プリント基板における研磨材の効果についてお伝えするシリーズ。
初回ではプリント基板の方向性と必要な研磨について大まかな概要をご説明しました。2回目である本記事では高周波基板の研磨についてご説明します。
(前回の記事:プリント基板市場における研磨材の効果と方向性 )
高周波基板とは
現在のプリント基板(以降PCB)は、3種類に分けることができます。
まず「特に気を使わなくていい普通の基板」、今回で説明する「高密度な信号向け基板」、そして 「電流量を流す必要があるパワー回路基板」です。
5G,6Gとよく巷で聞きますが、これは今回焦点を当ててお伝えする高密度な信号向け基板、
すなわち 高周波基板 が非常に重要になっています。
そもそもこの5G・6Gとは何か? ですが、この答えは要するに第何世代の通信技術か? です。黎明期の肩掛け電話が1G、「iモード」世代が2G、「FOMA」「CDMA-ONE」が3G、LTEが4Gになります。
スマートフォンをはじめとするモバイル機器は形を大きくするには限度があります。それは例えば重さの問題であったり、手の大きさであったり、皆様のカバンの都合などもあります。スマートフォンの性能が良くなったからと言って自分たちの手が大きくなることはありませんし、若い女の子が山登りに行くようなボディバッグを持ってショッピングには行きませんよね。
SoCのような集積化や技術革新で電子部品自体の基幹部分の性能は向上しました。それに合わせて、電気的なベースである基板も性能向上が求められています。
高周波基板で求められる性能
高周波基板で求められる性能とは何でしょうか?
それはエラーを起こさないことだと考えます。
最近では電子部品の性能向上で通信速度が非常に上がりました。例えば3Gと5Gを比較すると3Gが14Mbps、5Gでは20Gbpsです。単純計算だと20年間で1400倍に高速化しています。基板の中の信号も同様に高速で処理を行う必要があります。基板の中の信号の流れは速くなり、また、集積化で基板のサイズや基板パターンの高密度化が進みます。
基板パターンの中で導体(銅)をランド(L)、導体間のスキマのことをスペース(S)と言いますが、L/Sが非常に細かくなっているのが現状です。旧来法のビルドアップ法でも100μm/100μm、mSAP法では20μm/20μm以上に細かくなる様子があります。
パターンが細かくなるとどうしてもパターン形状のくずれが発生します。ビルドアップ法ではパターンをエッチングで化学的に溶解して作るためパターン形状のくずれが顕著です。
パターン形状がくずれると予期しない信号の受け渡しエラーが発生します。この際、理論値と実測値が異なるのは、理論値設計どおりの回路パターンになっていないことが原因として挙げられます。このため、通信ではある程度の冗長性をもってエラーの訂正を都度行います。
これらの基板の製造時、研磨に求められるのは大きく3点が挙げられます。
- パターンを崩さない
- 研磨カスを残さない
- 面精度を出す
これらについて順に説明します。
1.パターンを崩さない
パターンが‘崩れる’とは? と疑問に思われる方もいらっしゃるかもしれません。
PCBの研磨加工の際、一般的には1500~2000rpmの回転する研磨ホイール(ロール)に基板を押し当ててPCBを研磨していきます。実際研磨している時間は工数にもよりますが1枚あたり5~10分程度、単一の方向に向かって研磨ホイールを当てていきます。
パターンは10~30μm程度の厚みをもった銅箔がわずか100~200μmほどの線幅しかないものもあります。このため、パターンを保護しながら研磨する必要があります。研磨ホイールの形状が一様でない場合にはパターンを破損してしまうほか、基材自体も厚くて2ミリ程度のGFRP 板であり、研磨の衝撃や負荷の影響で伸び・反りが発生します。
研磨加工ができずに食いついてしまうと負荷が基板を歪ませるように力がかかってしまいます。このため低負荷で銅の表面や基板を研磨する快削性が必要になります。
2.研磨カスを残さない
エラーの原因になるのはパターンの形状だけではありません。研磨中の研磨カスが残留すると、これも基板の樹脂は導電性や帯電率の差があるため安定な動作を阻害します。特に銅箔研磨においてはアルミナ系の不導体砥粒よりもSiC系の砥粒は砥粒形状がシャープであることから研磨において効果的です。SiCはもちろん電気的に半導体の特性を示し、また、快削性を向上するために金属元素を含みます。
弊社ペレットタイプや砥石タイプの研磨ホイールでは通常の研磨グレードのSiCより高純度のSiC砥粒を使用していますが同様に半導体の特性は有しています。
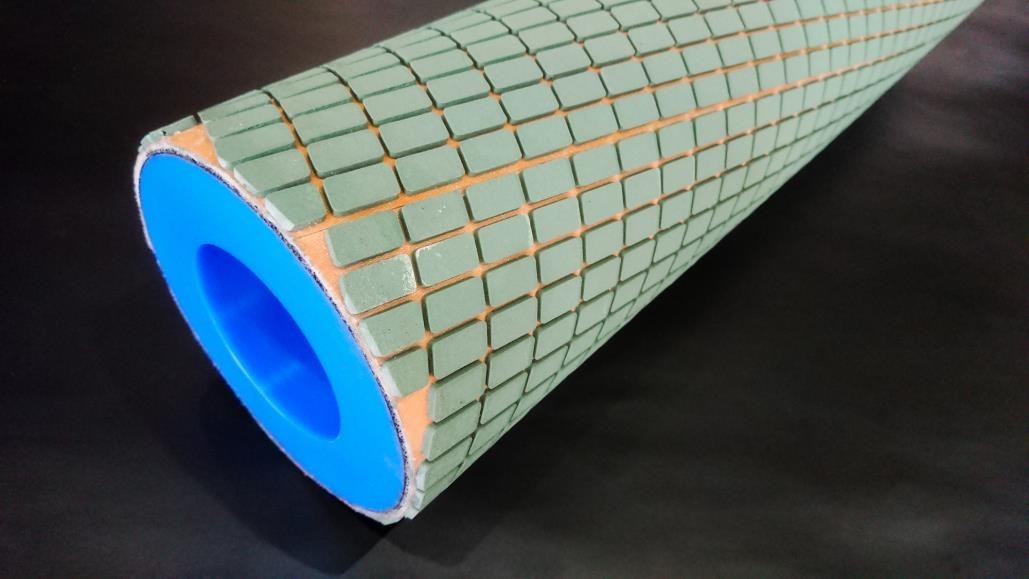
ほとんどの研磨カスについては研磨後の洗浄工程で洗い流されますが、特に不織布ホイールではパターン間への研磨材づまりが問題となります。不織布ホイールに使用される不織布研磨材は、不織布基材中の合成繊維、不織布バインダー樹脂、研磨材、研磨材バインダーの4種類の成分で構成されています。研磨材のつぶが突き刺さる、のではなくこれら複合体と研磨中の金属カスなどがからみあったものがパターン間に付着してしまいます。
パターンが理想形状であれば比較的素直に除去されますが、狭細なパターンでは前述の通り、パターン形状がつぶれていることがあります。この場合、パターンの変形した部分に挟み込んでしまい、簡単に除去できない場合が発生します。
PCB向け研磨ホイールでは多くの場合2種類の回避方法をとっています。
1つは「バフカス対策不織布ホイール」という製品を使用します。通常の研磨ホイールは研磨性能を重視するため、研磨材バインダーに硬い「フェノール樹脂」を使用し、合成繊維もしっかりとした太いPETやナイロンの繊維を使用します。「バフカス対策不織布ホイール」では、競合含め通常の研磨製品と異なりかなり細い繊維を使用しています。細い繊維と太い繊維を比べると当然、細い繊維の方が弱い力で切れます。繊維を細く、また、樹脂も通常品と比較すると柔らかな材料を使用することで大きな異物を作らず、細かく研磨ホイールのカスが発生していきます。このため、可能な限り細い繊維で作った研磨材不織布を利用し、各社それぞれ検討を行っています。
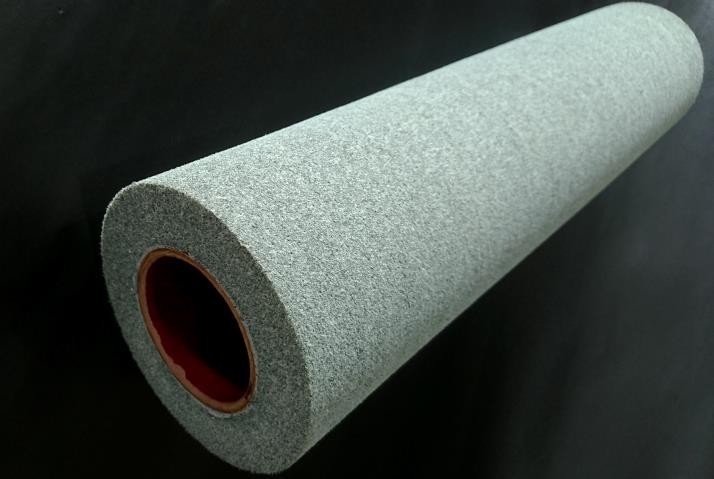
2つ目の方法ですが、そもそもこの分野では現在不織布製品が全体の大半を占めている状況です。最終仕上げに近い部分の研磨の為、砥石製品は向かず、ブラシ製品では研磨性が低く、ベルト製品はそもそも工程に向きません。
砥石製品がこの工程に向かない理由として、砥石の製法上、多くのPCB向け研磨材メーカーでは細粒度かつスクラッチ傷を入れない砥石を製造することが困難です。銅は非常に柔らかい金属の為目詰まりを非常に起こしやすい素材です。これが銅は削るのは簡単ですが難削材と言われる理由です。目詰まりを起こした部分は研磨性が無くなるため、ドレス作業(クリーニング作業)が必要となり、生産性が非常に悪くなります。
弊社ペレットタイプホイールは砥石製品と比較して非常に多様な形状・粒度・処方を選定することが可能です。このため、PCB向けの細粒度製品もラインナップしております。
3.面精度を出す
前述のようなパターンカット後の表面仕上げですが、一般的にRaで0.1μm程度に仕上げる場合が多くなっています。この後工程にはさらに層増しを行ったり、このためのフィルムを密着させたり、もしくはソルダーレジストを塗布したりといった複数の次工程があります。
次工程からすれば、パターン後研磨の工程は下地づくりともいえる工程です。どれだけ設計が良くても下地がガタガタだと設計通りに作ることは非常に困難です。特に基板の多層化が進んでいる現状では、層を何層も重ねるためには都度都度の下地作りが最も重要になっています。このため、高周波基板は現在、高平坦度を非常に重視した研磨を行っています。
多層化以外にも高平坦度の要求が非常に高い分野があります。パッケージ基板の分野です。パッケージ基板とは部品の中にある基板、と言えばよいでしょうか。実際の半導体を基板に乗せるための「ゲタ」のような役割をする基板です。半導体は昔はワイヤボンディングなど面―線―面でパッケージ基板と結合されていましたが、今やフリップチップボンディングなどの面―面結合が当然とされています(半導体の研磨に関しては弊社研磨加工部門にお問い合わせください)。
半導体表面は当然のことながら平坦ですが、PCBにも平坦性がより必要とされるようになっています。ワイヤボンディングであれば少々平坦に問題があっても対応可能でしたが面―面でのボンディングになると正確なパターン形成や、平坦度が必要となります。
弊社製品、特にペレットタイプ製品では業界でも非常に特殊な構造を持っており、一段階上の平坦度をご提供できる製品となっております。平坦度に問題がある場合にはぜひご相談をよろしくお願いいたします。