ステンレスパイプ(以下、SUS管)の研磨というと、まず溶接個所のバリ取り研磨を想像する方が多いのではないでしょうか。確かにバリ取り研磨も重要な研磨作業ではありますが、それだけではありません。SUS管製造工場の各工程において研磨材がどういった用途、方法で使用されているのか、私の調査した製造現場の例を挙げながらSUS管の研磨について解説します。
SUS管とは
SUS管は非常に汎用性の高い部材です。身近なところでは物干し竿やコンビニの駐車場の車止め、車のマフラーや電車やバスの手すりなどから、普段は目にしない建築構造材や工場プラントの配管設備まで、私たちの生活のさまざまな場所で使われています。
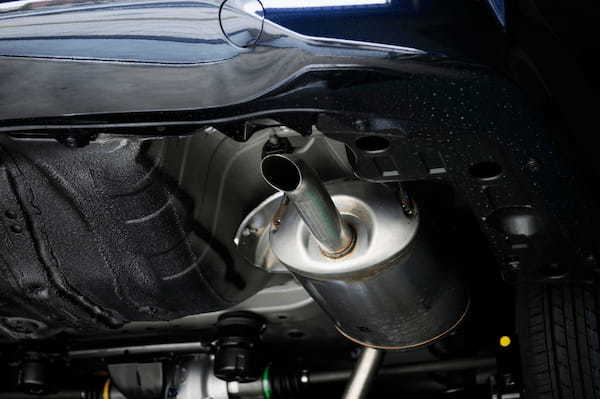
その材料であるステンレス鋼は英語で『stainless steel』といい、直訳すると『錆びて汚れない(stainless)鋼(steel)』を意味します。ステンレス鋼はこの言葉の意味通り、錆びや汚れに非常に強い鋼です。耐蝕性を改善向上させるため、鉄(Fe)にクロム(Cr)またはニッケル(Ni)を添加することにより不動態皮膜を生成させて耐蝕性を大幅に向上させた合金鋼です。一般的には、クロム含有量が約10.5%以上の鋼を総称してステンレス鋼と呼んでいます。
ステンレス鋼は単に『ステンレス』と呼ばれることが多いですが、さらに略して『ステン』とか、ステンレス鋼の記号の頭の『SUS』などと呼ばれたりもします。
SUS管製造で研磨が必要なライン3種類
SUS管製造工場において研磨が必要なラインは、おおまかに次の3種類に分けることができます。
① 造管ライン(大径管、中径管、小径管の製造)
② 異形管加工ライン(角管、フラットバー、その他異形管への加工)
③ 装飾管加工ライン(ヘアライン、鏡面加工)
①の造管ラインですが、その名のとおりSUSの薄板を丸型のパイプ形状へ成形するラインです。ここで成形されたSUS管はそのまま半製品や部材として出荷されるものもあります。②と③は、①の造管ラインで成形されたSUS管に付加価値を高めるための加工を行うラインです。
ちなみにSUS部材は、SUS304・316に代表されるオーステナイト系とSUS409・436のフェライト系に大別されており、硬度、靱性、耐熱性、耐蝕性、価格などがそれぞれ異なります。研磨という概念で見た際には、オーステナイト系は硬度が高く研磨性が悪い傾向、フェライト系は前者より柔らかいが目詰まりしやすい性質を持ちます。 それでは、順を追って各ラインの研磨を説明していきます。
① 造管ラインフローチャート
原反(SUS圧延鋼板)→フォーミング(成形)→高周波誘導溶接→冷却→溶接ビード研磨→洗浄 →サイジング(寸法矯正)→検査(渦電流探傷試験)→切断・面取り→検品→出荷
〔造管サイズ〕
・全て丸管 外径6m/m~450m/m 厚み0.3~9mm
〔使用研磨材〕
・NPホイール #320 355x30x220mm 回転速度2400~2900M/分
・研磨布ベルト #180 200x3120mm
〔研磨方式〕
・研磨液による湿式研磨
〔ラインスピード〕
・3M~60M/分 SUS管の径と厚みにより変動
〔設定負荷〕
・5~10A
ここでの研磨のメインは、溶接ビードの除去、外観整形です。薄板状態のSUSをロール形状の金型で円筒状に成形していき、その合わせ面を電気溶接した後にできる高さ1mm以下のビードをNPホイールと呼ばれるフラップ形状の研磨輪によって除去します。
電気溶接によって非常に高温となったSUS管を冷却溶液にて冷却する過程に湿式の研磨機が設置されており、研磨ホイール2ヘッド、研磨布ベルト2ヘッドの研磨プロセスがあります。ただし、直径25.4m/m以下の小径管についてはベルト研磨のみとなります。
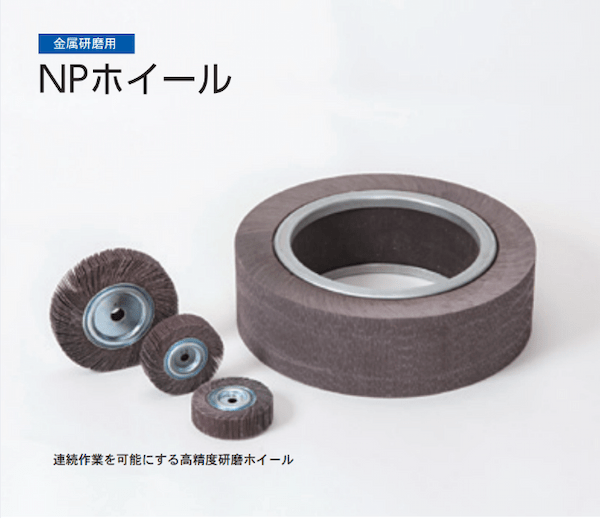
SUS管に対して研磨輪を45~60°の角度をつけて、しかも2ヘッドの回転方向は互いに逆の方向へ回転させていることが大きなポイントです。この角度により2~10mmというSUS管の直径によって変わるビード幅に対して研磨輪が最適な接触となり効率よくビードを削り取ってゆきます。
また、それ以外にもこの研磨輪には特殊な仕様が施されています。羽根基材の巻き癖を抑制することによって研磨輪の外径を均一化する処方で、研磨の安定性に重要な役割を果たしています。そして逆回転にすることで研磨キズを消しあい、仕上げ面の向上を図っています。
次はベルト研磨工程となりますが、ポイントとしてはこちらも研磨輪と同じようにSUS管に対して60°の角度をつけている点と、最初のヘッドに新品のベルトを使い2個目のヘッドに使い古しのベルトを使用している点で、粒度を細かくするよりも研磨性、仕上げのバランスが良好とのデーター評価を得ています。
② 異形管加工ラインフローチャート
造管の検品済み品 → フォーミング → 冷却 → サイジング → 検品 → 外観研磨 → 洗浄 → 検品・包装 → 出荷 → 洗浄 → 検品 → 出荷
〔加工サイズ〕
・角型パイプ換算7x7mm~200x300mm 厚み0.8~9mm
〔使用研磨材〕
・NPホイール #80 355x(25~50)x170mm
・NPホイール(木管)#80/#100 355x(10~20)x220x38.1mm
〔研磨方式〕
・乾式・湿式
〔ラインスピード〕
・成形時3~25M/分
・研磨加工時8M~10M/分
〔研磨輪回転スピード〕
・2000~2800M/分
〔設定負荷〕
・7~10A
次に異形管加工ラインですが、異形管とは言うものの形状は四角形断面の角管が大半を占めます。造管ラインから上がってきたSUS丸管を角管用の金型が設置されたラインへ流すことにより成形しますが、フェンスや橋の欄干に多用される細幅の角管は見た目の品質も重要なため、外観向上のための研磨工程が追加されます。
この際、角管は角があるため回転させることができず、『転がす』というアクションが使えないため自動化が困難です。SUS管を回転できないデメリットは研磨においても大きく影響します。具体的には以下のようなデメリットが挙げられます。
- 4面を研磨するために上下左右、最低でも4ヘッドの研磨輪を用意する必要がある
- 角管は研磨輪が点ではなく面接触となるため研磨熱による温度上昇が顕著
- 回転による放熱が無いため研磨熱がこもりやすく変形やひずみによる不良率が高い
上記に加え、数種類の幅に対応するために研磨輪の幅もそれぞれ用意する必要があり、コスト的にも負担が増加します。
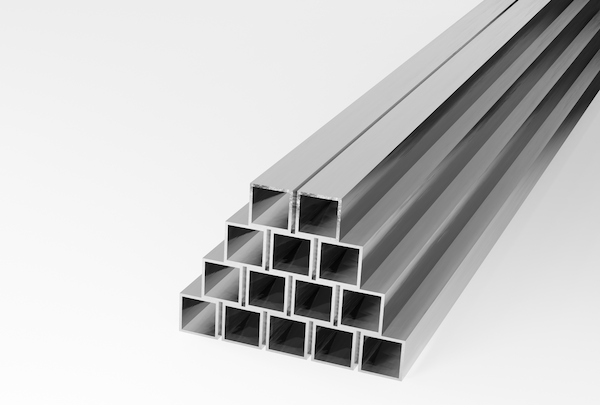
今回の製造現場では、研磨機は4ヘッド仕様となっており、1ライン当たり2機の研磨機が設置されています。要求される品質とSUS素材の種類や厚みによって、1機だけ通るものと2機とも通るものに分類されます。
バリ取り研磨と違って研磨輪はSUS管の面に対して接触するように進行方向へ向かって設置されており、回転もすべて進行方向に対して順回転となります。そして、珍しいのは同じ研磨機で乾式も湿式も兼用しているという点です。素材によって使い分けがされており、オーステナイト系SUSは耐蝕性が極めて高いので安定した研磨ができる湿式、SUSの中でもクロムとニッケルの含有量の少ないフェライト系は腐蝕に対して比較的弱いため乾式を選択しています。
研磨輪においても湿式はすべて金具式のNPKタイプで、羽根基材も柔軟性と仕上げの良好なSRAJ研磨布で統一されています。乾式については膨張するため水分には弱いが、熱伝導性の少ない木管式のNPWタイプ、羽根基材は乾式の負荷に負けないようWRAX S-23研磨布が採用されています。
③装飾管加工ラインフローチャート
造管の検品済み品→外観研磨→洗浄→検品・包装→出荷
〔加工サイズ〕
・全て丸管 外径5m/m~160m/m 厚み0.8~3mm
〔使用研磨材〕
・NPホイール #80~#400 355x100x220mm 回転速度1800~2700M/分
・サイザルバフ イエロー 350x100x175mm
〔ラインスピード〕
・鏡面加工時1M~6M/分
ヘアライン加工時1M~6M/分
〔研磨輪回転スピード〕
・鏡面加工時2500~2800M/分
ヘアライン加工時1700~2200/M
〔パイプ回転数〕
・鏡面加工時30~250rpm
・ヘアライン加工時15~130rpm
〔設定負荷〕
・鏡面加工時9~12A
・ヘアライン加工時1~3A
最後に装飾管加工ラインとなりますが、このラインは前述の2つのラインとは違い成形の工程がなく、研磨作業が工程の大半を占めます。SUS管の外面を研磨することにより、外観品質を高めた高付加価値管を造ります。大きく分けてヘアラインと鏡面(ミラー)加工の2種類の加飾があります。
鏡面加工工程
まず鏡面加工とは、文字通りSUS管を鏡のように磨き上げる工程です。研磨機は5ヘッドで構成されており、研磨輪をSUS管の上から圧着させるタイプです。以下の流れで研磨輪とバフが配置されます。
#240 ⇒ #320 ⇒ #400 ⇒ バフ ⇒ バフ
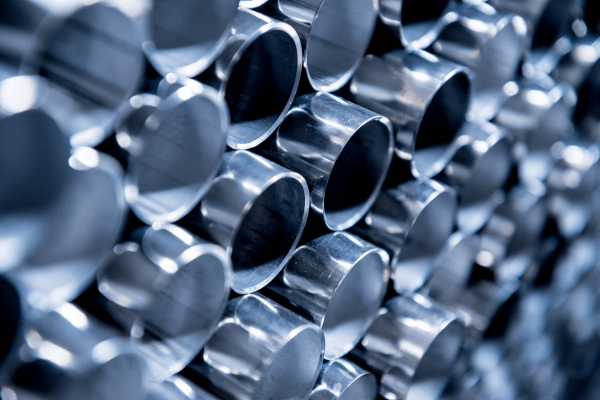
基本的に形状は丸管のみのため、角管研磨では使えなかったSUS管を回転させながらの研磨が行われます。これにより、1ヘッド単位でパイプ全周の研磨が可能となっています。大径のSUS管研磨に対応するために研磨輪も100mm幅のタイプが使われ、点接触による偏摩耗を防ぐためにヘッドがオシレーションするようになっています。
SUS管の直径によって送り回転数は異なりますが(同じ設定スピードでも径が大きくなると管の回転数は少なくなる)、標準的な直径25.4m/mのSUS管で130rpm程度となります。また、研磨輪とバフの回転数と負荷はかなり高く設定され、ある程度の研磨熱を高めることにより、その熱によって光沢を出していく手法をとっています。
ヘアライン工程
次にヘアライン加工についてご説明します。ヘアライン加工は、鏡面加工よりも難度の高い工程です。鏡面加工は最終的にバフを使って研磨目を消してしまうため、研磨輪の段階での仕上げに対してはそれなりの許容範囲がありますが、ヘアラインは研磨目自体が仕上げの外観になるため、ごまかしがきかず要求品質が高いのです。ヘアラインの細かさによって以下のA・B・C・D 4種類の仕上げに分けられます。
A. #80
B. #80 ⇒ #180
C. #80 ⇒ #180 ⇒ #240
D. #80 ⇒ #180 ⇒ #240 ⇒ #320
研磨機は4ヘッドで基本はDの粒度配置で並べられており、Bの仕上げの場合は、#240と#320の研磨輪を休止させるといった使い方をしています。ヘッドの数が違うだけで基本的には鏡面加工と同じタイプの研磨装置ですが、ヘアライン工程独自の設定も多いです。
特に設定負荷は低く抑えられ、#80に至っては1Aをきるぐらいの撫でる程度の研磨となります。研磨輪、およびパイプの回転数もへアラインの方向性に乱れが生じないように低めとなります。また、ヘッドとヘッドの間に矯正ローラーを配置し、パイプの真直度を高めながら研磨を行うことにより、非常に安定した方向性のヘアラインを加工することが可能となっています。
研磨輪に対する品質要求も高く、特にバランス不良による研磨輪のビビリはヘアラインの美観に大きく影響するため、このラインに納入しているNPホイールはすべて、ウエイトによるバランス調整を念入りに行っています。
まとめ
ここまで、SUS管製造工場における代表的な研磨を紹介してきました。実際にはまだまだSUS以外のチタンや複合材といった別素材、特殊な形状をもった特注管も多数製作されており、それらの研磨については未だ調査途上の段階です。溶接方法においても主流だった高周波誘導溶接に替わってレーザー溶接造管機が一部導入されてきたことにより、ラインスピードがこれまで以上に高速化してきており、現行の研磨の形態も少なからず変化してきています。
また、グローバル化による製造現場の海外展開、需要動向、物流、為替相場の動向はコスト管理を大いに悩ませます。こういった市場の流れに対していかに対処し、拡販と提案に努めていくか、今後も情報収集と現場調査を進め、先手の営業を心掛けてまいります。