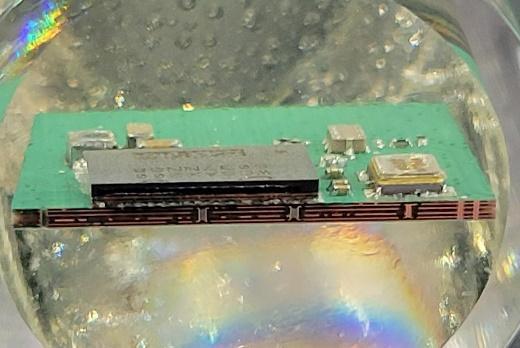
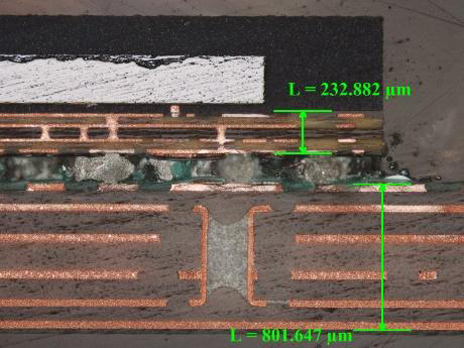
現在の情報化社会でスマートフォンやモバイルPCはなくてはならない存在になっています。これらのモバイルガジェットに必要な要件ですが「小型」「軽量」「長時間駆動」が挙げられると考えています。mg単位のダイエットがガジェット内の部品に課せられたわけです。もちろん基板に対してもダイエット要求は平等に課せられました。この要求をどうクリアしたかですが主に以下3つのような取り組みを行いました。
- 基板パターン(配線)を細かくする
- 板厚を薄くする
- 一部の部品を基板内に内蔵する
現行のスマートフォン技術で避けられない技術として「mSAP」などが 1.の基板パターン(配線)を細かくする にあたります。配線パターンを小さくすれば軽量化は容易です。ですが、配線パターンを小さくすると「高周波化」という問題が強くなります。ここに、情報技術が革新してデータ量が近年一気に増加しました。取り扱うデータ量も増えた場合どう処理するかというと「一回に処理できるデータ量を増やす」あるいは「処理するデータの個数を増やす」となります。
高周波化は「処理するデータの個数を増やす」にあたります。処理するデータの個数が増えた状態で基板パターンが細かくなると、信号線が近接した影響で信号の迷走が物理現象として発生してしまいます。クロストークやリークといった現象です。
物理現象に対しては物理現象で対応することが1番です。基板パターンを設計通りに作るということが弊社研磨材にも課せられています。研磨の精度を向上させる。ということです。これは①表面粗さを安定させる、②基板の厚みムラを抑える、などが挙げられます。
まず①表面粗さの安定についてですが、旧来のPCB研磨工程では基板サイズの広幅研磨布ベルトなどを使用しておりました。弊社がご提案差し上げる工程ではロール状のペレット研磨材をご提案いたしております。研磨布ベルトは合成繊維上にメイクコート・研磨材塗布・サイズコートといった工程を経て研磨材としています。研磨材は一般的に1層で塗布されています。[Fig3]
![[Fig3]](https://cdn.mipox.zuudev.com/media-cdn/186/139/MuwMfnlYJTbMrCMkHPrVKvAuEAGdXpxJ/976cb021-8570-4bb6-bc94-24dbc09bdde9.jpg)
研磨布ベルトは一般的に単層のため、研磨砥粒の状態が刻々と変わっていきます。初期には鋭く尖った砥粒の切っ先で強く傷が入り、交換前では砥粒が丸くなることで研磨性が十分に発揮されません。
弊社PCB向け不織布製品、ペレット製品は共に初期から交換まで同等の性能を安定して発揮します。特にペレット製品では他社砥石ロール製品と異なり、リジッドロールに近い性質を持っています。
この性質は表面粗さの安定以外に②基板の厚みムラを抑えることにも寄与いたします。基板は1枚をそのまま使用することは少なく、1枚の大きな(50cm×60cm程度が一般的です)基板を小さくカットして使用します。
一般的なPCB研磨ロールは外径15cm×幅61cmです。このロールは研磨中に微小ですが変形し、研磨対象の基板に厚みムラが発生します。基板毎の最終製品に発生する個体差の原因の1つではないかと考えています。
リジッドな性質の強い弊社「FSP」研磨材は比較的高級製品や、部品内に使用される極薄基板(パッケージ基板)等に採用いただく傾向が高くなっております。
今後一層進むと考えられる情報向け基板・パッケージ基板の高機能化、高精度化に対し一層の製品開発を進めてまいります。